The Importance of Poka Yoke Verification
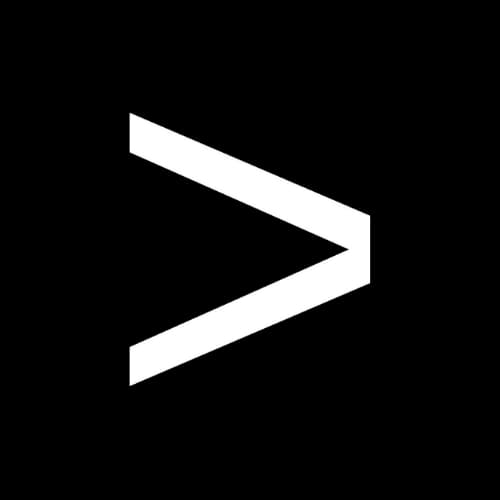

Imagine a plant facing customer complaints over failed parts, a problem traced back to a metal clip missing on a plastic part.
As a result, the team adds a proximity sensor to a machine as a poka yoke or mistake-proofing device to check that all parts have the required metal clip. They install the sensor and check that it works the first day, and feel confident knowing that any nonconforming parts will be immediately detected.
Operators soon realize, however, that a foil wrapper stuffed in the sensor fixture makes the machine pass every part, leading to more complaints and headaches for the company.
This scenario highlights one critical step in using poka yokes to prevent manufacturing failures: verification.
Below, we take a closer look at poka yoke verification, including two essential elements you must verify for poka yoke to be effective.
Download your free Root Cause Analysis 101 Guidebook for a 38-page rundown on 5 common root cause analysis tools
Poka Yoke Basics
In manufacturing, a poka yoke (or “error-proofing” in Japanese) is any device or mechanism used to prevent errors or mistakes in the process. Poka yokes fall into two broad categories: error-proofing and mistake-proofing.
An error-proofing poka yoke makes it impossible to execute a step incorrectly, whereas a mistake-proofing poka yoke keeps errors from being passed on to the next workstation. Each of these categories utilizes different poka yoke principles, as shown in the table below.
Error-proofing |
Mistake-proofing |
Elimination
Remove the step or part altogether |
Detection
Make it easy to see when a step has been performed incorrectly |
Prevention
Design the part so it can’t be assembled incorrectly |
Mitigation
Reduce the impact of potential nonconformances |
Replacement
Design parts so they can’t be mixed up, forgotten or misoriented |
|
Facilitation
Make the right step the easiest and safest choice |
Why Verification Matters
Poka yoke is a powerful tool for error-proofing your processes, with one key caveat: poka yokes must work as expected.
Imagine, for instance, you spend weeks or more adding a complex poka yoke system in a machine, only to discover it’s not working after customers receive bad parts. In this case, the poka yoke only provided a false sense of security, since you had no safeguard in place to verify its effectiveness.
A red rabbit is the most common strategy used to verify that a poka yoke is working. A red rabbit test involves running a known defective part through a machine to see if it rejects the part. From there, any SOP or work instruction should clearly state when the operator is to perform the red rabbit test, such as at the beginning of each shift.
Even this, however, still relies on human behavior, and as such requires an additional level of verification. That means incorporating red rabbit tests into process checks such as layered process audits, which allows you to verify that both the poka yoke is working and that it’s being tested regularly.
Adding Poka Yoke Verification to Plant Floor Checklists
When adding poka yoke verification to plant floor checks like layered process audits, it’s worth thinking about how you’ll design your checklist questions. To verify that the poka yoke is functioning and the operator knows how to run the red rabbit, your checklist question might say:
Can the operator demonstrate how to use the red rabbit, and does the machine reject the part?
Using plant floor audit software like EASE helps go one step further by allowing you to:
- Create a new question category or tag for error-proofing or poka yoke
- Rotate error-proofing questions into audit checklists so you can be sure they’re being checked regularly
- Track trends on where and when error-proofing failures are occurring
When Poka Yoke Verification Gets Complicated
Testing poka yokes isn’t always straightforward. In some situations, poka yoke verification can become quite complex, such as if a machine contains multiple poka yokes. For example, if your equipment has 12 poka yoke sensors on it, how do you test them all, and how do you pinpoint which specific one(s) aren’t working in the event of failure?
Addressing these questions requires careful forethought and planning. In the example above, you might group the sensors geographically, with four sensors each in the left, middle and right groups. Here, if you get a failure in the right grouping, that provides a smaller area where you’ll need to check specific parts.
Poka yokes act as a vital safeguard against defects and safety problems. At the same time, poka yokes themselves can break down, or people can find workarounds for them. Establishing processes for verification, such as red rabbit testing and layered process audits, builds in an added level of security, which is crucial if you rely on poka yokes for protection against failures.