The True Cost of Safety in the Workplace
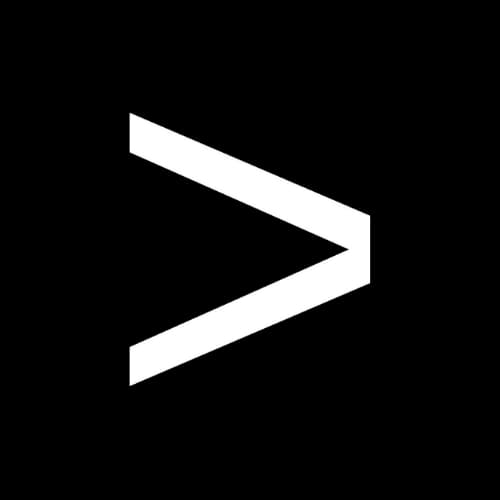
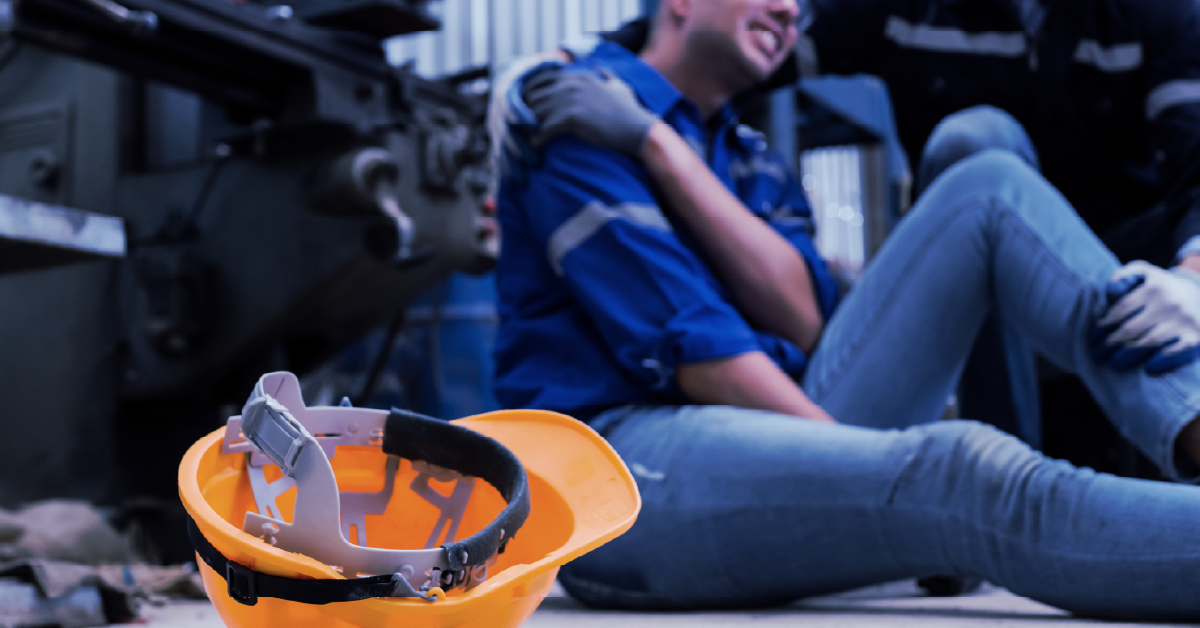
The manufacturing industry had 490,000 preventable injuries in 2021, with fatalities increasing 10% from 2020 according to National Safety Council (NSC) data.
These safety incidents represent a significant drain on businesses, on top of the often life-changing impacts on workers. In terms of financial costs, there are obvious expenses such as worker’s compensation claims, medical expenses, and regulatory penalties.
In reality, those costs are just the tip of the iceberg. Underneath them hide a wide variety of additional costs that impact the company, its workers, and society as a whole.
With that in mind, let’s take a closer look at the true cost of safety, comparing the relative impact of incidents to proactive investments in workplace safety.
Download a free white paper on Why and How Digital Safety Inspections Help Manufacturers Work Safer
Workplace Safety Incidents: The Big Picture
When talking about the impact of safety incidents, worker’s compensation costs often top the list of employer concerns, and it’s easy to see why. Liberty Mutual’s 2021 Workplace Safety Index estimates that U.S. employers pay more than a billion dollars every week on serious nonfatal injuries.
NSC notes, however, that total injury costs are more than three times that when accounting for costs not just to employers, but also individuals and society. Totaling an estimated $167 billion in 2021, these costs include:
- Administrative expenses such as insurance and legal costs ($57.5B)
- Loss of wages and productivity ($47.4B)
- Medical expenses ($36.6B)
- Uninsured costs, e.g. resources for investigation, reporting and time lost by other workers ($13.8B)
- Fire losses ($6.3B)
- Motor vehicle damage ($5.4B)
Individual Incidents and Violations in Focus
NSC estimates look at the total costs from all injuries, but how does this break down on an individual level? NSC estimates that for 2021, the average cost per medically consulted injury was $42,000. For a fatality, that number jumps to over $1.3 million.
Regulatory penalties are also a significant expense for businesses that violate safety laws. In 2023, the U.S. Occupational Safety and Health Administration (OSHA) increased civil penalties for workplace safety violations by 7.7%. For serious and other-than-serious violations, the penalty is now $15,625 per violation, and $156,259 for willful or repeat violations.
For general industry, the most commonly violated OSHA standards in 2022 were:
- Hazard communication (2,424 violations)
- Respiratory protection (2,185 violations)
- Lockout/tagout (1,977 violations)
- Powered industrial trucks (1,749 violations)
- Machine guarding (1,370 violations)
Hidden Costs of Workplace Safety Problems
While the above numbers cover a wide variety of expenses, they are still only part of the picture. Safety problems create many hidden, often unmeasured costs, including those associated with:
- Training employees to replace injured workers
- Corrective action costs
- Inefficiency from loss of skilled workers and crew breakup
- Equipment repairs and downtime
- Delivery delays
- Lower morale
- Higher employee turnover
In terms of the human cost, injured employees often suffer both lower quality of life and lower earning power, which also hurts their families. Clearly, the total impact of safety incidents runs far deeper than medical or worker’s compensation costs alone.
Investing in Plant Floor Safety
Many companies look at safety strictly from a compliance standpoint, looking only to meet bare minimum requirements. While this makes sense given the astronomical number of regulations they must meet, it is ultimately short-sighted.
A bare minimum approach often leads to underinvestment in safety, driving up costs later when businesses are forced to use valuable resources reacting to incidents. Taking into account both direct and indirect costs of safety incidents, a proactive approach focused on safety culture and prevention is far more cost-effective. As the old saying goes, an ounce of prevention is worth a pound of cure.
Frequent plant floor inspections are a key tool for addressing this challenge, allowing companies to:
- Verify compliance with safety protocols and regulatory requirements
- Monitor known hazards and identify new ones
- Verify effectiveness of corrective actions and ensure gains are held in place
- Identify gaps in safety training programs
- Foster more face-to-face conversations about safety
- Demonstrate management’s commitment to safety to gain employee buy-in
In this context, a digital inspection app like EASE is one example of a relatively low-cost investment to close the loop on risks and build a culture of safety. This type of platform can easily pay for itself if it helps avoid even a single incident, to say nothing of the efficiency gains it can provide.
Workplace safety problems take a huge toll not just on manufacturers, but also workers, their families and society in general. Rather than treating safety as a cost sink, manufacturers are advised to take a proactive approach to safety, using frequent plant floor inspections to mitigate hazards and foster safety culture.