Why Tribal Knowledge Is a Problem for Manufacturing
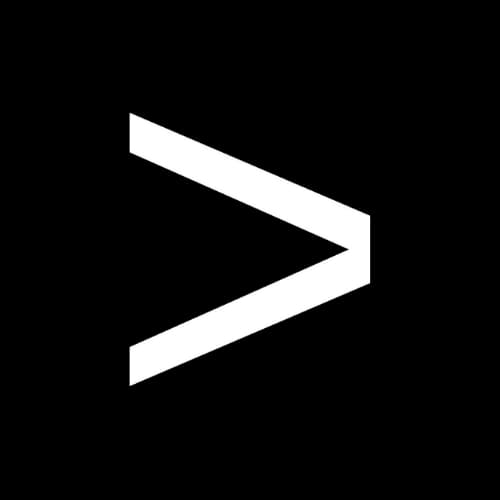
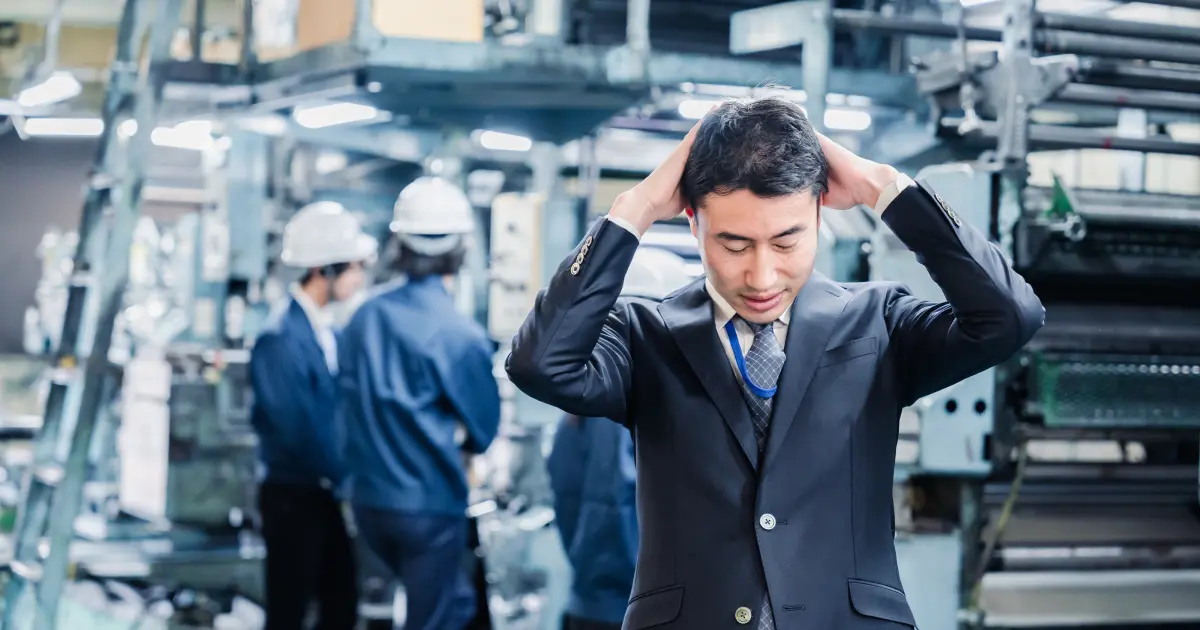
In every manufacturing plant, tribal knowledge exists behind the scenes that quietly keeps processes running more smoothly.
Imagine, for instance, a veteran operator who knows exactly how to troubleshoot equipment issues based on subtle machine indicators, a skill refined over years of work.
One big concern for manufacturers is the fact that the industry is quickly losing older, more experienced workers, who are often the custodians of this tribal knowledge.
The challenge then becomes capturing this information and turning it into standardized practices, so that the entire organization benefits—and essential information isn’t lost when workers leave.
Download your free Root Cause Analysis 101 Guidebook to learn about five common root cause analysis tools
What Is Tribal Knowledge?
Tribal knowledge refers to the unwritten best practices and insights veteran employees gain through years of on-the-job experience. In a manufacturing environment, tribal knowledge often includes technical information on how to run machines, troubleshoot processes or execute procedures. This knowledge exists outside of any documented processes, and is held only by individuals or certain groups of people.
Tribal Knowledge and the Manufacturing Brain Drain
Roughly one-third of today’s manufacturing workers are older than 55, according to analysis of BLS data by Deloitte. As these workers retire, they take with them decades of firsthand experience that is often essential to operational efficiency.
This loss of skilled labor is a central factor in the ongoing manufacturing skills shortage, and is exacerbated by continued struggles to attract and retain skilled workers. Large numbers of unfilled positions are expected to persist for years to come, which by 2030 may exceed 2 million open jobs.
According to survey data from the National Association of Manufacturers, a full 97% of manufacturers are concerned about the looming brain drain—and how it might reduce productivity and increase costs.
As the industry faces a tidal wave of knowledge loss, the question looms large: how can manufacturers capture and codify tribal knowledge to ensure the resiliency of their operations?
Strategies for Capturing Tribal Knowledge
Capturing tribal knowledge is fast becoming an integral part of mitigating the impact of the manufacturing brain drain. Those manufacturers who are proactive about turning tribal knowledge into documented practices are better positioned to adapt to the industry’s ongoing labor challenges.
Strategies here include:
- Surveying operators about common problems on the line and how they troubleshoot them
- Monitoring process data to identify operators or lines that are high performers (e.g., shorter cycle times or higher OEE) to determine why they are more efficient
- Observing each step of the process to find where people may have found better ways of working
- Soliciting feedback from experienced operators about practices they’ve developed over the years to make processes run more smoothly
Some workers may be hesitant to share their expertise if they’re worried about job security or getting reprimanded for using shortcuts. The key here is to reassure employees that they are vital members of the team, and not at risk of being let go. It’s also important that you’re open to reevaluating procedures where people have found more efficient ways of working, as long as quality or safety isn’t an issue.
Turning Tribal Knowledge Into Standardized Practices
Once you’ve identified tribal knowledge, next steps include incorporating that information into process documentation and standardizing new practices across the plant.
Digitizing your procedures, work instructions and standard operating procedures (SOPs) is an important starting point, providing a single source of truth for referencing essential information. Next, any changes need to be reflected in employee training. One way to do this is by turning process updates into microlessons or one-point lessons that can be shared on the plant floor.
Finally, you must take steps to verify the changes on the plant floor, without which documenting tribal knowledge is useless as people fall back onto old habits. Plant floor audit and inspection software like EASE can help by facilitating spot checks of key process changes. These checks also provide further opportunities to identify tribal knowledge where plant floor practices differ from documented standards.
Manufacturers today face an enormous challenge in capturing tribal knowledge before it is lost forever. To do it, organizations must prioritize a culture of communication and knowledge-sharing that involves actively seeking insights from experienced workers, and turning those insights into action on the plant floor.