The Great Resignation and How LPA Software Can Help
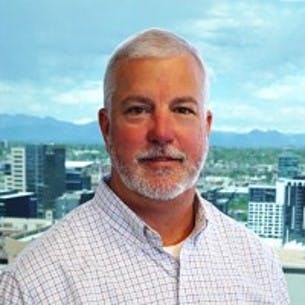
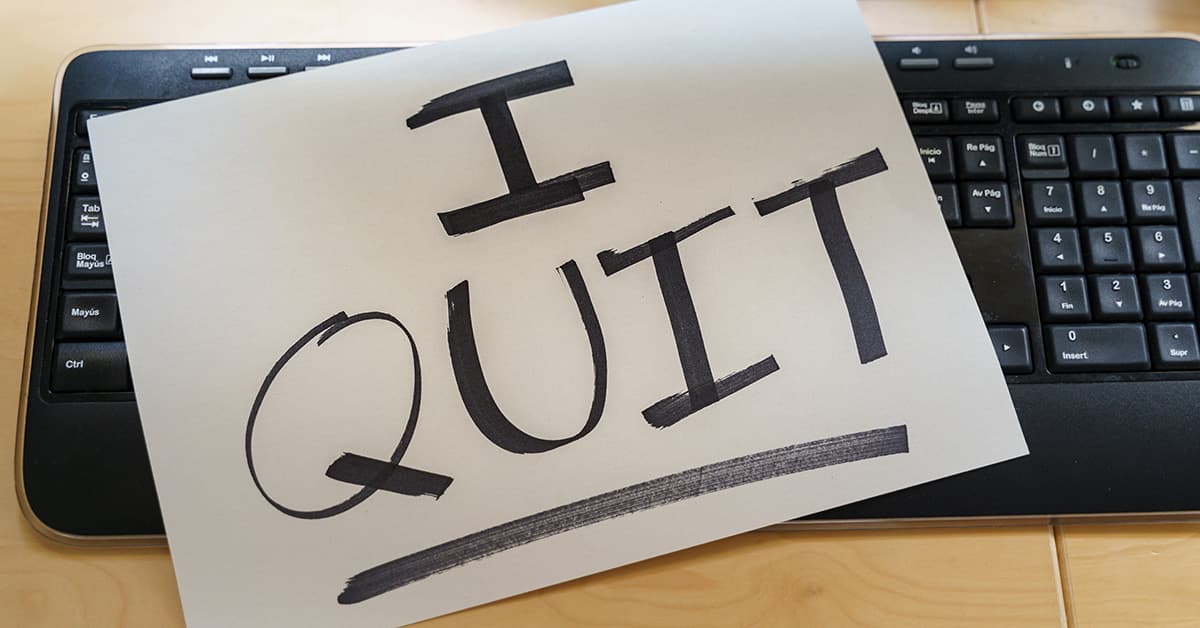
U.S. Bureau of Labor Statistics (BLS) data show that 3.5 million people quit their jobs in November 2021, a record high that’s part of what many are calling the Great Resignation.
Already facing a skills shortage, the manufacturing industry hasn’t escaped the effects of the Great Resignation. Plants today must cope with the loss of knowledge that comes with increased turnover, and that creates opportunities for quality and safety risks.
Daily process verification programs such as layered process audits (LPAs) can help manufacturers adapt and even thrive in the face of these challenges. With that in mind, let’s look at how the Great Resignation is impacting manufacturers, how LPAs reduce risk and why digitizing LPAs makes all the difference.
Learn how to use LPAs to prevent defects, complaints and audit findings with our Ultimate Guide to Layered Process Audits
How the Great Resignation Is Impacting Manufacturers
According to the BLS, 308,000 workers left their manufacturing jobs in December 2021. This represents a more than 28% increase in the number of voluntary quits compared with December 2020.
The good news, however, is that hiring is also up in manufacturing, with the number of available job openings decreasing by 66,000 in November 2021.
These trends have several direct implications for manufacturers:
- Loss of internal expertise: With people quitting at all-time record rates, plants are losing the workers who are most familiar with their operations.
- More new workers: Increased hiring means a higher proportion of new and/or temporary workers still getting up to speed on processes and procedures.
- Changing processes: In many cases, dealing with staffing shortages has meant spinning down certain production lines. Rearranging production lines can mean putting operators in areas where they may not be as familiar with equipment or operations.
All of this can add up to significant disruption in a plant, particularly from a quality perspective. Increased turnover means less familiarity with processes, meaning people are more likely to deviate from standard work. The possible results: more defects, scrap and complaints, as well as a higher risk of safety incidents among workers.
Using Layered Process Audits to Protect Quality and Safety
LPAs enable daily checks of high-risk processes, ensuring operators are following standards and processes are working as expected. These audits are often conducted at the beginning of a shift to determine whether all the conditions are in place for safe, high quality work.
LPAs counteract a lack of workforce continuity by:
- Helping find and correct instances where people aren’t following standards
- Identifying work areas with a high number of audit failures where quality problems are most likely to occur
- Revealing where training is not effective or where gaps in knowledge exist
- Helping identify tribal knowledge and hidden factory processes that impact quality
Particularly important in the context of increased turnover is the fact that LPAs require participation from multiple levels of management. This means that if you’re losing headcount in your Layer 1 auditors, the backup you get from Layers 2 and 3 provides added oversight and safety. With three groups focusing on the same work areas and issues, there are fewer opportunities for problems to slip through the cracks.
Why Digital LPAs and Vendor Support Are Key to Mitigating Risk
Not all LPA programs are created equal. Many manufacturers use paper checklists and/or Excel spreadsheets to track findings, creating complexity that leads to missed audits, lag time in reporting and lack of follow-up on issues.
Digital LPA software addresses all of these problems, unlocking greater efficiency and risk mitigation through:
- Email notifications for upcoming audits and automated escalation of missed audits, improving audit completion rates
- The ability to schedule an audit to a group to complete as available on a first-come, first-serve basis
- Links to checklists auditors can complete on a tablet or smartphone
- Instant reporting and charting to identify and prioritize problem areas
- The ability to assign mitigations and link corrective action tasks to audit findings
Vendor selection is also an important factor to consider if turnover and staff disruption is a concern. A vendor like EASE can help you make sure you’re getting the most from your LPA program by:
- Proactively reaching out to touch base on your audit programs
- Helping get new employees up to speed on platform administration
- Providing full retraining as necessary to your plant
- Identifying potential issues for review and training on new software features
The Great Resignation shows no signs of slowing down, with turnover and staffing shortages continuing to hit the manufacturing industry. These problems make the need for process verification even greater, and LPA software ensures these daily checks are effective at rooting out quality risks. The right vendor can help, providing proactive support and outreach to ensure you’re getting the most from these high-frequency audits.