Three Key GM BIQS Controls Every Organization Should Implement
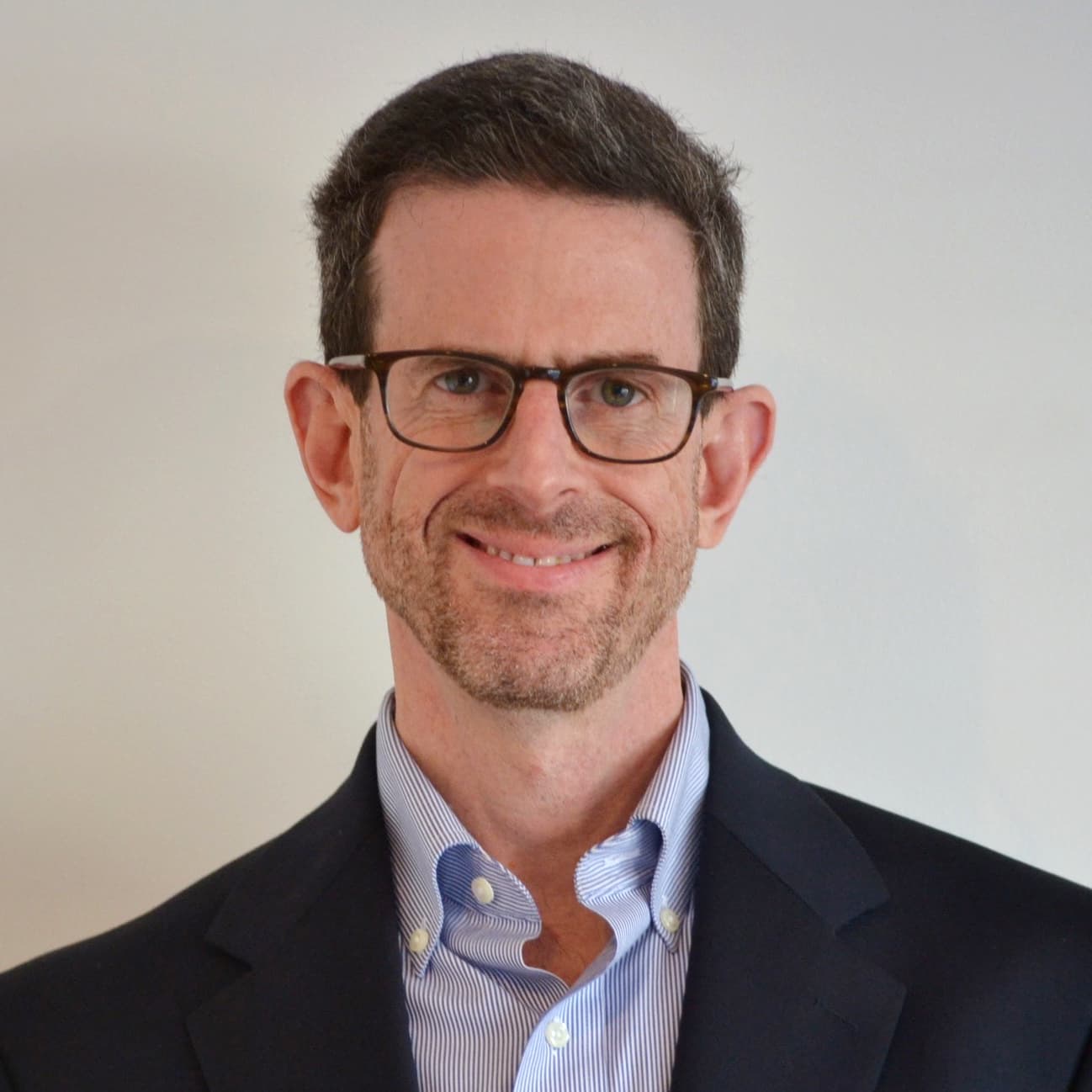
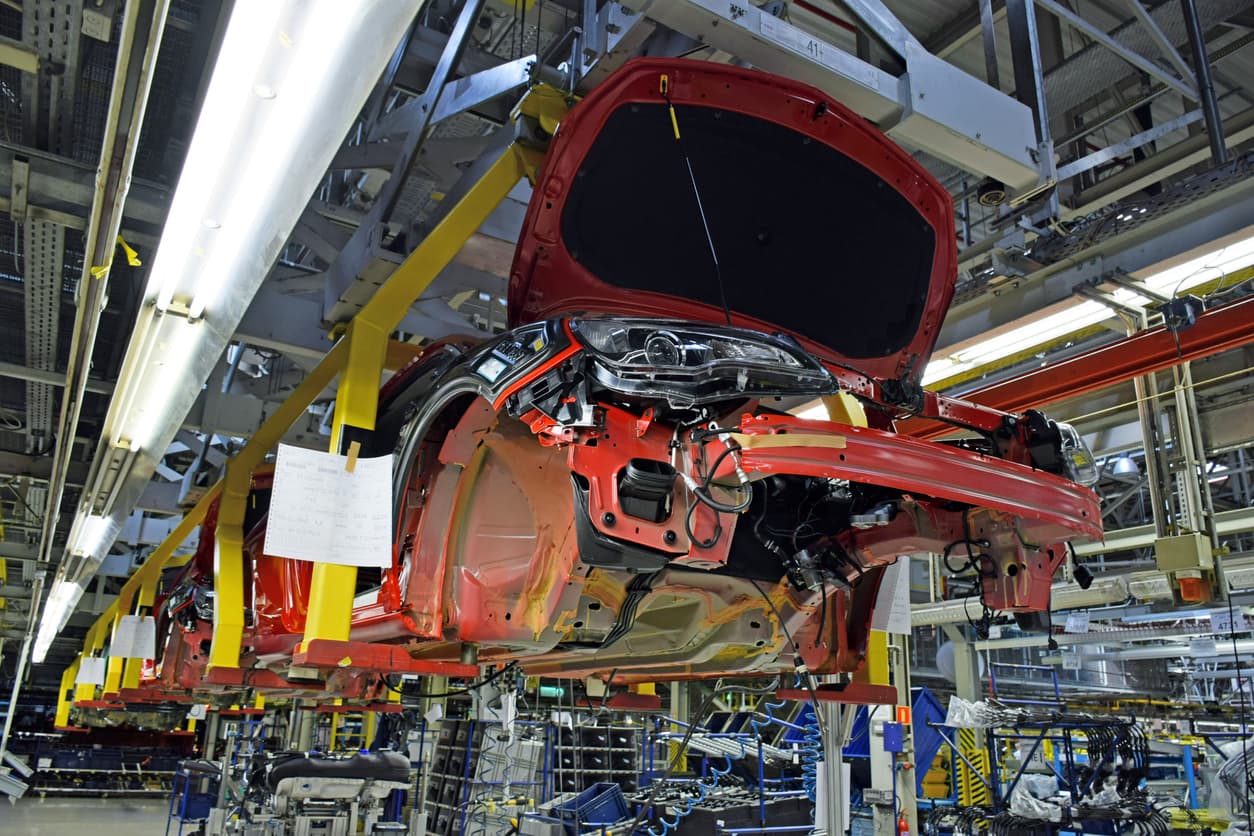
As one of the world’s largest automakers, General Motors (GM) must continually look for ways to increase value and reduce waste throughout its supply chain. Like many manufacturers, they are under pressure to keep ahead of the increasing challenge to meet demands for ever better, faster and cheaper products.
Following the unprecedented recall problems of the past few years, GM put some of their best and brightest minds together to develop new strategies that include their suppliers as one aspect of a multi-prong quality improvement initiative.
As a result, in January 2016 GM began transitioning suppliers from their existing supplier quality program, Quality Systems Basics (QSB) – which had 11 quality elements, to Built in Quality Supply Base (BIQS), a more robust 29-element strategy program. BIQS holds GM suppliers to many similar quality standards that GM implements for its own internal quality effort.
Whether you are a GM supplier seeking greater awareness of BIQS or in another manufacturing industry, BIQS contains best practice quality management strategies that can be applied in any environment to make lasting improvements in quality. Following are three examples of BIQS quality element strategies.
BIQS strategy #1 – Utilize a layered audit process that includes identifying frequency, schedule, findings, and corrective action.
Layered audits are gaining popularity in many manufacturing processes for their ease of implementation and use, and its power to bring management and shop floor employees together to verify processes are being done right the first time. According to GM’s standards, the layered audit process:
- Assesses the supplier’s compliance to standardized processes
- Assigns management the responsibility for assuring the effective implementation and adherence to scheduled audits
- Identifies opportunities for continuous improvement
- Provides coaching opportunities
- Requires management to actively participate in the audit process on the shop floor on a frequent basis
- Includes customer-specific and quality-focused checks reviewed by all layers including management
- Assigns management the responsibility of ensuring that effective corrective actions and counter measures are in place
