Manufacturing Quality Management System (QMS): What Is It and Why Do You Need It?
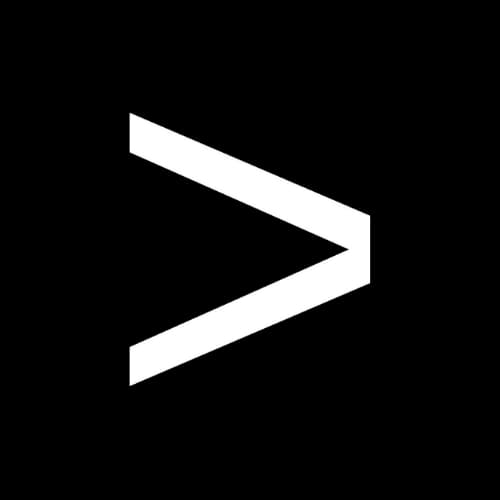
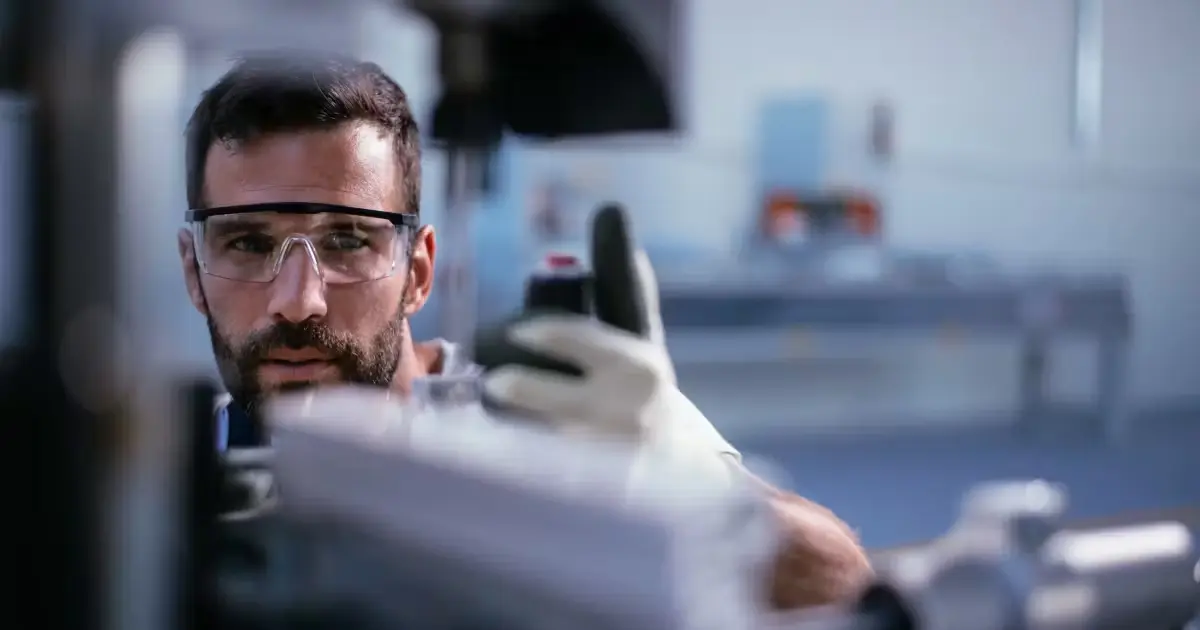
Every successful manufacturing organization strives for quality. But product quality isn’t something that just happens by chance. Manufacturers with a reputation for excellence also have a world-class quality management system (QMS) that safeguards against defects while continuously pushing for better results.
In this guide, we explore the basics of quality management systems for manufacturers, including:
- What a quality management system for manufacturing is, and why it’s crucial
- The tangible benefits it brings to your quality control or quality assurance
- The stages, components, and methods of QMS
- How a QMS relates to ISO’s 7 Quality Management Principles
We’ll also examine the ongoing transition in manufacturing from paper-based quality systems to targeted digital solutions, including how to implement a QMS that drives continuous improvement.
