Process and Skills Verifications: Why Product Inspections are not Enough
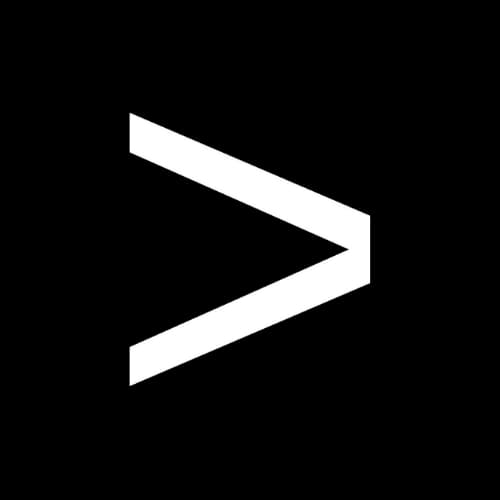
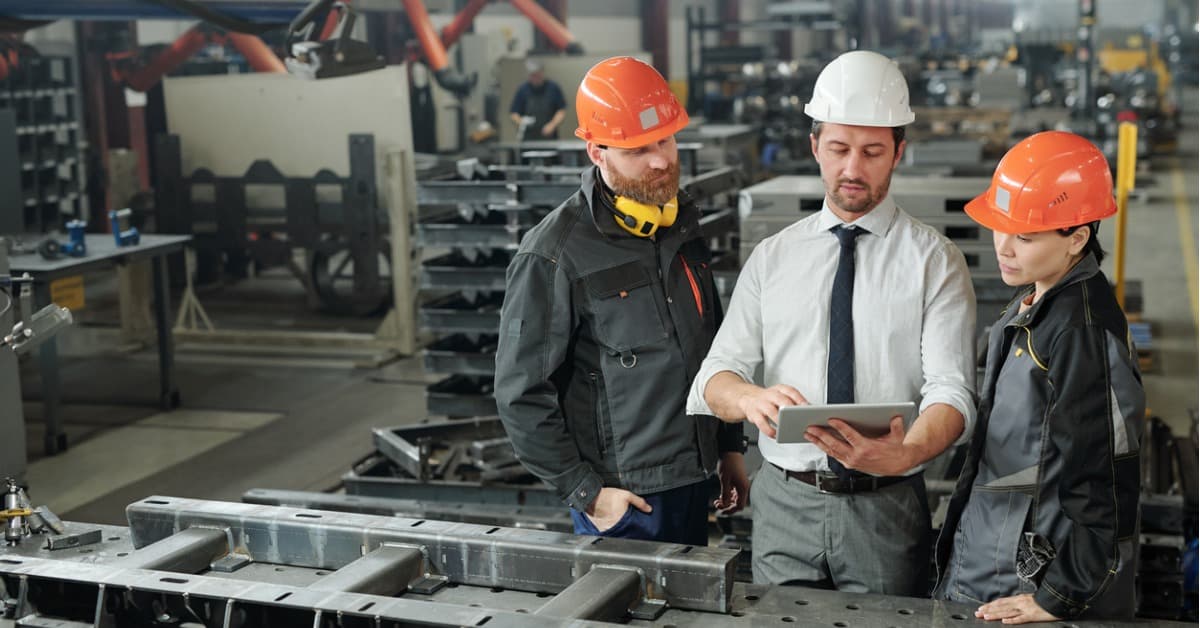
Product inspections are vital to quality control, helping manufacturers identify bad parts before they leave the plant. At the same time, inspections aren’t always enough to stop bad parts from reaching the customer.
Verifying processes and skills, on the other hand, addresses several shortcomings of product inspections, acting as a high-leverage strategy for pushing down defects and costs.
Below we examine key shortfalls of product inspections, as well as how process and skills verifications prevent quality escapes and accelerate continuous improvement.
Download your free Ultimate Guide to Layered Process Audits to learn more about preventing defects with process verification
Shortfalls of Product Inspections
Thinking that product inspections will catch defective products can provide a false sense of security, but the truth is inspections only go so far. One main concern is that while inspections may find individual defects, they don’t deal with the underlying problem: the manufacturing process itself.
Then there’s the fact that inspectors may not catch certain defects if they aren’t immediately visible. Some defects may not be visible at all, such as latent defects arising from structural weaknesses or material issues. Finally, sampling bias can mean that the inspected products aren’t representative of the entire batch, with other defects going undetected.
One unintended consequence of overreliance on product inspections to catch defects is the sheer inefficiency of this approach. When a bad product is identified, that kicks off a sequence of actions that eat up valuable time and resources, including:
- Sorting and isolating affected product
- Conducting root cause analysis investigations
- Implementing, reviewing, and verifying corrective actions
The downhill—and often unmeasured—impact of this is loss of productivity and profitability as resources are tied up dealing with defects rather than making revenue-generating products. And that’s if you’re lucky enough to catch the defects before they leave your facility. Should they become external defects, the costs go up exponentially, both in terms of financial and reputational impact.
Verifying Your Processes
Process verification addresses many of the shortcomings of product inspection, also giving manufacturers valuable data they can use to support continuous improvement efforts.
Process verification techniques such as layered process audits allow plants to:
- Ensure process inputs comply with work standards
- Identify sources of variation that lead to defects
- Prevent defects at the source rather than after products are made
- Minimize time and materials used for correcting problems
- Generate data that can be used to increase efficiency and improve processes
Another major advantage of process verification is that it involves direct observation of processes. This provides more opportunities for engagement between management and operators, fostering a culture of quality and communication.
Sources of Variation to Check
When we talk about potential sources of variation to check with process audits, one place manufacturers should start is with the 6Ms of process control.
What are the 6Ms of Process Control?
- Man (People): Operator behavior, skills, conformance to standard work and safety requirements, etc.
- Machine: Includes equipment settings and condition
- Method: Whether the correct method version is being followed, e.g. when switching between two methods for two customers on a similar process
- Mother Nature (Environment): I.e. temperature, humidity, storage, and warehousing conditions
- Material: Usually labeling or supplier quality issues
- Measurement: Part orientation, gauging, measurement techniques, condition of measurement tools, etc.
All of these represent manufacturing process inputs where verification on the plant floor can prevent production defects. The first category refers to variation in operator behavior and is particularly important to verify on the plant floor. This variation naturally happens over time as people become more familiar with—and pay less attention to—processes. It also applies to variation among different individuals, which can arise due to a variety of reasons, including different skill sets.
Skills Verification
Verifying operator skills and qualifications is an important part of minimizing variation due to human behavior. During process audits, consider asking questions such as:
- Can the operator explain the most important step in the process?
- Can the operator demonstrate the key job step according to the work standard?
- Can the operator tell you why this particular step is important to quality?
You may also want to include questions related to craftsmanship relevant to the work process in question. For instance, if a blow molding press operator must scrape flash off of a part within 0.3 mm, you might include a question to have them demonstrate this.
Product inspections are an essential part of quality control, but they aren’t everything. If you’re not also verifying processes and skills, you’re rolling the dice on potential quality escapes. Identifying sources of variation in the process, particularly operator skills and behaviors, represents a low-cost, high-payoff method for reducing production defects compared with product inspections.