Lessons from the 3 Biggest Recalls in History
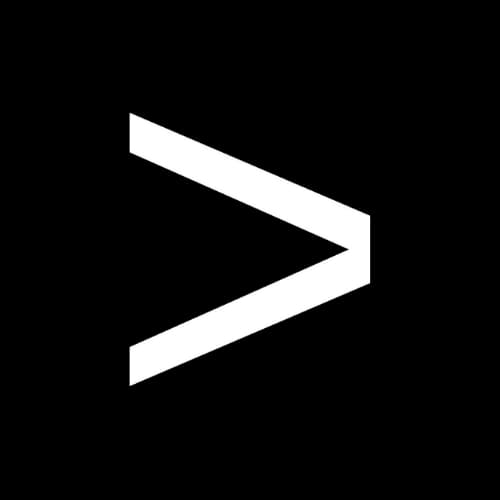
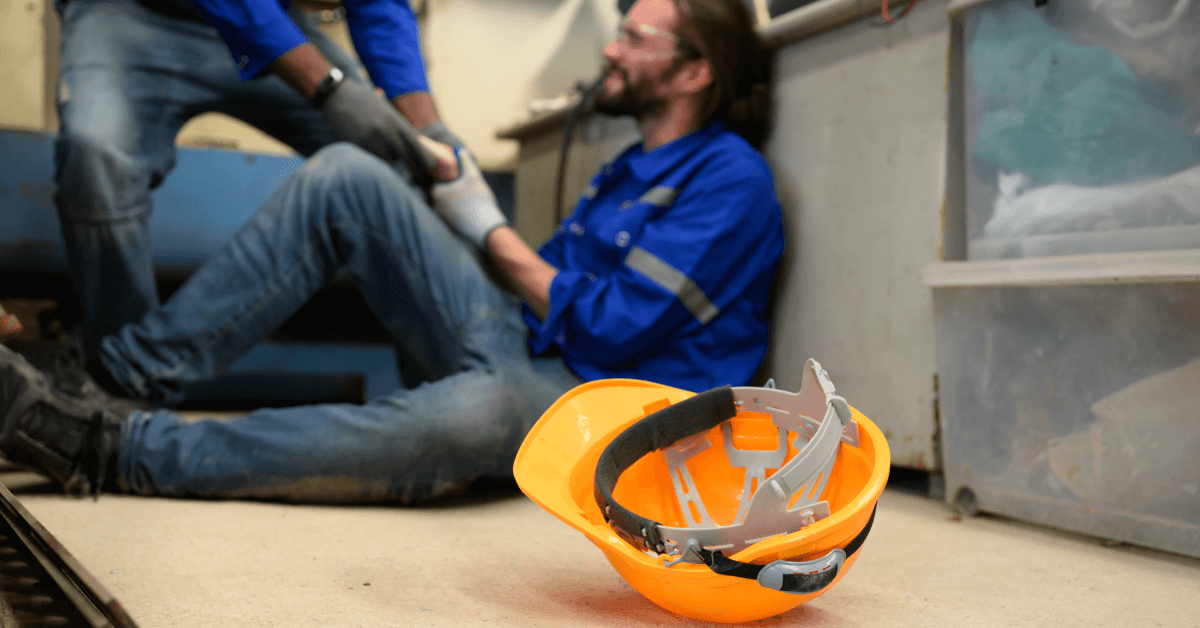
Whenever there’s a large-scale product safety failure, the question inevitably comes up: What went wrong, and could this have been prevented?
Manipulated test data, faulty product designs, poor safety culture—all of these and more have been linked to some of the most infamous recalls of the past few decades.
As for what manufacturers can learn from these recalls, it all comes down to prioritizing safety and quality over profits, and ensuring consistent checks to make sure that commitment is carried out on the plant floor.
Watch our webinar on How Digital Layered Process Audits Close the Accountability Loop
1. Takata Airbag Recall
The Takata airbag recall is one of the largest in history, stretching out over a decade and persisting to this day. The event affected 67 million vehicles from multiple manufacturers, sent Takata into bankruptcy, and caused at least 36 deaths.