BIQS Strategy #2 – Analyze the risk for all operations using Process-FMEA and Process-FMEA methodology
Process-FMEAs are not intended to be completed by engineers, then simply checked off, submitted to customers and filed away. Instead, using a workshop format, Process-FMEAs conducted by cross-functional teams provide a robust blueprint to ensure manufacturing quality. A key to this quality initiative is the consistent application of severity, occurrence and detection ranking tables for prioritization of risk.
BIQS Strategy #3 – Implement a fast response, problem solving process with daily monitoring
According to GM’s requirements, the supplier must show evidence that timely and thorough problem solving techniques are applied to all quality and safety issues.
Fast Response could be triggered by a high severity LPA nonconformance, end of line test failure, safety incident, customer issue or other problem. Rather than accepting the issue at face value, Fast Response requires verification that suspect parts are contained, a disciplined root cause investigation is conducted, short-term and long-term solutions are considered, and updates are made to document process instructions and controls.
Manufacturing plants that use a Fast Response-like process discuss production issues during their daily production meeting to inform management and coordinate action plans to resolve issues and hold the gain with new questions in the relevant layered audit check sheet.
Interestingly, a highly effective LPA system actually incorporates key aspects of Fast Response. Ease Inc.’s Beacon LPA process performance platform has built-in functionality to trigger a nonconformance action. Just as with Fast Response, responsibility is assigned, mitigation status is monitored and open items are reported in a real-time management dashboard.
These three requirement excerpts illustrate how BIQS strategies can be integrated to provide fast and disciplined handling of issues at all levels resulting in continuous improvement across operations. LPAs hold process controls and desired human behaviors in place, FMEAs assess risk and causes upfront, and when an unanticipated problem occurs, Fast Response limits the exposure and drives actions to prevent recurrence. With those high-impact strategies from BIQS, a lot of waste, customer dissatisfaction and related operational and financial pain can be avoided.
Article written by The Luminous Group.