How to Tackle the Six Big Losses in Manufacturing with Digital Layered Process Audits
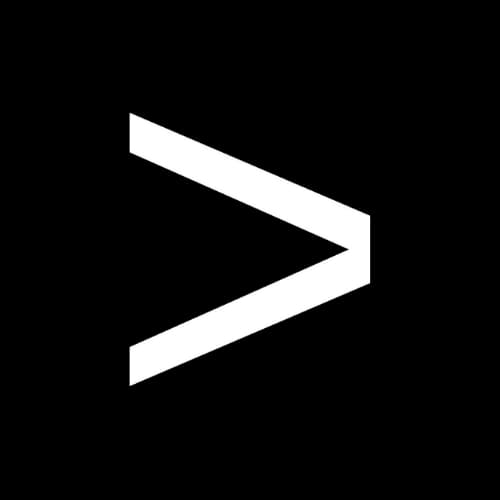
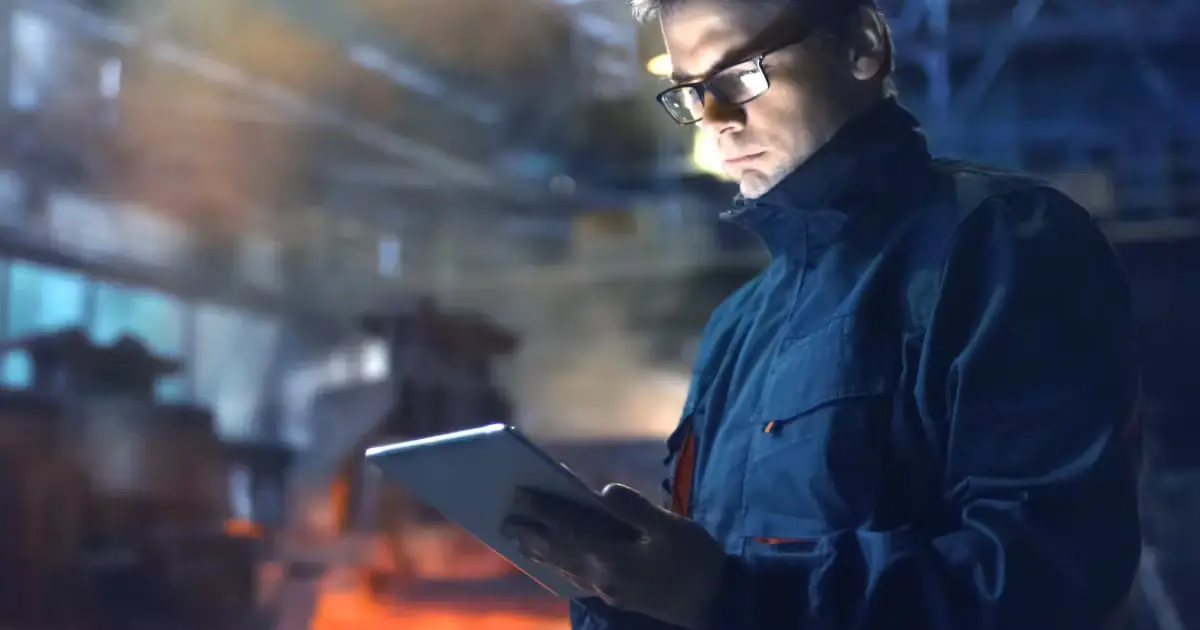
Manufacturing leaders charged with improving overall equipment effectiveness (OEE) and total productive maintenance (TPM) face a complex challenge, and it’s not always clear where to start.
At the heart of the problem sit the Six Big Losses in manufacturing processes, which is simply a way of categorizing manufacturing losses that impact the three OEE factors.
One way manufacturers can uncover and prevent the Six Big Losses is with layered process audits, a high-frequency plant floor auditing technique focused on process inputs. These audits occur every day, even as often as every shift, providing opportunities for observation, feedback, preventing slow cycles, and increasing productivity.
To see how, let’s dive in with a closer look at the Six Big Losses, their underlying causes and what plant floor checks should focus on to prevent them.
Download your free Root Cause Analysis 101 guidebook to learn more about identifying the root cause of manufacturing issues
What Are the Six Big Losses in Manufacturing?