Download your free eBook on Cost of Quality: The Hidden Truth Behind Your Ultimate Quality Metric
What is a Quality Management System in Manufacturing?
A QMS is a formal system with documented processes, procedures, and responsibilities for achieving quality objectives and policies. The key word here is “documented,” underscoring the importance of documentation and record keeping in quality.
The goal of a QMS is to improve product or service delivery and create happier customers, while reducing manufacturing costs and improving efficiency. It’s also quite important in defining everyone in the organization’s roles and responsibilities in achieving quality objectives.
Why Do You Need a QMS?
Effective quality management in manufacturing ensures the quality of products meets customer expectations and complies with regulatory standards. Without a well-implemented QMS, companies face significant risks, like:
- Failing to identify nonconforming processes and hidden factory issues
- Low visibility into quality metrics, including leading indicators
- Not effectively resolving problems in a timely manner
- Non-compliance with regulations and standards
- Being unable to verify the effectiveness of employee training
Left unchecked, these challenges can lead to nonconformances, defects, or deviations. If those problems are not caught before shipping, you’ll be dealing with customer complaints, expensive product recalls, and rework. Companies without an effective QMS also put themselves at risk of costly regulatory violations and penalties. All of these can lead to a damaged reputation and loss of key business contracts.
A robust QMS establishes clear policies, procedures, and accountability structures, which enable companies to detect and address quality issues early. With a QMS, you can embed quality into every stage of production. This helps you improve operational efficiency, which leads to reliability. That, in turn, builds customer trust and supports long-term business success.
Learn common misconceptions around quality costs and how manufacturers can use the 1-10-100 rule to push down cost of quality.
Benefits of a Manufacturing QMS
As you can see, quality management systems help mitigate several risks in manufacturing. As a result, implementing a QMS leads to some significant benefits for your organization.
Customer Satisfaction
With standardized processes comes consistency, and with continual improvement, you can deliver an exceptional product or service. Both these features build trust with consumers, which helps your reputation in the market.
Operational Efficiency
Planning ahead compels you to proactively think of potential issues that could arise, which allows you to devise solutions before a problem causes issues with your production. As a result, you are prepared for most eventualities, or at least have a plan to rectify them.
Cost Reduction
Efficient processes result in fewer rejected products, less material wasted, and fewer instances of rework. This helps reduce the overall cost of production.
Continuous Improvement
The QMS process is designed to collect data and help you use it to make informed decisions. It quickly highlights any inefficiencies and drawbacks in your processes, with systems in place to help you improve them.
Competitive Advantage
You know that reliable and consistent products help your reputation in the market, and that streamlined processes reduce your operational costs. Together, these features help your bottom line.
Compliance
Manufacturers are expected to comply with the regulatory standards of their industries. By building these into your QMS, you can avoid legal repercussions and fines.
Parts of the Quality Control Management Process
Before we dive into the essential components of a QMS, let’s first understand the principles of quality control management. This process can be divided into four parts:
Quality Control Planning
It’s very difficult to plan or improve something if you don’t know what your goals are. Understanding your baseline will determine what quality standards you should follow (more on that later). Each standard has its own set of requirements, and knowing which one to follow helps you understand the necessary procedures to comply.
Some of the questions you might want to ask yourself during this stage are:
- Do you know your stakeholders’ expectations and priorities?
- How does your company define success?
- Are there any standards or regulations that your industry must follow?
- Do you have designated people for handling each role in the quality management process?
- How frequently do you want to evaluate processes for quality?
Quality Control Implementation
Now that you have the roadmap planned, it’s time to execute it. Quality control refers to the process of physically testing and implementing the plan to check if it is practical.
This is the stage where you determine if you can meet all the standards you have set. It is also where you can identify any errors in the plan and fix them because it’s better—and easier—to fix flaws sooner rather than later. As such, you would have to pay close attention to all aspects of the product, including the materials you use to produce it and the processes you follow.
