Three Reasons to Invest in Manufacturing Software to Streamline Processes
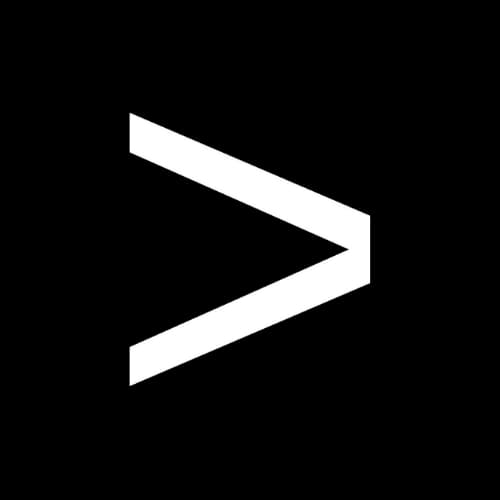
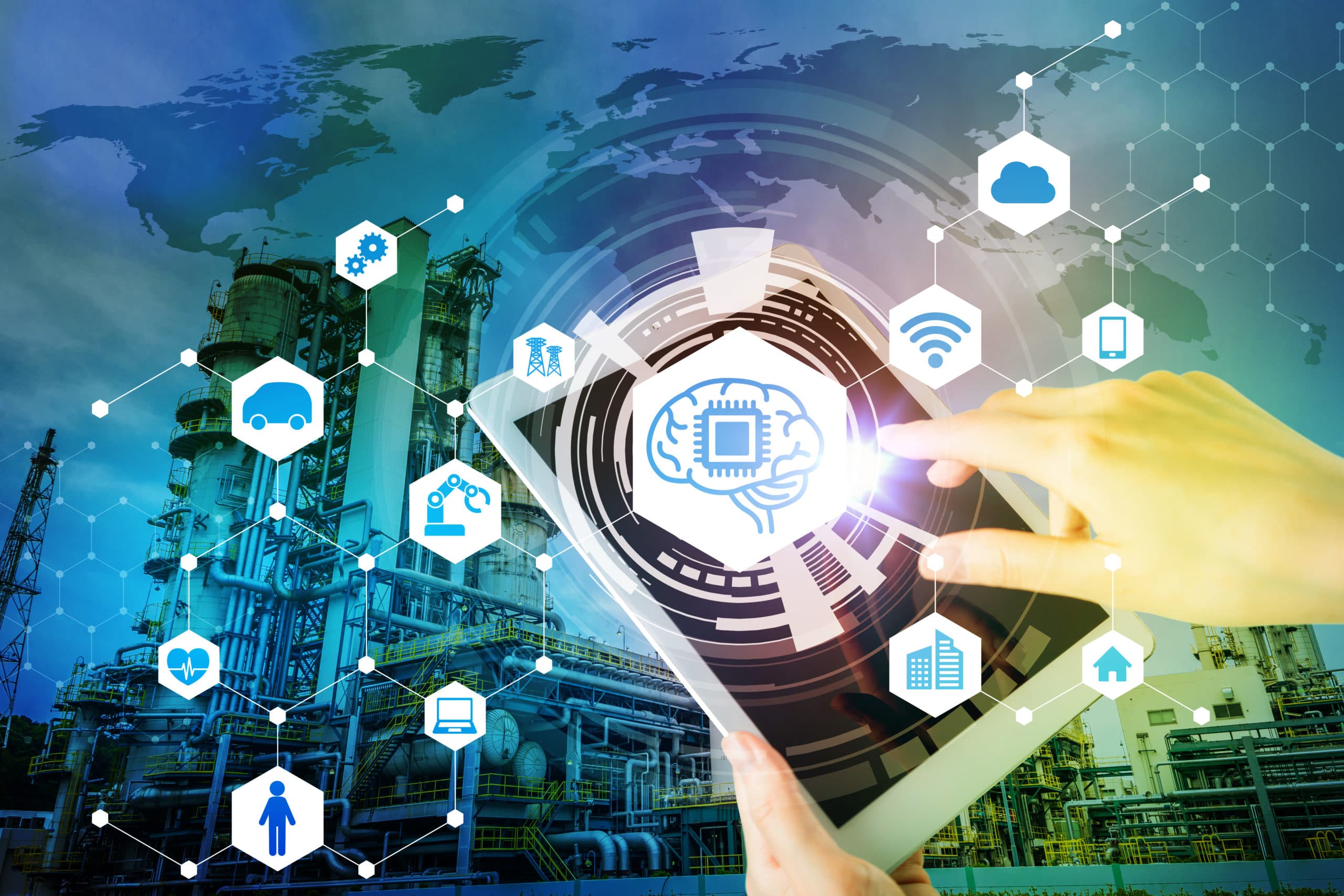
A few things in life are required—we simply have no choice but to do them—like paying taxes. Some quality managers would compare the often-mandatory requirement of completing layered process audits (LPAs) to calculating taxes—both are cumbersome and are easily forgotten once the requirement is met. But what if there was an effective solution to simplifying your LPA process and at the same time adding value to your organization?
