Using a QMS Tool: Benefits, Examples and Solution Selection
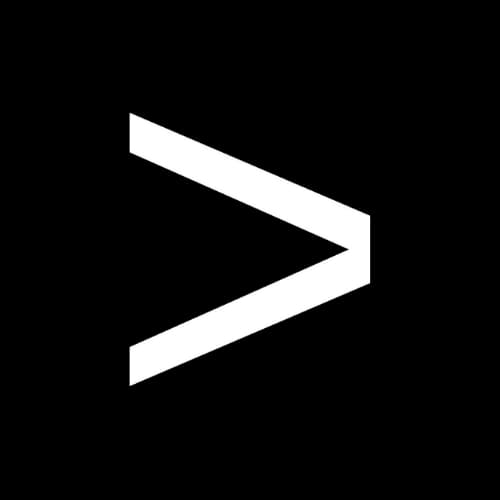
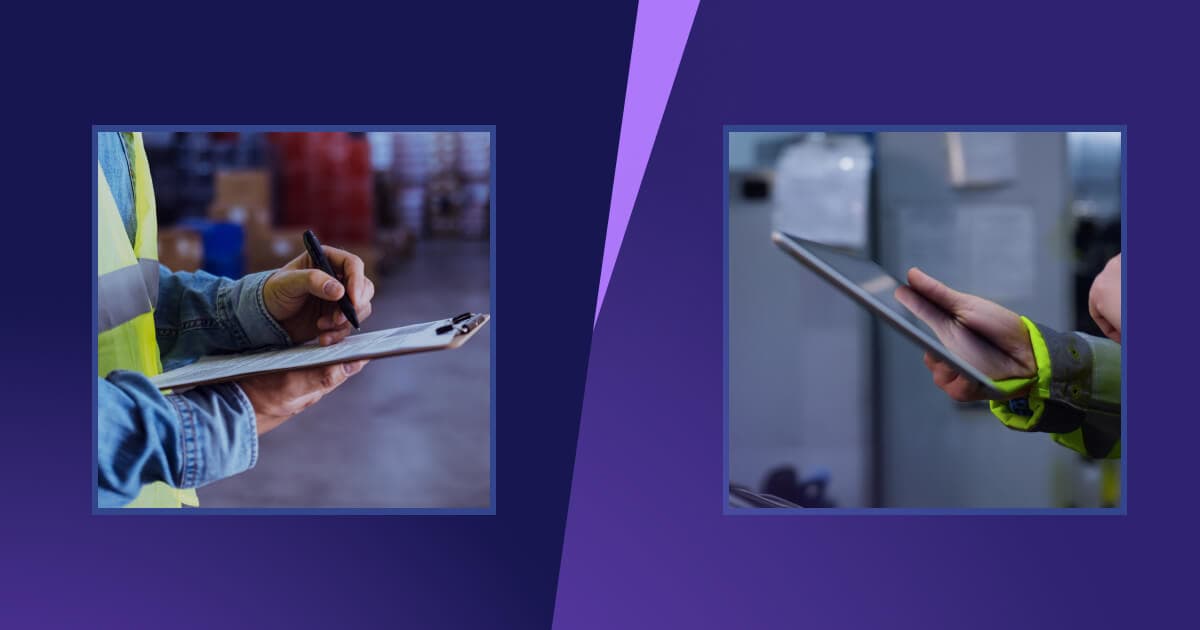
In today’s rapidly evolving manufacturing environment, managing quality effectively can mean the difference between market leadership and a company that makes headlines for all the wrong reasons.
Quality management system (QMS) tools play a key role in this, with automation acting as a catalyst for closing loops in the quality process.
On the road of quality, a paper-based QMS tool is like using a physical map: it might get you there, but there’s the potential for many wrong turns along the way.
Quality 4.0, a concept introduced by LNS Research, on the other hand, is like GPS, offering real-time updates and proactive issue identification. Quality 4.0 applies emerging technologies like digital QMS tools to transform quality management across the entire value chain, building upon traditional quality methods.
This article explores how the use of digital QMS tools can improve the manufacturing process, including:
- What is a QMS, core elements and benefits
- How a QMS aligns with the Plan-Do-Check-Act process
- QMS regulations and standards
- Point solutions vs. enterprise QMS (eQMS)
Download your free Root Cause Analysis 101 Guidebook for tips on using the most common root cause analysis tools
What is a Quality Management System (QMS)?
