Takeaways From Our Ultimate Guide to Layered Process Audits
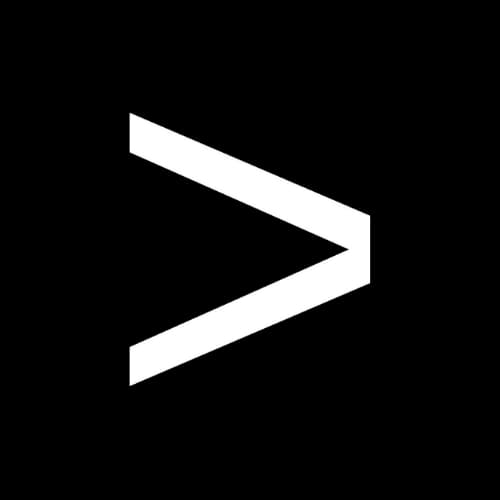
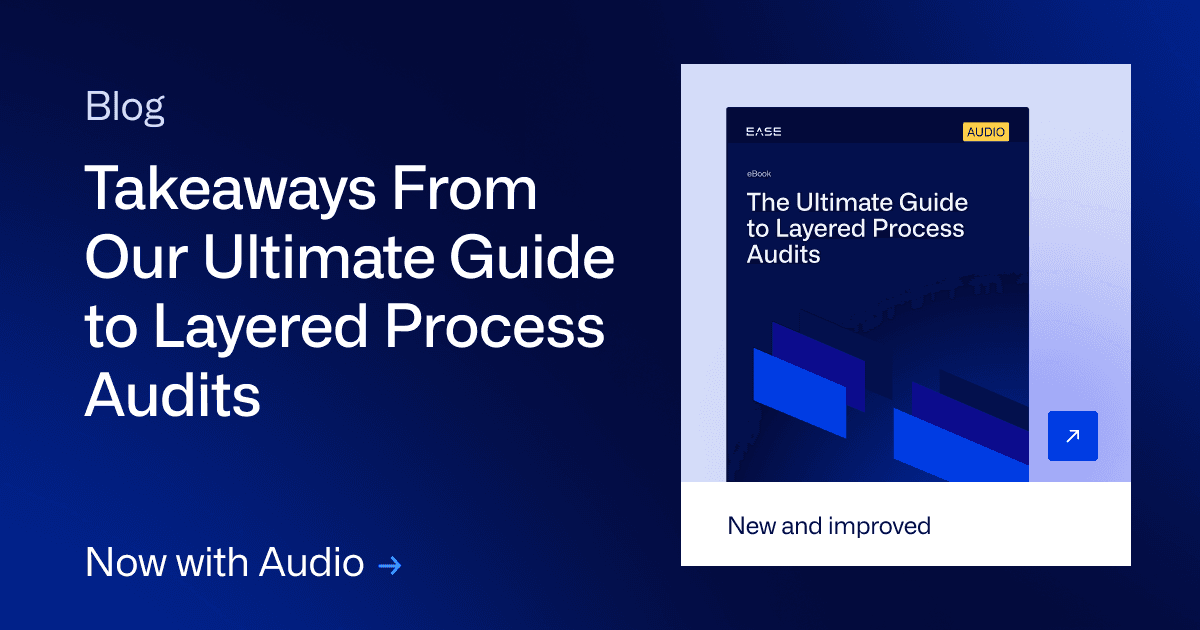
Prefer to listen to this post instead? Here’s the audio version:
Layered process audits: Done right, and they can transform your operation into a lean, efficient powerhouse. Done wrong, and your entire production can go downhill—fast.
Here are key takeaways from our 93-page, newly revised Ultimate Guide to Layered Process Audits. It’s the go-to resource for everything you need to know about LPAs and the right way to do them, but we know not everyone has time to read through the full guide. Consider this your CliffsNotes edition.
Chapter 1: What Are Layered Process Audits?
LPAs are short, frequent audits to make sure your processes are running as they should—think of it like a pre-flight checklist. You’re not inspecting the final product; you’re checking the process inputs to stop issues before they happen. Everyone gets involved, from the frontlines to upper management. LPAs are essential in industries like automotive, aerospace, and medical devices, where adherence to standards is everything and any defects can have serious consequences.
Chapter 2: Why Should You Conduct LPAs?
So, why are LPAs worth your time? Fewer defects, happier customers, and lower costs, among other critical operational and quality key performance indicators (KPIs). LPAs help you catch problems early, meaning less scrap, fewer complaints, and a lot less fire-fighting when things go wrong. As just one example, a global aerospace supplier reduced customer defects by over 50% by streamlining its quality audit process.
Done right, LPAs can boost your productivity and build a stronger culture of quality.
Grab your digital copy of our full, newly updated Ultimate Guide to Layered Process Audits, 2nd edition
Chapter 3: The LPA Implementation Process
Implementing LPAs is like building a house. Start with a solid plan. Form your LPA team, figure out where to begin, and set up your checklists. Then, train your auditors and roll it out step by step. LPAs shouldn’t be owned by the quality department alone—operations should drive it. Get management to check in regularly to keep everyone accountable.
