Profiles in Quality: Joseph Juran
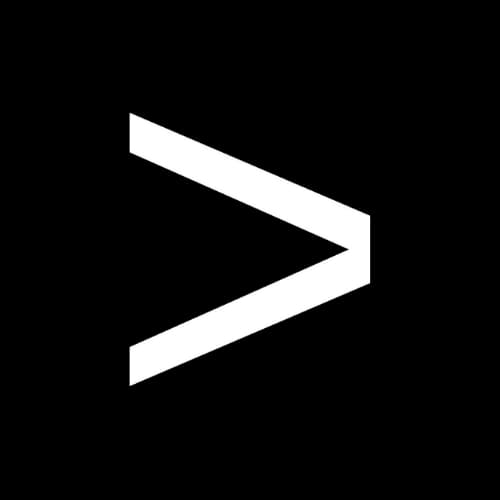
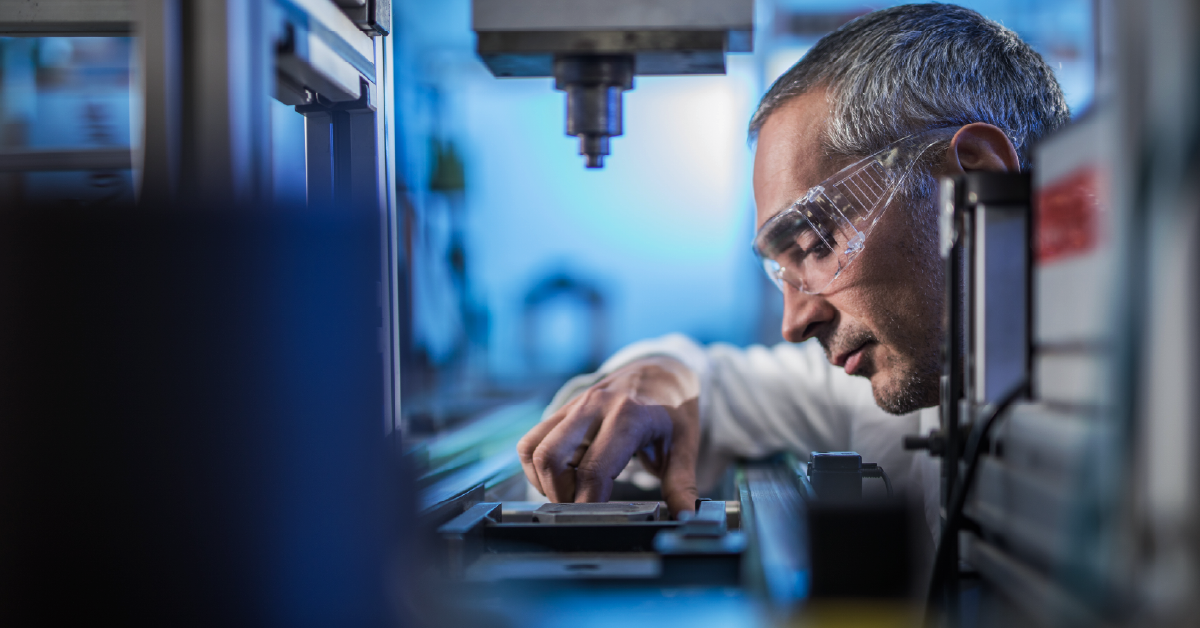
“Without a standard there is no logical basis for making a decision or taking action.” –Joseph Juran
Today, this idea is so fundamental to the practice of quality management that it seems a statement of the obvious.
In quality pioneer Joseph Juran’s time, however, it had not yet been truly internalized by manufacturing leaders. Widely considered one of the founding fathers of quality management, Juran had an impact on manufacturing quality that can hardly be overstated, with a career spanning many decades and continents.
Today’s post, the second in our series profiling quality leaders, focuses on the life of Juran, including his contributions and lasting legacy in the field of quality management.
Download your free Root Cause Analysis 101 Guidebook for an overview of common root cause analysis tools
Early Life and Career
Born in 1904 in Romania, Juran came to the United States at the age of eight, when his family settled in Minneapolis, Minnesota. As a young man, Juran held over a dozen jobs ranging from selling newspapers to janitorial work before earning a degree in electrical engineering from the University of Minnesota.
From 1924 to 1941, Juran worked as an engineer at Bell Laboratories’ Western Electric Hawthorne plant in Chicago, where his time overlapped with that of W. Edwards Deming. There he was exposed to the ideas of Walter Shewhart and became part of a new department focused statistical quality control, one of the first of its kind.
Juran left Bell to work in the Lend-Lease Administration during World War II, after which he became a professor of industrial engineering at New York University. In 1951, he published his Quality Control Handbook, still widely considered a seminal text in quality control.
Experience in Japan
After World War II, Juran chose to continue his work in quality management rather than return to Bell. His reputation had grown globally, and in 1954, the Union of Japanese Scientists and Engineers (JUSE) invited him to Japan to discuss his quality control theories and techniques.
At the time, Japan’s economy was still reeling from the effects of World War II, and leaders were looking for a new way forward. While visiting the country, Juran met with managers from different Japanese companies on how they could use quality control to improve their processes.
The visit was a resounding success, and Juran visited the country nine more times to continue teaching his quality philosophy. Similar to Deming, his work there helped spark a revolution in quality in Japanese industry. This ultimately led to Japan gaining a competitive advantage in the global market as manufacturers there began producing higher quality vehicles at lower cost.
The development of the Lean methodology was also a byproduct of his work there, spreading across the globe to redefine quality as we know it.
Contributions to Quality Management
Over the nearly 75 years Juran was actively working, he published hundreds of articles and papers, as well as over 30 books. Many of these books continue to be bestsellers, a testament to the lasting impact of Juran’s ideas in the field of quality.
Foremost among these are the idea of the ‘vital few,’ as well as what’s known as the Juran Quality Trilogy. Juran was the first to identify how the Pareto principle or 80/20 rule could be used in quality management. The 80/20 rule is about separating the “vital few” from the “useful many,” for example identifying the 20% of defects that account for 80% of quality costs.
The Juran Quality Trilogy is the foundation of quality in many manufacturing organizations today, and is comprised of three components:
- Quality planning: Defining customer expectations and requirements at the design stage
- Quality control: Conducting ongoing checks to monitor processes and keep them in control
- Quality improvement: Proactively optimizing and refining processes to drive ever greater levels of quality
Another element that made his approach unique was his focus on the human dimension of quality, recognizing disengagement in upper management as the primary roadblock to improvement. Solving this problem, he said, was the key to overcoming cultural resistance to change.
As he put it, “Observing many companies in action, I am unable to point to a single instance in which stunning results were gotten without the active and personal leadership of the upper managers.”
Today, this principle still stands as a fundamental tenet of quality culture. What Juran astutely recognized was that quality excellence goes beyond mere statistics, processes and tools. Rather, it depends on a personal commitment—starting at the top of the organization—to deliver high quality products that consistently meet and exceed expectations.