Understanding OSHA’s Hierarchy of Controls in Safety Management
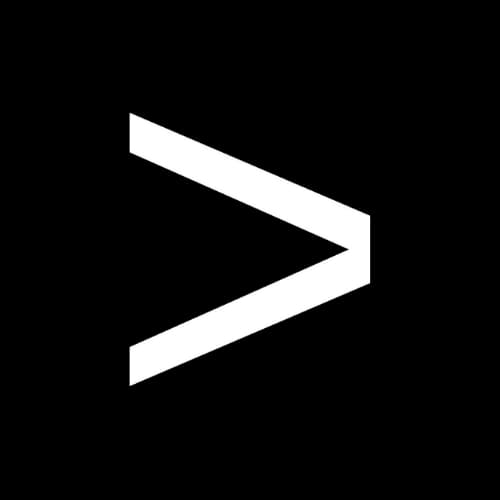
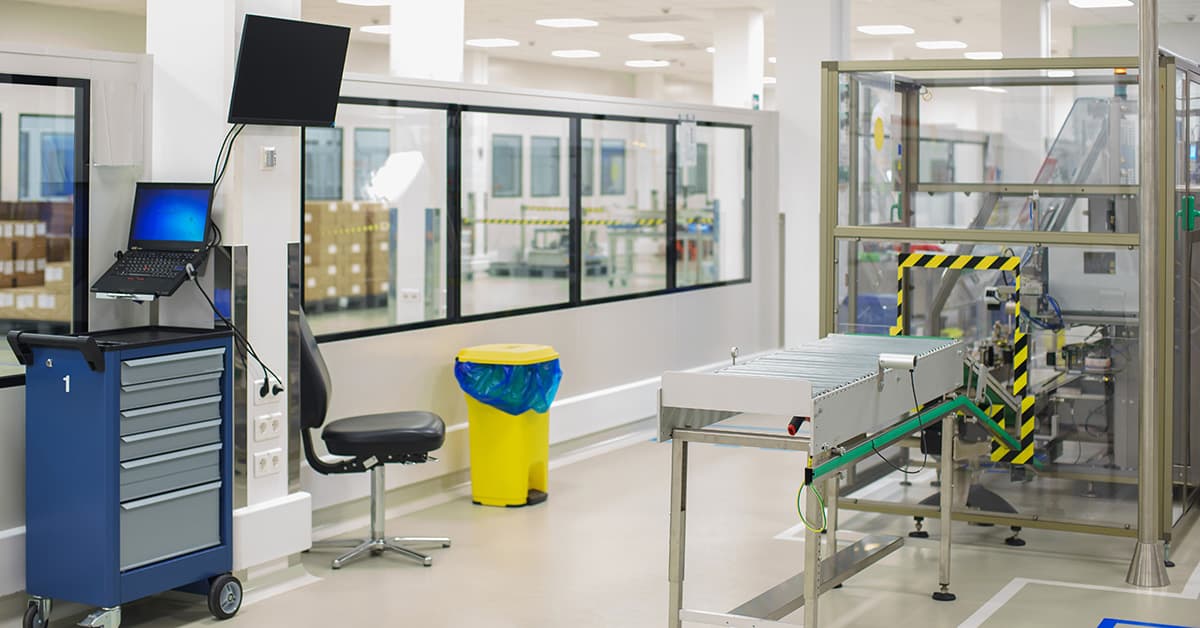
When COVID-19 first began to ripple across the globe, employers everywhere scrambled to put in place new controls to reduce transmission risk.
The world underwent a massive shift towards remote work, eliminating in-person interactions wherever possible. Companies with onsite workers began to stagger shifts and reorganize manufacturing floors to minimize contact among workers. Employers upgraded ventilation systems and sanitation practices, and they also installed Plexiglas barriers. Finally, they implemented new rules around masking in the workplace to minimize viral spread.
These actions are all a perfect example of OSHA’s hierarchy of controls. The agency recommends using the hierarchy of controls to focus on the highest impact controls, improve safety management and reduce workplace injuries and illnesses.
Today we’re looking at the different levels in the hierarchy of controls, exploring each type of control and the one thing you must do for controls to work.
What Is OSHA’s Hierarchy of Controls?
The hierarchy of controls describes the order in which different injury and illness prevention methods should be used. The most effective methods are at the top, while the least effective are at the bottom.
There are five levels of controls:
- Elimination
- Substitution
- Engineering controls
- Administrative controls
- Personal protective equipment (PPE)
Elimination
The most effective way to mitigate a hazard is to eliminate it entirely. Elimination should always be the first priority, since that’s the only way to truly provide a workplace “free from recognized hazards” as OSHA’s general duty clause mandates.
Some examples of elimination include:
- Reworking a process so that work is done at ground level rather than at height to eliminate fall hazards
- Eliminating a sampling step at a hazardous location and conducting sampling elsewhere
- Removing a dangerous machine part
- Replacing a faulty tool that’s a risk to workers
Practically speaking, elimination is typically simplest at the design phase. In an existing process it can be far more complicated and expensive, especially if it involves reworking the process or replacing equipment.
Substitution
If you can’t remove a hazard altogether, your next best option is substitution. The classic example is replacing a hazardous chemical with a less hazardous one, for instance using alcohol as a solvent in place of benzene or toluene. Again, this may be easier to do at the product or process development phase.
Engineering Controls
Engineering controls focus on isolating workers from a hazard through changes to the work environment. Engineering controls work better than administrative controls and PPE because they do not rely on employee behavior.
Examples of engineering controls include:
- Adding an overhead balancer for a tool to reduce strain on workers
- Upgrading ventilation systems and adding Plexiglas dividers to prevent COVID-19 spread
- Using an exhaust system to remove welding fumes
While higher in cost than administrative controls and PPE, engineering controls can reduce long-term operating costs, according to NIOSH. The agency maintains a database of engineering controls that manufacturers can use to search specific hazards and find proven solutions.
Administrative Controls
Administrative controls are aimed at changing work practices to reduce risks to workers. Examples include changes such as:
- Staggering shifts in a plant to reduce density of workers on the line
- Reducing exposure time for workers to a specific hazard
- Installing alarms or signage to warn employees
- Using the buddy system for confined space entry
Personal Protective Equipment (PPE)
If you can’t completely design out a hazard or isolate workers from it, PPE is your last line of defense. It’s the least effective of all the control types, in part because it relies on individual compliance.
OSHA points out the importance of not implementing new controls that inadvertently create new hazards, for instance if workers can’t hear alarms due to hearing protection PPE.
Verifying Controls to Close the Loop
Hazard identification and implementing controls is only half of the risk management process. A closed-loop process also requires verification on the plant floor to check that controls are in place and working.
Hazard prevention plans amount to nothing if people aren’t actually following them on the plant floor. It’s easy to find examples of this all the time. Multinational companies with whole departments staffed full of safety people regularly have incidents where basic safety measures were ignored.
Plant floor safety inspections are a key tool for preventing this problem, showing people that leadership cares enough to show up in person to verify safety protocols. Rather than getting bogged down in paperwork, however, an automated platform like EASE makes plant floor checks simple and easy, so you can quickly verify:
- Controls have been implemented
- Any new engineering controls installed are functioning properly
- Employee knowledge of engineering controls, safety practices and PPE usage
- Preventive maintenance plans are being followed to prevent equipment malfunction
The hierarchy of controls provides a risk-based approach to addressing safety risks in the most effective way possible. Making this a reality, however, requires a robust verification system to determine whether those controls are working. Only with this piece do you have the data to make the right adjustments, completing the loop of the Plan-Do-Check-Act process.