A QMS is a system of processes that ensures products consistently meet customer expectations and comply with regulatory standards, while contributing to overall operational efficiency. Whether paper-based or digital, a QMS encompasses all activities designed to ensure products meet quality standards, including:
- Quality Planning: Establishing objectives and specifying necessary processes
- Quality Control: Implementing operational techniques to fulfill quality requirements
- Quality Assurance: Providing confidence that products and processes will meet quality requirements
- Quality Improvement: Ongoing efforts to enhance product and process quality
Core Elements of a QMS
A QMS may include a wide range of processes depending on the nature of the manufacturing process. At the core of the QMS are elements such as documentation, employee training, audits and corrective action:
- Documentation of processes, procedures, SOPs and specifications forms the foundation of the QMS. These are the standards against which manufacturers must gauge compliance. In essence, this is the “say what you do” step.
- Employee training: Well-defined processes don’t mean anything unless your workforce has the knowledge and skills to execute them correctly. Employee training must be a dynamic process, where workers are supported not just with classroom and computer training, but also on-the-job training and skills reinforcement.
- Audits: This is where you verify that you “do what you say.” Plant floor audits and inspections look at plant floor practices and compare them against your documentation.
- Corrective action: Corrective and preventive action (CAPA) is the mechanism for making adjustments that move the continuous improvement process forward.
Together, these basic functions support the Plan-Do-Check-Act (PDCA) cycle.
QMS Software in the Context of Plan-Do-Check-Act
The PDCA cycle, also known as the Deming cycle, is a fundamental concept in quality management for driving continuous improvement. Let’s break how this cycle works in the context of the QMS:
- Plan: In this phase, manufacturers document their SOPs as well as identify quality issues or improvement opportunities. They set objectives, analyze data, and develop action plans.
- Do: This is where the plan is implemented, which may involve activities like rolling out updated SOPs, employee training or executing continuous improvement projects.
- Check: After implementation, the results are monitored and measured, an area where plant floor audits play a crucial role. Quality leaders must assess whether SOPs are being followed, and whether any changes have the desired effect.
- Act: Based on the results observed in the Check phase, manufacturers must then make adjustments, often using tools like corrective action. If the changes are successful, they can be standardized and applied to other areas. If not, the cycle begins again with a new plan.
Manufacturers can create a continuous improvement loop by leveraging digital tools to support the PDCA cycle, constantly refining and optimizing their processes for better quality outcomes.
Improve your plan floor quality and safety using our 5S Audit Checklist
QMS Regulations and Standards
Food and beverage, medical device and pharmaceutical manufacturers are required to have a QMS that complies with federal regulations specific to those industries, such as:
- Quality Management System Regulation (QMSR) for medical devices (21 CFR Part 820)
- Good manufacturing practice (GMP) regulations for pharmaceuticals (21 CFR Part 210 and 211)
- Current good manufacturing practice (cGMP), hazard analysis and risk-based preventive controls for food (21 CFR Part 117)
Implementing a QMS is best practice in any industry, and many suppliers are required to have one to secure business contracts.
Several standards have been developed to guide manufacturers in creating a QMS. While ISO 9001 is the most recognized global standard, many sectors have developed their own specialized standards, including:
- IATF 16949 for automotive manufacturing quality
- AS9100 for aerospace manufacturing quality
- ISO 22000 for food and beverage manufacturing
- ISO 13485 for medical device quality
Complying with or certifying to these standards demonstrate a manufacturer’s commitment to quality and continuous improvement.
What ISO 9001 Requires in a QMS
ISO 9001 is widely recognized as the gold standard in quality management processes, and certification to the standard is required of suppliers to many OEMs. ISO 9001 doesn’t prescribe specific methods that manufacturers must use in creating their QMS, nor does it require them to use automated QMS tools.
Rather, it defines the processes that must be in place and documented to achieve compliance. In other words, ISO 9001 shows you the destination—it’s up to you how you get there.
ISO 9001 compliance emphasizes several core areas:
- Leadership: Leadership commitment is vital to any quality effort, and the standard underscores the need for management to be involved in the process to provide team accountability.
- Planning: Organizations must define their processes and procedures, as well as set objectives against which they will measure their progress towards continuous improvement.
- Support: Documentation and employee training are central to driving awareness and competence among the workforce.
- Operation: ISO 9001 also includes operational considerations such as determining requirements, designing products, addressing nonconformances and working with third parties.
- Performance Evaluation: The standard emphasizes ongoing monitoring as well as internal audits and regular management reviews to ensure the organization is progressing toward its goals.
