SMED Meaning: What is Single-Minute Exchange of Die (SMED) in Manufacturing?
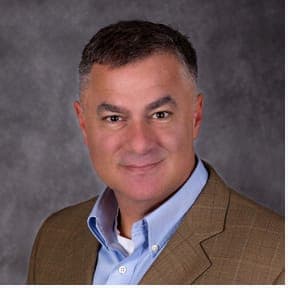
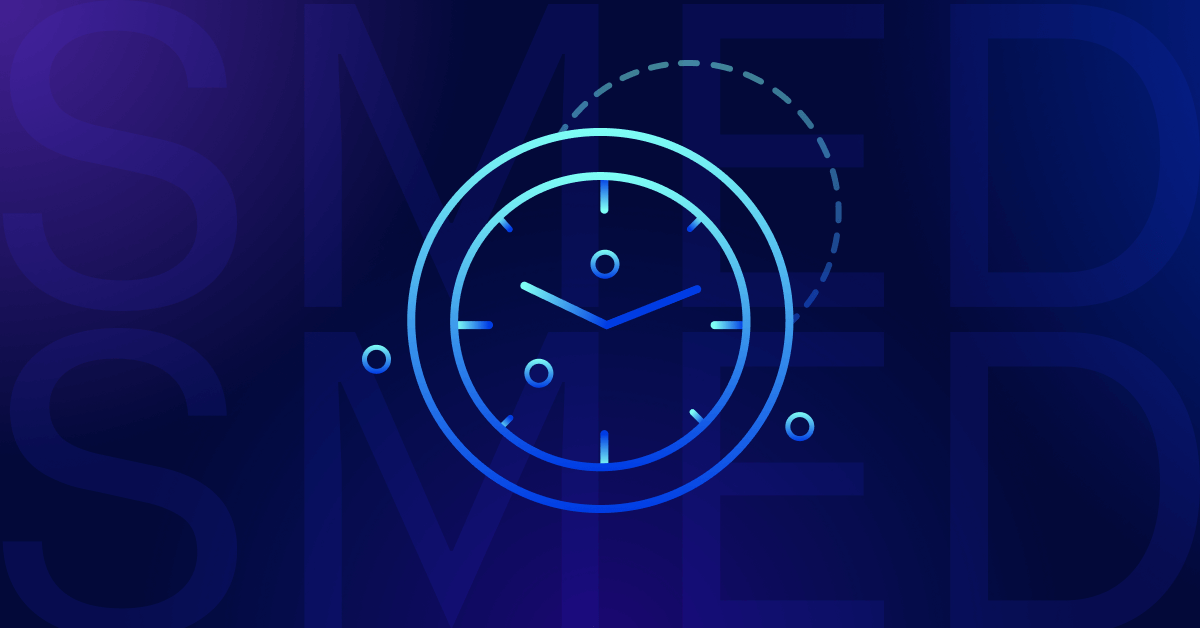
Time is money, and in manufacturing, every minute of downtime comes at a cost. Downtime created by changing or replacing tools is a costly waste, because you have the continuing costs of labor and equipment while production of parts is on pause.
When there are considerable production losses because of time-intensive or frequent changeovers, manufacturers need to pay attention to the changeover process itself. That’s because the changeover process can have significant impacts on downtime, overall equipment effectiveness (OEE), productivity, and even scrap costs.
A lean concept that can help improve changeover time is single minute exchange of die (SMED), a group of tools focused on reducing changeover times by scrutinizing the steps, tools, and responsibilities during the setup.
We’ve helped many customers utilize SMED in their plants, in some cases delivering millions of dollars in savings over the course of a year. Here, we tackle SMED meaning, taking a closer look at SMED and considerations for implementing it in your plant.
Learn more about how lean tools can help improve efficiency with a free eBook on The 5S of Lean Manufacturing Principles
SMED Meaning
Single-minute exchange of die (SMED) is a group of lean tools for eliminating waste in setups and standardizing work to reduce machine setup and changeover times, ideally to single digits (under 10 minutes).
One of the key ways that SMED helps minimize downtime is by converting internal changeover steps previously done while a machine is stopped to external steps that can be completed while the machine is running.
Reducing Changeover Time: SMED Metrics
To understand how SMED impacts manufacturing efficiency and productivity, let’s first look at two KPIs that we think about when starting a SMED workshop or project.
The first is what’s usually called “hit to hit,” or how long it takes from when a machine makes the last good part until it makes the next good part. This is the total time a machine is down. Consider a case where the last good part was made at 12:00, then the machine was shut down for a tool change. If the first good part is made at 12:20, but quality control (QC) checks take until 12:28, then the changeover was 28 minutes. That’s 28 minutes of lost production time.
The second KPI to look at is average hits per hour. This metric is strongly influenced by changeovers and downtime, and one way to improve it is to utilize SMED tools and concepts. When less time is lost to changeover, the average hits per hour will increase, indicating a more productive day.
To illustrate how changeover time impacts productivity (and profits), imagine a plant that does five changeovers in a day. If each change takes an hour, your maximum availability is 19 hours. If each changeover was reduced to 30 minutes, you’ve now gained 2.5 hours of productive machine time in a day, or hundreds of hours over the course of a year.
SMED Benefits
Reducing changeover time with SMED has a number of downstream effects on manufacturing KPIs, including:
- Productivity: Less downtime means more time that machines are producing parts and higher profitability overall.
- Overall equipment effectiveness (OEE): Shorter changeovers increase availability rate, one of the three parameters that go into calculating OEE.