The root cause was the use of a chemical propellant (ammonium nitrate) that is unstable at high humidity, causing some airbags to explode and send dangerous shrapnel into vehicles.
Multiple investigations revealed deeper issues that pointed to a broken safety and quality culture involving manipulated test data and delayed corrective actions. Production lapses also played a significant role, including problems like:
- Inconsistent environmental conditions during production
- Defective inflators that allowed moisture to enter inflator cartridges
- Quality checks that were inadequate or skipped altogether
- Leadership ignoring concerns raised about production issues
- Insufficient supplier oversight on the part of automakers
Lessons for Manufacturers
The key lesson from the Takata airbag recall is that prioritizing production over safety and quality can have disastrous consequences. It’s why several automotive OEMs now require suppliers to conduct layered process audits—frequent checks of manufacturing inputs performed by multiple levels of management.
A strong layered process audit program supports safety and quality culture, and reduces the risk of issues seen in the Takata recall by:
- Getting multiple sets of eyes on manufacturing processes so that problems aren’t overlooked
- Providing frequent checks of key process inputs like operator behavior and environmental conditions
- Improving accountability, transparency, and communication with leadership around plant floor problems
Of course, all of this starts with recognition from the top that safety and quality culture is paramount. Without this, none of your efforts will be enough to counteract the message that leadership cares more about profits.
2. Samsung Galaxy Note 7 Recall
In 2016, 3 million Galaxy Note 7 phones were recalled over defective batteries that caused some phones to overheat and catch fire. Production of the phone was ultimately halted over manufacturing defects in the batteries.
The problem was traced back to several issues that caused the batteries to short circuit:
- A design flaw in one battery type related to insufficient insulation between electrodes
- In a second battery type, welding defects created a sharp burr on some batteries
- The compact design of the phone left insufficient room for heat dissipation
What makes Samsung unique among the recalls listed here is the company’s response to the issue. Within two weeks, they announced an exchange program and ceased production of the phones entirely within two months. They also built a large-scale testing facility to investigate the failure, where more than 700 engineers gathered and analyzed data from 200,000 phones.
Lessons for Manufacturers
Manufacturers can learn several lessons from this recall, especially in terms of:
- Design: Risk management is critical at the design stage, such as using a design failure mode and effects analysis (DFMEA). It’s also essential anytime components are replaced, since this can introduce new risks.
- Production quality: Preventing production defects requires meticulous checks, including of craftsmanship elements like welding quality (another area where layered process audits can help).
- Corrective action: Taking the problem seriously and acting quickly to contain and correct the problem helped limit its impact, both to the public and the company itself.
3. Peanut Corporation of America Recall
In 2008 and 2009, a multi-state Salmonella outbreak linked to contaminated peanut products triggered a massive recall affecting thousands of products from Peanut Corporation of America (PCA). PCA was a major supplier to numerous food companies, with the outbreak sickening hundreds of people and leading to nine deaths.
The root cause of the PCA recall was traced back to unsanitary conditions and gross negligence by company leadership, including:
- Mold, dead insects, and rodent infestations in the PCA plant
- Structural issues such as holes in the roof that allowed pests to enter the plant
- Shipment of products that were known to be contaminated with Salmonella
One unique element of the PCA recall is that it led to criminal fraud and conspiracy charges for company executives, leading to years of jail time.
Lessons for Manufacturers
It’s easy to dismiss the PCA scandal as a case of egregious behavior on the part of company executives. While their disregard for public health and safety was shocking, food recalls are still common due to similar issues that occurred at PCA such as:
- Sanitation issues, especially where facilities are not well-designed or well-maintained
- Inadequate testing and preventive controls
- Lack of consistent checks on the manufacturing process
As in every recall discussed here, it’s vital to recognize that culture starts at the top. A robust system of layered process audits communicates a commitment to quality and safety, while providing accountability around non-conformances and added levels of protection against failure.