- Improvement: Corrective action is an essential tool in the pursuit of continuous improvement.
Drawbacks of Using Manual Quality Management Tools
Traditionally, manufacturers have created their QMS around paper-based systems and/or spreadsheets. Adoption of QMS software is growing, but some companies still perceive manual systems as sufficient to meet their needs, and advantageous in terms of their simplicity and cost. In reality, manual systems come with inherent limitations that often hinder effective quality management in that they are:
- Time-intensive: Manual data entry and report generation cause delays in addressing quality issues while driving up administrative costs. Reporting lag time can also allow problems to grow in scope and impact before they are fully addressed.
- Error-prone: Handwritten records and manual data transfer increase the risk of mistakes. Versioning errors are also a risk when using shared server drives or sharing documents via email.
- Low visibility: Paper systems hinder real-time oversight and access to historical data. These systems make it hard to identify where problems are occurring, as well as lessons learned from similar issues that have occurred in the past, resulting in duplicate effort and ineffective solutions.
- Complex to report on: Identifying patterns or recurring issues over time is challenging, requiring significant input of manual labor hours to validate and process data.
- Inconsistently executed: Lack of standardization leads to variation in the manufacturing process—the very opposite of what process excellence frameworks like Lean are trying to achieve.
Benefits of Using a QMS Tool
Digital QMS tools have revolutionized quality management, addressing the limitations of manual processes while providing a competitive advantage to those manufacturers that pursue automation.
They help protect organizations by protecting the company from productivity losses due to inefficiency as well as helping bolster their competitive positioning. In a recent global survey, for example, Deloitte found that 56% of executives prioritize Industry 4.0 investments to protect their organizations from disruption by competitors.
At the same time, QMS tools can help companies become market disruptors by enabling new ways of working and decision-making. They provide real-time data and insights that weren’t previously available, allowing for more agile and responsive manufacturing processes.
These modern solutions enhance various aspects of the quality process by improving:
- Efficiency and accuracy: Eliminating manual data entry streamlines processes and reduces errors, while also saving hours of administrative time.
- Real-time insights: Instant access to information like audit and inspection findings and real-time alerts for critical issues enable swift decision-making and immediate action. This allows for prompt corrective actions, preventing minor issues from escalating into major problems.
- Visibility and analysis: Custom dashboards and automated trend analysis provide deep insights into quality performance to facilitate continuous improvement and proactive identification of systemic issues.
- Standardization and consistency: Implementing automated quality processes helps maintain uniform quality across different production lines, shifts or facilities.
- Improved collaboration: The ability to easily share results with leadership and other departments helps down silos and promote an organization-wide focus on quality.
- Traceability and compliance: Automated QMS tools ensure accountability and regulatory compliance by centralizing quality records for better tracking and tracing.
What Is an eQMS?
Companies looking to automate their quality processes need to consider whether they will implement an enterprise quality management system (eQMS) and/or use point solutions focused on specific processes.
An eQMS typically offers a wide range of individual solutions either packaged as a whole or purchased in bundles. It may also include modules designed for a specific industry, such as medical devices.
eQMS Solution | Function |
Document management | · Centralize documentation · Ensure processes and SOPs are up-to-date · Revision control |
Employee training | · Identify training gaps · Track training compliance · Provide on-the-job support |
Audits and inspections | · Centralize checklists · Track findings |
Corrective and preventive action (CAPA) | · Assign action items · Track issues to closure · May incorporate root cause analysis tools like 5 Whys or 8D |
Risk management | · Mitigate design and production risks · May incorporate tools like failure mode and effects analysis (FMEA) |
Change management | · Assess risk of changes to processes, equipment or people · Streamline change with minimal disruption |
Nonconformance and deviation tracking | · Collect data on nonconformances and deviations · Track investigation and issue resolution |
Supplier management | · Monitor supplier compliance · Track supplier corrective action requests (SCARs) |
Learn common misconceptions around quality costs and how manufacturers can use the 1-10-100 rule to push down cost of quality.
Using an eQMS vs. Specialized Point Solutions
An eQMS provides a unified approach to quality process automation, but these systems often require significant investment in cost, implementation time and staff training.
Some organizations choose to implement an eQMS and then must heavily customize different solutions to their needs. Others may choose to integrate the QMS with point solutions that provide specialized functionality for a given process.