Once you’ve gathered the inspection data, it should be displayed in clear, visual formats, so it can be analyzed quickly and easily by everyone. These visuals should be shared through a document management system, where everyone involved in the quality process can view them for easy collaboration.
Quality Assurance
Quality control focuses on the end product and making sure it meets the standards. Quality assurance, on the other hand, is responsible for evaluating the processes used to make the product or deliver the service, keeping them efficient and error-free.
It’s a proactive form of reducing mistakes, where the inspection happens quite early in the production process to catch flaws before they affect the consumer. Identifying these errors also allows you to change your processes, thereby reducing mistakes in the future.
At this stage, you want to:
- Check whether everything from the planning stage—including processes and policies—works as intended.
- Measure the efficacy of the processes you designed and confirm that you’re complying with regulatory requirements.
- Document any insights you gained during the review process.
- Identify processes that can be improved for better efficiency and fewer errors.
QA is most effective when it’s carried out regularly by third-party auditors who are not invested in the results in any way.
Quality Improvement
Quality management efforts are only meaningful if you decide to act on your findings and change processes to improve them. To prioritize continuous improvement, you need to improve your processes, product, and overall quality.
Quality improvement is part of that cyclical exercise, where you identify what you need to change in the QC and QA stages and implement them.
Core Components of a QMS in Manufacturing
Now that we know the four broad stages of quality control management, let’s take a look at the components of a QMS. Since each of these components falls within one of the stages, we’ve grouped them accordingly.
Components of Quality Planning
Quality policy establishes the guiding principles of quality.
Quality objectives set measurable goals to achieve quality.
Risk management helps identify and mitigate risks during planning.
Process management defines key processes and workflows.
Components of Quality Control
Inspection and testing ensure products meet specified standards.
Quality control measures include checks, audits, and validations during production.
Data management tracks and visualizes inspection results to identify trends or deviations.
Components of Quality Assurance
Process audits verify that processes comply with planned quality standards.
Document and records control ensures process consistency and traceability.
Training and education ensure employees understand quality requirements.
Components of Quality Improvement
Customer feedback and complaint handling indicate areas that need improvement.
Corrective and preventive actions (CAPA) address the root causes of issues.
Continuous improvement initiatives drive innovation and long-term quality gains.
QMS Methods
While the components of a QMS provide the structural framework, QMS methods are the tools and techniques that allow you to practically implement it. They ensure that the goals set by the QMS are consistently met. Here are some key QMS methods:
Root Cause Analysis
Tools like the 5 Whys, fishbone diagrams, and scatter plots are used to identify the underlying root causes of nonconformities or process failures. These methods help resolve problems at their source and prevent them from recurring.
Statistical Process Control (SPC)
SPC involves using data-driven methods like control charts to monitor process variation. It helps detect trends or deviations early and drives proactive quality management.
Plan-Do-Check-Act (PDCA) Cycle
This is an iterative method for continuous improvement through which you systematically plan changes, implement them, review results, and make further refinements.
Failure Modes and Effects Analysis (FMEA)
FMEA is a risk assessment tool used to identify potential failures in a process or product, evaluate their impact, and prioritize mitigation actions.
Internal and External Audits
Auditing ensures compliance with internal standards and external regulations. These reviews highlight gaps and provide actionable insights for improvement.
Corrective and Preventive Actions
CAPA processes address immediate quality issues (corrective) and implement measures to prevent similar problems in the future (preventive).
Process Mapping
Techniques like flowcharts and swimlane diagrams visually define workflows, clarifying roles and identifying bottlenecks or inefficiencies.
Supplier Management
Supplier scorecards and audits help evaluate and monitor supplier performance in terms of the quality of materials and components.
Key Performance Indicators (KPIs)
Metrics and KPIs such as defect rates, on-time delivery and cost of quality are tracked to measure the effectiveness of the QMS and identify areas for improvement.
Data Analysis and Visualization
Using methods like Pareto analysis or histograms, teams can interpret quality data effectively, identifying trends and prioritizing improvement areas.
