How Scrap and Rework Affect Cost of Quality and OEE
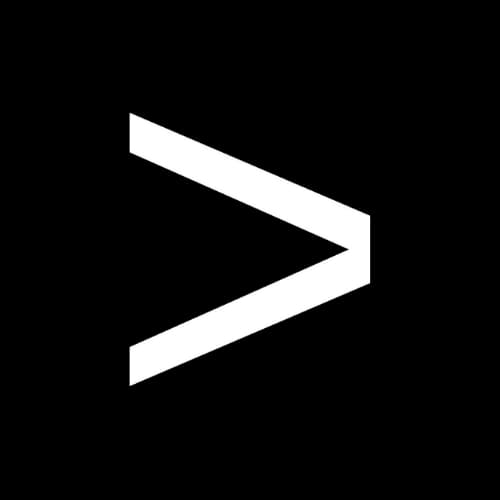
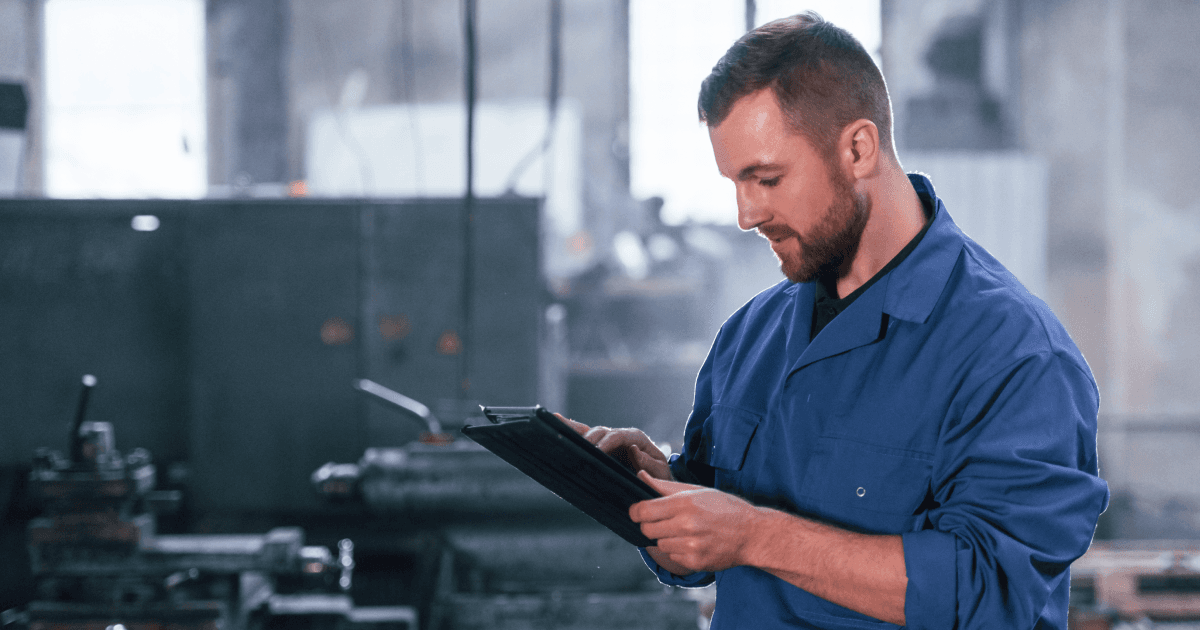
Tracking quality metrics is an integral part of quality improvement. Just as important is understanding the interplay between them, so you can find key leverage points where targeted actions can have maximum impact on the results you’re trying to achieve.
Today’s article is the first in a series on how key metrics work together, looking at scrap and rework in the context of cost of quality and overall equipment effectiveness (OEE).
Download your free eBook on Cost of Quality: The Hidden Truth Behind Your Ultimate Quality Metric
Understanding OEE
OEE is a summary metric calculated by multiplying three variables: availability, performance and quality.
Availability is a function of downtime, and is defined as the percentage of planned production time a machine actually runs:
Performance is a function of whether you’re meeting your ideal cycle time:
Quality is a function of the number of defects produced:
An OEE of 100% would indicate a machine or plant running with zero downtime at ideal cycle times with zero defects. Availability, performance and quality are all negatively impacted by what are called the Six Big Losses, a concept that originates from Total Productive Maintenance.
OEE variable |
Six Big Losses |
Availability | · Equipment failure · Machine setup |
Performance | · Minor stoppages · Reduced operating cycle time |
Quality | · Scrap · Rework |
Scrap, Rework and Cost of Quality
It’s not hard to see how scrap and rework would add to quality costs. What may surprise some manufacturers, however, is just how much it costs them.
The issue with scrap, and quality costs in a larger sense, is that what you can quantify is just the tip of the iceberg. On top of wasted time and material, there are also other hidden costs to consider that are harder to quantify, including:
- Cost of waste disposal and transportation when parts can’t be reworked
- Detection and correction costs associated with having to find and fix defective parts
- The opportunity cost associated with using resources on products that can’t be sold
- Lower profit margin on reworked products due to the additional work needed to bring them into conformance
- Lower production capacity from having to rework parts
All in all, scrap and rework costs the average manufacturer up to 2.2% of annual revenue, which can quickly add up depending on the company size.
Company Revenue |
Scrap and Rework Costs |
$10 million | $220,000 |
$100 million | $2.2 million |
$1 billion | $22 million |
The key takeaway here: leveraging down scrap and rework by even modest amounts can deliver significant savings. For example, a $100 million company that reduces scrap and rework by even 10% would achieve $220,000 in annual savings—to say nothing of the improved productivity, efficiency and customer satisfaction this would deliver.
Scrap, Rework and OEE
In addition to reducing cost of quality, lower scrap and rework also equates to higher counts of conforming products, which in turn increases OEE. Let’s look at an example.
First, note that in calculating OEE, the variables we’re working with are percentages, meaning a small change in one variable can exert significant impact on OEE. For instance, let’s say your availability and performance rate are both 85%, with a quality rate of 83%:
OEE = .85 x .85 x .83 = .599 or 59.9%
Even though all three numbers seem relatively high, the final OEE number is only 59.9%, a result that would indicate some room for improvement. Here, if you were able to reduce defective parts such that your quality rate increased to 93%, the impact on OEE is significant.
OEE = .85 x .85 x .93 = .672 or 67.2%
Using Plant Floor Audits to Reduce CoQ and Increase OEE
A significant proportion of defects are attributable to process errors, such as not using the correct machine settings, loading parts incorrectly or not following standard work instructions. Often this is unintentional, such as if a process was updated but the operator falls back on old habits that result in defective parts.
Plant floor audits are essential for uncovering these process errors, which is why some industries use high frequency layered process audits to verify adherence to standards daily.
One aerospace manufacturer, for instance, reduced internal PPM by a full 73% with layered process audits, noting a strong correlation between audit volume and quality performance. A company spending $2.2M on scrap every year that achieves a similar result immediately adds more than $1.6M to the bottom line, and can also expect to see improvement in OEE.
Automated plant floor audit software like EASE is integral in achieving these kinds of results, eliminating barriers to progress with paper-based audit systems that include:
- Lag time between manually entering data and analyzing findings
- Slow issue closure times
- Lack of visibility into process nonconformance trends driving up scrap
Scrap and rework are key drivers of quality costs, and they also have a major influence on OEE. Manufacturers aiming to improve OEE should consider how digital plant floor audits can help reduce scrap, as well as address the other big losses that impact OEE.