Top OSHA Violations + Audit Questions to Prevent Them
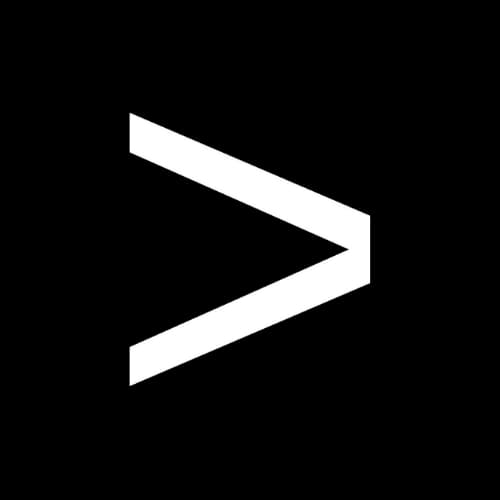
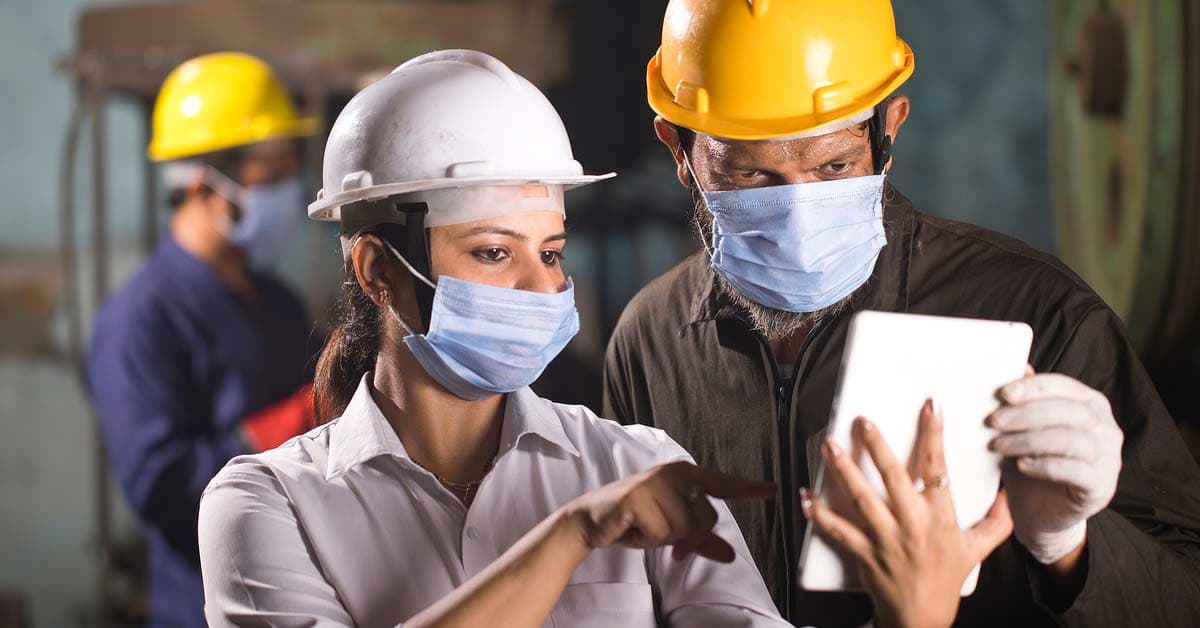
According to the U.S. Bureau of Labor Statistics, more than 420,000 non-fatal workplace injuries occur in manufacturing every year.
And while the pandemic has meant a lull in U.S. Occupational Health and Safety Administration (OSHA) inspections, the pace is likely to pick up under the new administration.
One positive for employers:
The list of top 10 OSHA violations doesn’t change much from year to year. That means if OSHA does pay you a visit, you can pretty much count on inspectors looking at these areas.
Checking compliance with the most common violations will help not only protect workers, but avoid fines and bad press. Below are common violations cited under each standard, plus sample questions you can use in plant floor safety audits and inspections to avoid them.
Learn how to promote a culture of safety with plant floor inspections
Hazard Communication
Every year, hazard communication is one of the top OSHA violations. The areas most cited under this standard are:
- Creating or providing a written hazard communication program
- Hazardous chemicals training
- Having the Safety Data Sheet (SDS) available for each chemical
- Chemical labeling
Based on these top findings, audit questions to check compliance could include:
- Are chemicals in this location labeled clearly?
- Can the employee find the SDS for chemicals at their work station?
- Can the employee describe how to respond to a chemical spill?
- Is there a written hazard communication program?
Lockout/Tagout
OSHA’s Lockout/tagout (LOTO) standard aims to stop injuries from hazardous energy release, for instance when a jammed conveyor belt suddenly starts moving again.
Common violations are not having procedures, lack of adequate training, not reviewing procedures and not using LOTO devices. Questions to ensure lockout/tagout compliance may include:
- Does the piece of equipment include a documented lockout procedure?
- Can the employee describe the lockout procedure for the piece of equipment?
- Has the LOTO procedure been reviewed in the past year?
- Does the employee follow the proper procedure to verify the machine was de-energized?
Powered Industrial Trucks
According to the National Safety Council, forklifts are responsible for nearly 1 in 10 occupational injuries with days away from work. The most common OSHA violations in this area are:
- Inadequate training
- Lack of regular inspections
- Defective equipment still in service until repair
- Lifting up workers unsafely
- Not having or using seat belts
With that in mind, questions you could ask to reduce forklift injuries include:
- Is the operator up-to-date on forklift training?
- Are daily forklift inspection checklists complete?
- Does the machine have any open work orders?
- Does the operator use the seat belt when running the forklift?
Machine Guarding
Poor machine guarding causes roughly 18,000 severe injuries every year, according to OSHA. In addition to not having the proper machine guards—or worse, not having them at all—misuse is also a problem.
Below are some audit questions to help protect workers:
- Do machine guards prevent body parts and objects from contacting dangerous moving parts?
- Are machine guards securely in place?
- Can the employee comfortably operate the machine with guards in place?
- Can the operator lubricate the machine with the guards in place?
Eye and Face Protection
Failure to provide eye and face protection is a serious safety issue. The National Institute for Occupational Safety and Health (NIOSH) says about 2000 workers suffer a work-related eye injury requiring medical attention every day. This can happen when objects or particles strike or scrape the eye, or from heat, chemicals or optical radiation (such as from welding).
Eye and face protection questions to ask on the plant floor include:
- Is the employee using proper eye and face protection?
- If there’s a hazard from flying objects, does the eye protection provide protection at the sides?
- If the employee wears prescription lenses, does the eye protection fit on top or have custom prescription lenses itself?
- Does the employee say that the eye protection is comfortable to wear?
- Does the eye and face protection fit well?
Keeping Tabs on Top Safety Issues
Regular safety audits and plant floor inspections are key to injury prevention. Just as important is actually taking action on what you find—and not letting problems persist.
Digital safety audits and inspections performed on a mobile device can help achieve this better than paper checklists. A mobile audit platform like EASE makes it simple to:
- Rotate and randomize questions for broad coverage
- Track and report on safety risks in real time
- Link inspection and audit failures to corrective actions to close the loop
- Upload photos to clarify questions and responses
Avoiding OSHA violations can’t be the main goal, of course. Being proactive about safety is about recognizing the human cost of workplace injuries and making sure each employee goes home to their family at night.
Making that goal a reality requires a closed-loop process to identify hazards, hold people accountable and check areas at risk for similar problems.