These methods are essential for translating QMS principles into actionable practices, ensuring the system’s success in driving quality and efficiency across manufacturing operations.
Learn more about how to implement layered process audits (LPA) with our free Ultimate Guide to LPA. Find tips and tricks, real life examples, checklists and expert advice from seasoned LPA professionals.
Quality Standards and Regulations in Manufacturing
Manufacturers today are subject to numerous quality standards and regulations that outline the requirements for a quality management system in manufacturing.
At the top of the standards list is ISO 9001, which is the most recognized quality management standard in the world. While manufacturing organizations are not required by law to follow this standard, in many instances, OEM customers require their suppliers to be ISO 9001-certified. Following that, there are industry-specific quality standards, like:
- ISO 13485 for medical device manufacturing quality management
- ISO 22000 for food manufacturing quality management
- IATF 16949 for automotive manufacturing quality management
- AS9100 for aerospace manufacturing quality management
In terms of quality regulations, the U.S. Food and Drug Administration has established regulations for medical device quality, pharmaceutical quality, and food quality.
Medical Device Manufacturing
ISO 13485:2016: Focuses on the safety and efficacy of medical devices and covers design, development, production, installation, and servicing.
FDA 21 CFR Part 820 (Quality System Regulation – QSR): U.S. regulation for consistent production and control of medical devices.
Good Manufacturing Practice (GMP): Covers equipment verification, process validation, and documentation.
Pharmaceutical Manufacturing
ICH Q10 (Pharmaceutical Quality System): Framework for product lifecycle management that encourages innovation and continuous improvement.
PIC/S GMP: Harmonized standards for pharmaceutical quality assurance.
GMP (e.g., US GMP, EU GMP, WHO GMP): Ensures quality, safety, and efficacy.
Cosmetics Manufacturing
ISO 22716:2007: GMP guidelines for production, control, and storage.
Regulation (EC) 1223/2009 (EU Cosmetics Regulation): Safety testing and compliance for cosmetic products.
Food and Beverage Manufacturing
Global Food Safety Initiative (GFSI): Sets criteria for food safety standards.
ISO 22000:2018: Requirements for Food Safety Management Systems (FSMS).
ISO Quality Management Principles
ISO has published guidance on what it considers the seven core quality management principles, which manufacturers can use as a reference when implementing a QMS.
The seven ISO quality management principles are:
- Customer focus: Understanding and meeting customer needs, both current and future, are crucial for sustained success. This principle emphasizes exceeding customer expectations.
- Process approach: Employees must understand that their work is part of an interconnected process. This approach provides more consistent and predictable results while improving efficiency and effectiveness.
- Leadership: Leaders at all levels need to be united in purpose. This principle emphasizes a top-down approach to ensure all employees are engaged in achieving the organization’s quality objectives.
- Engagement of people: Successful organizations instill the belief that quality is everyone’s job. This principle recognizes that involving employees leads to a better outcome.
- Continuous improvement: Quality management is not a one-and-done task to be checked off a list. This principle focuses on the need to continuously drive innovation, performance enhancement, and quick responses to changes.
- Evidence-based decision-making: Data-driven decision-making is the gold standard in quality. This approach reduces guesswork and is more likely to deliver the desired result.
- Relationship management: This principle recognizes the interdependence between an organization and its stakeholders, including customers and suppliers.
These principles form the foundation of effective quality management systems and guide organizations in their pursuit of excellence.
Benefits of an Automated Manufacturing QMS
Quality management systems provide numerous benefits, all leading to one central goal: increasing customer satisfaction. QMS automation, in particular, holds the key to breakthrough improvements in quality, eliminating many inefficiencies inherent in paper-based, manual tracking systems.
Below, we explore some of the top benefits manufacturers can expect to gain from implementing an automated QMS.
Visibility
A QMS provides a clear, comprehensive view of your quality processes and any issues that need attention. You can easily access and analyze quality data from various stages of production, and make informed decisions quickly to limit the scope and cost of potential problems.