- Scrap: Extended changeover times can allow for machines to change in other ways (which we discuss below), leading to downstream scrap and customer complaints.
While reducing scrap isn’t the first thing people think about in the context of SMED, it is an important benefit.
One customer we worked with had a plastic molding process where the plastic would cool and absorb moisture when the machine shut down. By reducing changeover time from an hour to less than 20 minutes, the plant was able to reduce startup scrap and the likelihood of shipping defective products. Scrap can also be reduced by standardizing the steps and settings to changeover a part, helping operators get more things right the first time.
Steps to Implement SMED
A SMED event is a type of Kaizen event, which is typically defined as focused, short-term continuous improvement projects aimed at improving a specific process within the plant.
A typical SMED event takes place over a series of a few days, bringing together a cross-functional team to analyze the process, identify inefficiencies, and implement improvements. The goal: to drive significant change quickly while building a culture of collaborative problem-solving.
With that in mind, let’s take a look at how the SMED process breaks down in five steps.
1. Observe the Process
The first thing we do in any SMED project is to take a multi-point video of the process. Here, we might take one video from the front of the machine, one from the back of the machine or at the control panel, and one from the top down, depending on what you can see.
From there, we sync the videos together to get a full view of the process.
2. Cross-Functional Review
The next step is to sit down to review the video with the changeover team, including:
- Maintenance and toolroom employees
- Die setters or mold setters
- Any operators involved
- Quality management employees responsible for checking parts and approving the setup
The goal at this step is to get agreement on what the process is right now, which is harder than it seems. Teams may think they are doing a specific set of steps, but when they see it on video, it’s actually something different.
Once you establish the baseline process, you start looking for different areas of waste, particularly movement. For example, let’s say employees move the old material somewhere, and then they have to move it again to make room for the new material. That is essentially wasted movement that increases changeover time where streamlining movements can have an impact.
3. Externalize Changeover Steps
Remember that when you turn the machine off, the clock is ticking in terms of time between hits, making whatever you do during that time especially critical.
The key idea here is to start any possible changeover steps before shutting the machine down, while it’s still making good parts.
One classic example would be a stamp within the machine marking parts with the date. Many companies put the die or mold in the machine, then open it up and increment the date in the machine. Rather than doing it during changeover, however, you can look to have the date set correctly before the setup even begins.
Another example would be to look at whether you can get all of your molds or dies to a single shut height. This may mean installing a backplate onto a mold to get it to a specific height, but the advantage is it’s something you can do while the press is running. If you have to put the mold in and inch the press down, that’s time you could be using to continue making parts.
4. Streamline Remaining Internal Changeover Steps
Next up, you want to look at all remaining internal changeover steps and find ways to make them as efficient as possible. If someone is using a hand wrench, for instance, could they use a pneumatic driver instead?
Another example would be if you have a person who has to tighten bolts in the front of the press and then walk around to work on the back of the press. If you instead have two people working simultaneously, one in front and one in back of the press, you’ve just saved valuable time in the changeover process.
Ultimately, externalizing all steps possible and improving the efficiency of what’s left is what will get you closer to a true SMED changeover.
5. Create Your Pre-Flight Checklist
Every good SMED changeover requires a good pre-flight checklist to make sure all the right elements are in place.
As an example, let’s say a changeover process requires fastening a mold with eight fresh bolts rather than using potentially damaged or dirty ones. Your pre-flight checklist would then ask questions like:
- Are the eight bolts there?
- Are the bolts cleaned?
- Are the threads good?
- Is the socket head cap screw still solid?
- Is the half-inch driver used to fasten the bolts there?
The focus at this step is turning your standardized process into a list of items that people must follow to ensure conformance.
Is Automation Necessary?
Notice that in all the examples above, automation wasn’t necessary to drive improvement, which is true in the vast majority of changeovers. Externalizing changeover steps and streamlining remaining internal steps represent the low-hanging fruit for minimizing downtime.
That’s not to say automation can’t help; however, it tends to be very expensive and often requires changes to how molds and dies are designed. A better strategy is to first standardize your process and make it more efficient, an approach that delivers substantial savings with minimal investment.
Factors for Success with SMED
If you’re looking to conduct a SMED project in your plant, it’s important to know a few things up front.
First, the event requires a lot of support, commitment, and involvement from management.
That’s because any die change team can do a great die changeover once. The question is, how do you do it on a consistent basis? That’s where management comes in, providing support and regular feedback to keep the process on track.
Changeovers are a process, and one way to make sure the new SMED activity is maintained over time is to verify it with layered process audits (LPAs). Someone from management can attend changeovers and look for key elements using an LPA checklist or even the pre-flight checklist.
Second, SMED is an ongoing activity, not a one-and-done event. Once our team helps manufacturers establish a baseline changeover, we then establish a six-month plan that moves you incrementally toward your goal and more and more sources of variation are identified and eliminated.
In other words, you’re not going to go from a 30-minute changeover to a 13-minute changeover in a day. Rather, it’s a long-term process where you continually shave down the process over time. Management commitment, tracking progress, sustaining the gains—all of this is a process, not an event.
After all of this, you may be wondering—can you really get changeovers down to less than 10 minutes? In many cases, the practical answer is no, unless the process is very simple or you invest in expensive automation.
At the same time, reducing an hour-long changeover to 17 minutes has huge cost savings and efficiency implications, making SMED a worthwhile investment for those willing to go the distance. Standardize your process, externalize all changeover steps possible, and streamline the rest: This, plus consistent tracking and feedback, are the ingredients needed to reach the finish line.