The Six Big Losses describe common types of losses that result in a reduction in overall equipment effectiveness (OEE). Each of the losses fall into three categories, or OEE variables (availability, performance and quality rate). By analyzing the Six Big Losses, manufacturers can pinpoint specific improvements that will help increase OEE.
OEE variable | Six Big Losses |
Availability | · Equipment failure · Machine setup |
Performance | · Minor stoppages · Reduced operating cycle time |
Quality | · Scrap · Rework |
How to Address the Six Big Losses in Lean Manufacturing:
Avoid Equipment Failure, Optimise Machine Setup and Adjustments
Reduce Availability Loss
Availability is defined as the percentage of planned production time that a machine or plant actually runs. Availability losses include both planned and unplanned stops as shown in the table below.
Planned stops | Unplanned stops |
Scheduled maintenance | Equipment breakdowns (downtime) |
Tooling or machine changeovers | Tooling failure |
Equipment adjustments | Upstream or downstream bottlenecks |
Machine warmup time | Lack of operators or materials |
Even when equipment is scheduled for maintenance, the lost production time still counts towards availability loss. Manufacturers can use layered process audits to increase availability by verifying items such as whether:
- Operators perform autonomous maintenance
- They have the right tools, and those tools work correctly
- Workstations are blocked by upstream or downstream bottlenecks
- Systems for requesting additional materials are working efficiently
Download our free Ultimate Guide to Layered Process Audits
Reduce Performance Loss
Performance rate is defined as how fast a machine runs in comparison with its optimum speed. Performance loss, e.g. reduced speed, comes from idling and minor stops as well as less than ideal cycle time (reduced operating cycle times).
Performance losses | Common causes |
Minor stoppages (less than a few minutes) | · Equipment and material jams or misfeeds · Incorrect machine settings · Blocked sensors or similar issues · Stopping to clean equipment |
Reduced operating cycle time | · Machine or tooling condition · Startup and shutdown · Material quality issues · Operator inexperience |
Here, layered process audits can help identify sources of performance and productivity loss by asking questions such as whether:
- Equipment settings are correct
- Operators can describe and demonstrate steps in the production process to gauge training effectiveness
- There are issues with incoming materials slowing the process down
- Operators encounter any machine issues frequently, such as equipment jams or sensor issues
- Machines and tools are in good condition
Reduce Quality Loss (Defects & Rejects)
Quality rate is defined as the number of good parts produced compared with the total number manufactured. It is a direct function of defective parts, which can have a variety of causes. Some of the most common are incorrect machine settings and operator errors, as well as startup rejects that occur at the beginning of the shift or after changeover.
Layered process audits are a powerful tool for reducing manufacturing defects. By checking daily that operators are following standard work and that key machine settings are correct, manufacturers can proactively identify sources of quality loss so they can better prevent production rejects.
For example, layered process audits can help verify that:
- Operators correctly execute critical-to-quality steps in a specific procedure
- Machine settings are correct
- Incoming materials meet key quality specifications
- Previous corrective actions are held in place
Why Going Digital Matters to Improve OEE and TPM
Conducting layered process audits—or simply performing plant floor checks more frequently—can unlock a wealth of information for improving availability, performance and quality rate. However, upping the frequency of audits does come with its own challenges, particularly if you rely on pen-and-paper or spreadsheets.
A digital plant floor audit platform like EASE eliminates the challenges of traditional auditing by allowing you to:
- Schedule a large number of audits with just a few clicks
- Automatically notify people when it’s time to do their audits, or escalate to managers when people miss them
- Conduct audits on mobile devices and immediately upload results to the system
- Flag problems and track them to closure for greater visibility into issues
Benefits of Digitizing Layered Process Audits
- Improved accuracy and consistency
- Real-time data collection and analysis:
- Cost and time savings
- Customizable checklists
- Improved compliance
- Continuous improvement
- Integration with other systems
- Sustainability
Gain Insights on How to Improve the Production Process and Boost OEE with EASE
Improving your OEE score is a complex task, one that requires understanding the variables that go into it and how they are impacted by the six big losses. Conducting frequent plant floor checks like layered process audits can help address these losses to promote leaner, more reliable and more productive plant operations.