Understanding the Supplier Corrective Action Request & Report (SCAR)
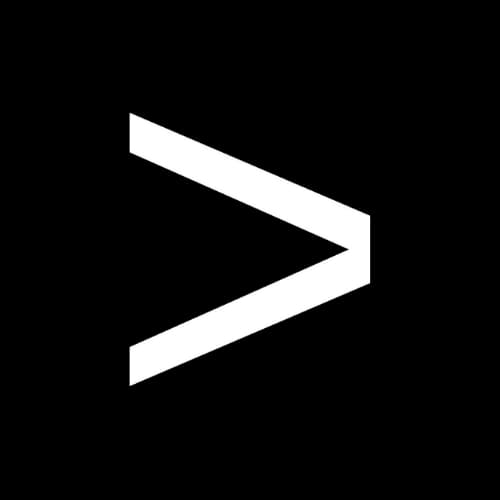

A mislabeled material is used in a manufacturing process, leading to defective products and complaints. A supplier is late with a shipment, impacting on-time delivery to customers. A supplier alters their production process without notifying the customer, causing downstream quality issues.
All of these and more are reasons that manufacturers issue supplier corrective actions—and reasons why effective supplier quality management is so critical.
To help understand how it works, this article explores steps in the process, elements to include in your supplier corrective action request (SCAR) and best practices to implement.
Download your free 38-page Root Cause Analysis 101 Guidebook to learn about common root cause analysis tools used by manufacturers
What Is a Supplier Corrective Action Request?
A SCAR is a formal notification issued to a supplier of a nonconformance they must investigate and correct. It helps drive supplier corrective actions by detailing the scope of the problem and initiating the collaboration process between the customer and supplier to address the root cause.
Supplier Corrective Action Report
SCAR is also used to refer to supplier corrective action reports. While the two terms (request and report) are used interchangeably, they aren’t the same thing. The request initiates an action, while the report records its resolution and documents accountability. Of course, in practice, organizations often conflate the two in a single document, which is why the line between the two terms is blurred.
Key SCAR Components
SCAR templates vary from one manufacturer to another, however most of them share a set of common components, as shown in the table below.
SCAR Component | Elements Covered |
Supplier information | · Supplier name · Supplier contact details |
Problem identification | · Detailed description of the problem · Date of detection · Location of issue (e.g., incoming inspection, production line, end user or customer location) |
Product details | · Part or material number · Batch and lot number · Number of units affected |
Root cause analysis | · Preliminary findings · Results of problem-solving activities (e.g., 5 Whys, 8D, Fishbone diagram) |
Corrective action plan | · Immediate containment steps · Long-term corrective actions · Preventive actions · Implementation timeline and responsibilities · Verification method and criteria |
Review and closure | · Documentation of effectiveness review results · Formal sign-off |
How Does the SCAR Process Work?
SCAs should follow a repeatable, closed-loop process to mitigate the impact of nonconformances and prevent their recurrence. Below is a high-level look at the steps in the SCAR process:
Problem Identification
The manufacturer identifies a supplier-related quality issue, such as when a defect occurs or if a plant floor audit reveals a non-conformance in materials or parts from a supplier.
Issuing a Supplier Corrective Action Request
The manufacturer formally issues a SCAR detailing the problem and asks the supplier to investigate and fix it. The supplier must acknowledge they’ve received and understood it or ask for clarification if needed.
Root Cause Analysis
Once the SCAR is issued, the supplier stops the production processes of the defective product or materials and isolates them. They conduct a root cause analysis using tools such as 5 Whys, 8D or a Fishbone diagram, reporting the findings on the SCAR.
Corrective and Preventive Actions (CAPA)
The supplier reports the immediate actions they have taken to contain the problem, as well as a detailed plan to correct the problem and prevent it from happening again.
Verification and Follow-Up
The supplier documents that they’ve implemented corrective actions correctly and sustained them, noting any future actions to be taken.
Customer Review
Once the supplier submits the completed report, the customer determines whether the actions are sufficient, or if additional steps or responses are necessary.
Final Approval
If the SCA meet the required conditions, it then goes on to the final stage for formal sign-off, with all results documented in the quality management system (QMS). If they do not pass quality control, they may be subject to action, such as removal from the approved supplier list.
Best Practices for Supply Chain Corrective Actions
One of the first questions manufacturers face when dealing with supplier-related nonconformances is whether or not to issue a formal SCAR for a given supplier issue. The criteria for opening a SCAR will depend on your own internal requirements and may be based on elements such as risk level or whether it’s a repeat issue.
Effective communication and collaboration is also crucial when it comes to SCA. This includes:
- Assessing the supplier’s root cause analysis to determine whether they’ve dug deep enough into the problem
- Working together to identify the best corrective actions, such as reworking the process, adding new controls or updating training
- Asking the supplier to evaluate other areas where similar risks exist so that appropriate preventive controls can be added
Finally, you want to remember that it doesn’t matter how good your solution is if you don’t have a system to verify that the correction is held in place. Additional checks around incoming inspection, process audits or supplier audits can all provide added safeguards to ultimately maintain high quality standards and protect your customers—and your business.
Difference Between Corrective Action Request (CAR) & SCAR
You’ll often find CAR and SCAR being used interchangeably. However, they are not the same. The distinction is in their name. SCAR specifically addresses non-conformance issues with third parties, while CAR has a more general application. It can be issued internally or externally to address conformance issues. A CAR is also broader in scope, while a SCAR is limited to the supply chain.
Supplier quality issues represent a major risk, especially for companies without good visibility into their suppliers’ processes. Implementing a robust supplier quality management program, including using SCARs effectively, can help proactively identify issues and pave the way for a stronger supply chain overall.