Chapter 4: Management’s Role in LPAs
Management needs to lead by example: allocating resources, actively participating in audits, and holding everyone accountable. When leaders show up on the plant floor, it sends a strong message that quality matters. Without management’s support, LPAs will struggle to take off. (Check out our on-demand webinar: Why Management Communication is Critical to Learning from Process Audits)
Chapter 5: Top LPA Challenges
Like any good tool, LPAs come with their challenges. One hurdle is getting people to actually follow through. You’ve also got to make sure people aren’t just checking boxes without paying attention (i.e., pencil-whipping). And then there’s tracking follow-up corrective actions—because if you don’t, those problems aren’t going anywhere.
Chapter 6: How to Write LPA Questions—The Basics
It’s all about keeping it simple and focused on the process, not the end product. You want yes/no questions that trigger corrective actions if something’s wrong. Stay specific, avoid vague terms, and make sure your questions are directly tied to key process steps. A well-written question can make or break your LPA program. (Learn more: A 3-Step Method for Writing LPA Questions)
Chapter 7: Types of Questions to Include
Concentrate on the process inputs—things like operator qualifications, machine settings, and materials used. You’re digging into what’s happening on the plant floor, not just checking if paperwork is in order. Keep the questions relevant and make it interactive with photos and videos so that operators aren’t just going through the motions.
Chapter 8: Be Specific with Your LPA Questions
Every question should be a datapoint to improve a process. Instead of asking, “Is the machine running properly?” ask for specifics like, “Is the machine running between 600 and 620 RPM?” The more targeted and measurable your questions are, the more valuable your audits will be.
Chapter 9: Rolling Out LPAs to Your Plant
Rolling out LPAs isn’t as simple as flipping a switch; you need a plan. Start with training your auditors and making sure everyone understands the “why” behind LPAs. Then, get employees on board by showing them how LPAs help them in their daily work. Finally, run mock audits to work out any kinks before going live.
Chapter 10: Audit Best Practices
Conducting a good audit is more than just checking a list. Auditors need to engage with operators, explain why they’re asking certain questions, and take the time to listen. Record both the good and the bad—and even if you fix a problem on the spot, mark it as a nonconformance so it gets tracked. The human element is key here; how you interact makes all the difference.
Chapter 11: Creating the Reaction Plan
When a nonconformance pops up, you need a plan. The reaction plan tells you what to do next: contain the issue, mitigate it, and, if needed, assign corrective actions. The goal here is not just to patch things up, but to get to the root cause so the problem doesn’t happen again. Avoid the “it’s just human error” excuse.
Chapter 12: Updating Your Question Library
Your LPA question library isn’t a set-it-and-forget-it situation. You need to update it regularly based on corrective actions, customer feedback, and any new risks that come up. If a question keeps passing 99% of the time, consider scaling back its frequency. Keep things fresh and relevant.
Chapter 13: Strategies for Improving LPA Results
If your LPAs aren’t delivering value, it’s time to take a closer look. Are you doing enough audits? Is leadership participating? Are you tracking the right metrics? Sometimes, overcoming resistance is just a matter of showing the team how LPAs help them, not just the company. And remember, it’s all about continuous improvement. (Learn more: Questions to Ask When Benchmarking Your Layered Process Audit Program)
Chapter 14: Increase Efficiency with LPA Software
Digital LPAs are a game changer. Going paperless helps with scheduling, tracking, and getting real-time data, which is essential if you want to make LPAs work on a larger scale. Digital tools can help you spot trends, close the loop on issues faster, and reduce the risk of pencil-whipping.
Chapter 15: Improve Checklists with LPA Software
Using digital audit software to manage your LPAs lets you customize questions, randomize audits, and even add photos for extra clarity. This makes it easier to track conformances and nonconformances across your plant. By keeping things dynamic, software can also prevent repetitive audits that don’t add value.
Chapter 16: LPA Dashboards for Analysis
Digital dashboards are your secret weapon for tracking LPA effectiveness. They help you visualize trends, track metrics like audit completion rates, and see where your nonconformances are coming from. Use dashboards to monitor the health of your LPA system and keep everyone accountable. If you’re not measuring, you’re guessing.
Chapter 17: The Role of LPAs in Quality Maturity
LPAs are a stepping stone to higher levels of quality maturity. As you improve your LPA process, you’ll move from basic operator-driven actions to a culture of zero defects, where quality is baked into everything you do. This is the long-term goal for any manufacturing operation serious about quality: Getting to that “zero defects” mindset.
And there you have it: Your quick hit, section-by-section rundown of our Ultimate Guide to Layered Process Audits. LPAs are one of the most powerful tools you can add to your quality toolbox, and a key component to creating a culture of quality across your sites. Do them right, and watch your quality output soar.