While a single QMS software package may seem attractive on the surface, the reality of digital transformation is that no single solution will do everything you need. The leading thought process in smart factories today is to focus on cultivating an ecosystem of tools that help you meet your requirements and goals.
Your ultimate priority: getting the right information to the right people at the right time, with no bottlenecks in the process.
This is the idea behind emerging connected worker strategies, which aim to bridge the growing disconnect between people, information and systems as a result of process digitization.
Deploying a Specialized Point Solution
One example of the above strategy would be using plant floor audit software with a dedicated mobile app for audits and inspections on the manufacturing floor..This type of solution can then be integrated with other systems such as business intelligence reporting or eQMS platforms that may have limited capabilities around plant floor audits.
This type of A specialized plant floor audit solution goes beyond what eQMS audit modules typically provide by allowsing manufacturers to:
- Schedule a large volume of audits to account for shifting schedules
- Build dynamic checklist libraries with advanced functionality such as photo uploads, conditional questions and question tagging
- Conduct plant floor checks with an intuitive mobile app
- Document conditions on the plant floor to aid in root cause analysis
- Easily update audit and inspection checklists
- Instantly get findings on plant floor nonconformances presented in graphical format
- Follow-up on findings to close the loop on corrections
Compared with rolling out this process via an eQMS, these tools offer a more agile approach with lower initial costs, faster implementation and easier adoption. A digital audit solution built for mobile devices, for example, is typically far easier to use than trying to pull up the web version of an eQMS audit management module on the plant floor.
Thus, companies that need to perform frequent checks or drive defect rates down quickly may benefit more from a specialized audit solution than simply relying on eQMS audit tools.
The Strategic Impact of QMS Tools: Real-World Digital Audit Examples
Numerous automotive suppliers are subject to IATF 16949 customer-specific requirements around layered process audits, which involve checking high-value process inputs daily. These manufacturers often struggle to achieve value from these plant floor checks due to the administrative effort involved, but cloud-based audit platforms are changing the equation. Find our layered process audit checklist here.
With these tools, companies like Dana have been able to reduce internal PPMs by 47%, a number that’s not uncommon among other organizations that deploy EASE.
Beyond just the hard metrics, this type of platform can have a strategic impact on an organization’s ability to prevent, detect and respond to systemic quality risks effectively.
Like many companies that conduct frequent process checks, a large tire manufacturer was facing challenges with data entry, checklist distribution, timely data analysis and efficient issue mitigation.
After implementing the EASE audit platform, the manufacturer was able to perform over 200 audits weekly, close out mitigations faster and gain real-time visibility into plant floor processes.
Most notably, the digital platform enabled them to develop an innovative strategy using dynamic question banks to identify systemic issues across the plant quickly. This approach led to the discovery of quality issues that might not otherwise been identified, potentially preventing costly quality escapes.
The shift to digital also allowed for scalability and data-driven decision-making that was impossible with paper systems. As the company’s director of quality emphasized, it would have been impossible to manage thousands of audits with a paper system, let alone harness valuable data from them.
Being able to schedule, conduct and report on audits digitally was the key to eliminating constraints in the process. This case demonstrates how digital QMS tools like layered process audit software can overcome the limitations of paper-based systems to drive improvements in quality and efficiency.
How to Evaluate QMS Tools
Whether you’re looking at a specific point solution or an eQMS, there are several critical factors to consider as part of your decision-making process:
- Usability: Implementing tools that are intuitive and easy to use minimizes training difficulties and promotes user adoption—a critical element of success for any software implementation.
- Scalability: You want to make sure that any solution you implement can grow with your operations, which is one main reason why companies choose cloud-based tools
- Integration capabilities: Look for solutions that can connect with other critical systems such as manufacturing systems and business intelligence tools.
- Mobile access: Quality isn’t just something that happens behind a desk. The ability to use QMS applications on the plant floor enables real-time data collection and communication.
- Reporting: Look for advanced analytics that turn quality data into actionable insights, with custom dashboards so you can keep your most important metrics front and center.
- Flexibility: A flexible system allows you to adapt the tool to your existing processes rather than forcing you to change established procedures. This preserves operational efficiency and reduces implementation time and costs.
A multitude of QMS tools exist on the market today that can help companies advance their digital transformation and quality goals. Any solution you choose will be unique to your business needs and requirements, whether it’s an eQMS solution or augmenting your current QMS with specialized tools. What’s crucial is finding user-friendly solutions that deliver data-driven insights, which will improve user adoption and deliver better results on the whole.