LPAs are a sub-type of process audits; and they differ from generic process audits by requiring multiple people, including management, to conduct an ongoing chain of simple verifications to ensure that a defined process is followed correctly. LPAs provide an active view into operational process conformance and corrective actions as required by many end manufacturers (such as automakers) to maintain supplier quality. When implemented correctly, LPAs can help shape your organization’s culture into one that embraces continuous improvement. This powerful audit management methodology can:
- improve safety and quality,
- deliver cost savings by boosting problem-solving systems, and
- make continuous improvement nearly routine.
Unfortunately, some organizations complete LPAs only because they are required to do so by a customer. While such organizations do, in fact, fulfill their customer’s requirement, they are missing out on the rich benefits that LPAs can provide. In order to realize those benefits it’s worthwhile to consider manufacturing software options to streamline your LPA process by simplifying scheduling, utilizing real-time data, and closing the quality loop.
Simplify Scheduling
Much of the value of LPAs comes from building an effective layering system where you have fresh eyes conducting audits on a routine basis. You want to utilize a variety of employees—from shop floor operators to executives—to verify that standardized procedures are in place and are indeed being followed consistently. Try to schedule multiple layers of management—typically three, but at least two layers. Given the number of people involved in LPAs it can become time consuming to schedule so many audits efficiently.
You can reduce the administrative overhead associated with assigning and scheduling audits with software programs which ensure that all levels of staff from across the organization are participating in the LPA system. For example, manufacturing software allows you to easily build a schedule where first-level supervisors are performing audits on every shift while top-level management representatives, such as a plant manager, complete at least one audit per week.
Utilize Real-time Data
With paper-based audits, the results are difficult to view and share. Transferring your LPA results to an electronic format is labor intensive. Management software allows you to:
- view audit and inspection results in real time,
- compare current and historical results, and
- share reports throughout your organization.
Robust dashboard metrics that enable users to view reports in real-time help to maximize the value of your LPA audits by driving improvement to meet key performance measures. After all, monitoring metrics builds accountability across the organization.
Close your quality loop
A good LPA identifies non-conformances and provides a mechanism to correct or prevent problems that are systemic. Uncovering the reasons for why a nonconformance occurs is essential for developing effective recommendations for improvement. In most cases, you don’t know immediately what corrective actions are necessary to prevent an error from happening again and potentially affecting product quality. Generally, mistakes don’t just happen, but rather can be traced back to some well-defined causes.
Manufacturing software, by providing real-time data, helps uncover the root causes of a nonconformance. This up-to-the-minute reporting serves as the foundation for a robust corrective action and preventive action (CAPA) program—a key element in creating a culture of continuous improvement. When you are able to utilize your CAPA program to identify root causes, you can pinpoint opportunities for improvement and thus prevent problems before they affect production and your bottom line.
For an LPA to help close your quality loop it must be followed by a plan to implement and monitor corrective actions. With paper-based audits, nonconformances are easily lost in the paperwork shuffle. Manufacturing software allows you to build in follow-up audit questions to ensure that problem-solving solutions (corrective actions) are held in place to prevent your staff from fixing the same problem multiple times. This helps ensure the needed consistency and follow through between audit findings and corrective actions. Software provides the ability to easily follow up on corrective actions and delivers alerts when CAs are complete and the quality loop is closed.
Could your LPA program benefit from the use of manufacturing software?