Efficiency
By standardizing processes and documenting procedures, a QMS reduces errors, minimizes waste, and optimizes resources. An automated QMS makes it easier to identify and eliminate bottlenecks in your process, leading to improved productivity and cost savings.
Trend and Pattern Tracking
With QMS software, manufacturers can centralize quality data in one place. This enables you to track trends and patterns over time, identify areas for improvement and mitigate the risk of quality escapes.
Root Cause Identification
When problems arise, a QMS provides you with the tools to determine the root cause more effectively, whether you’re conducting a 5 Whys, 8D or fishbone analysis. By centralizing all relevant information, you can quickly analyze data, identify the source of the issue, and implement targeted corrective actions.
Fewer Audit Findings
A robust QMS reduces the likelihood of external audit and customer audit findings. Standardizing your processes and maintaining proper documentation helps demonstrate compliance, and gives customers and external auditors confidence in your operations.
Improved Quality Metrics
A QMS helps reduce defects, minimize customer complaints, and improve on-time delivery. This, in turn, can have a positive downstream effect on metrics like scrap, overall equipment effectiveness (OEE), and cost of quality. Consistently meeting or exceeding quality requirements and targets is the key to ensuring customer satisfaction—the driving goal of quality.
Effective Issues Management
With a QMS in place, you can ensure that you’re addressing and resolving quality issues quickly. Establishing clear procedures for problem identification, escalation, and resolution helps minimize the risk of problems falling through the cracks, leading to a more proactive quality culture across your operations.
Supporting Quality Excellence Frameworks
A QMS is an essential tool for companies pursuing process excellence using frameworks such as lean, Six Sigma, or Total Quality Management (TQM). Documenting processes, gathering data, tracking results—all of these are simplified with an automated QMS so that teams have more time to focus on strategy rather than repetitive or administrative tasks.
Driving Quality Culture
A robust manufacturing QMS supports quality culture by giving you the tools to proactively solve problems and demonstrate an authentic commitment to quality. It also helps in training management and communicating to your team the importance of quality.
When your team sees the constant and consistent approach to quality through efficient processes, real-time data access and quick issue resolution, it builds engagement and trust. It creates a feeling of responsibility and pride in their work.
Automation also makes work less tedious, which helps with morale. All these factors combine to create a culture of continuous improvement.
Implementing QMS Software in your Plant
Establishing and implementing quality management software is a complex process that requires careful planning and execution. While a full exploration of the topic is beyond the scope of this article, below are the key steps on a high level:
- Identify the need: Begin by building a solid business case that clearly articulates the benefits of transitioning to a QMS software solution.
- Build your team: Involve multiple stakeholders from various departments and secure leadership buy-in using your business case.
- Gather requirements: Determine the most important features your organization needs in a quality management software solution. Depending on your specific industry and operational needs, you might be looking for one or more specific capabilities such as:
- Audit and inspection management
- Deviation and nonconformance management
- Supplier quality management
- Complaint handling
- Change control
- Risk management
- Failure Mode and Effects Analysis (FMEA) capabilities
4. Narrow down vendors: Consult colleagues, leverage resources like Gartner reports and review sites, and evaluate how potential vendors align with your priority capabilities. Consider key features like adaptability, ease of use, ability to integrate emerging technologies, and flexible licensing and hosting.
5. Request demos: Shortlist 2-3 vendors and schedule demonstrations of their products.
6. Choose your system: Make your final selection based on your initial criteria, but also consider factors such as vendor support, training resources and pricing structure.
7. Implementation: Collaborate with your chosen vendor to develop a rollout plan, which often involves piloting the system at one location before expanding to others.
These steps help organizations select quality management software that not only meets their current needs but also positions them well for future challenges and opportunities in quality management.
Whether you’re transitioning from paper-based processes or looking to optimize your existing digital systems, the right QMS solution can transform your operations. It’s not about finding a tool with the flashiest bells and whistles, but finding the solution that meets your organization’s unique needs and challenges.
From reducing defects and costs to streamlining audit management, strengthening quality policies, and enhancing customer satisfaction, well-executed quality planning is your pathway to process excellence.