Using Layered Process Audits to Drive Continuous Improvement: 3 Examples
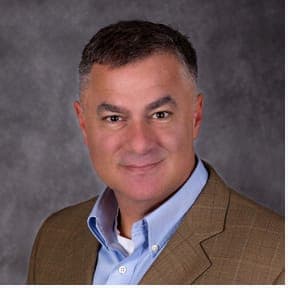
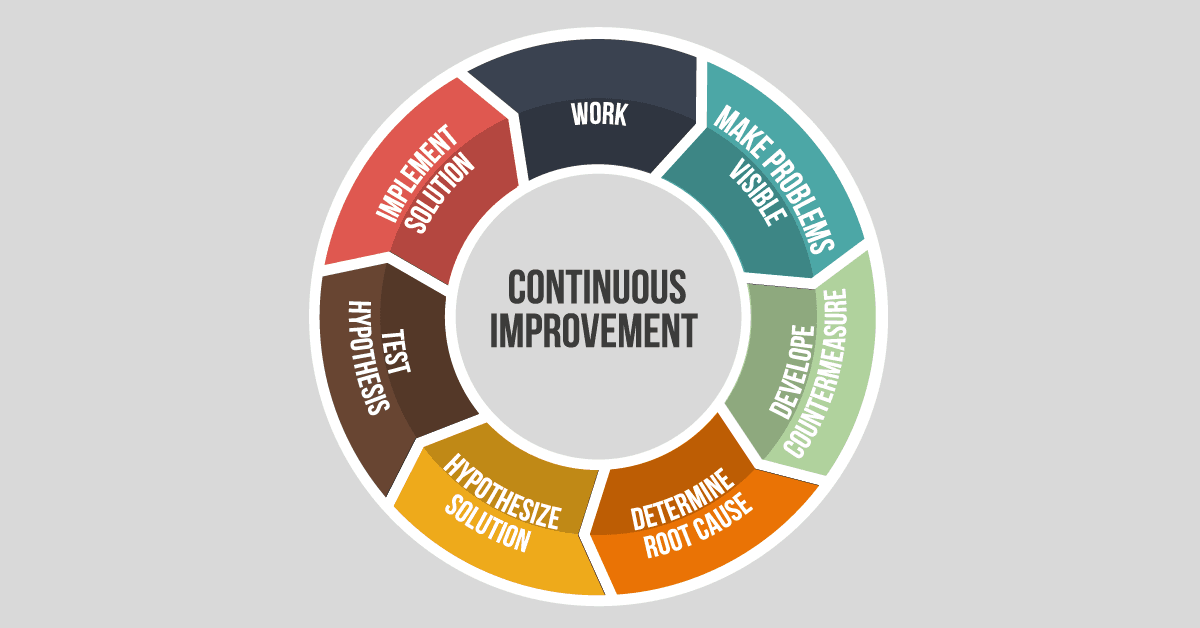
Layered process audits are a first-line defense against variation that leads to product defects and customer complaints. In fact, many manufacturers implement them in direct response to customer-specific requirements, particularly in the automotive industry.
However, companies that implement these high frequency audits as part of a commitment to quality rather than to meet compliance are likely to get more out of them.
One key example: finding continuous improvement opportunities that might otherwise go unnoticed.
Here we explore three examples of how plants have used layered process audits (LPAs) to drive continuous improvement. We also look at how technology can help uncover these opportunities, and why face-to-face interactions are so important to the process.
Download your free Ultimate Guide to Layered Process Audits for more LPA question best practices, examples and tips
Finding 5S Improvements
Layered process audits provide a mechanism for capturing operator feedback that leads to continuous improvement opportunities. The operator’s perspective is critical, acting as a window into plant floor conditions that can’t be replicated in conversations among management alone.
In one example, a plant installed a screw dispensing machine as a poka-yoke device to ensure operators received the exact number of screws needed in the assembly process. The problem was that the tray at the bottom of the machine was too flat. When the operator hit the button, the machine would dispense four screws, but one would often slide off the tray onto the floor.
The result is that the work area had screws on the floor, an obvious 5S issue. Operators stopped using the machine, defeating the purpose of the poka-yoke device. A 5S question during an LPA identified that there were components on the floor.
Asking the operator how the screws were ending up on the floor led to the bigger finding that operators had changed the process. A poka-yoke that was supposed to be in place was not! A hidden risk was identified. Talking to the operator about why they weren’t using the machine led to a more effective solution: installing a deeper dish to catch all the screws.
Understanding Safety Behaviors
Reducing safety incidents relies on individual behavior, something where LPAs provide data and a deeper understanding of behavior to improve compliance. In particular, LPAs provide opportunities to dig into why operators aren’t following safety procedures. For example, why aren’t people using personal protective equipment (PPE) as required? Is there a barrier that needs to be addressed by management?
In one plant, a photo captured during an LPA provided added detail that led to a more permanent corrective action. During the audit, a question on whether there were any trip hazards uncovered an extension cord going across a work cell. Rather than just fixing the problem, the auditor flagged the issue and included a photo of the work cell.
What the team learned during root cause analysis is that the operator was using a plug-in drill rather than the battery drill defined in the standard. This type of variation could cause product variation in addition to the safety concern. It turned out that the operator liked the corded drill because it was lighter. As a result, they installed an overhead balancer to address the operator’s concern and ensure the right tool was used. Without the LPA photo to identify the issue—and asking for feedback from the operator—they would not have been able to address the true root cause.
Uncovering Larger Trends
LPA responses are a primary source of data that companies can use to improve not just a single process, but also processes plantwide.
One manufacturer, for example, created a system for identifying systemic issues by asking LPA questions that fail in one area across all related machines. By using a dynamic question bank with custom tags, failed questions are tagged for inclusion in all plant checklists. This process allows them to connect the dots between issues that may be occurring at multiple workstations, rather than treating each as an isolated incident.
If you’re using an automated LPA platform, consider creating groups of tags by:
- Process-specific questions
- Safety questions
- Questions that address 6M inputs
- Continuous improvement questions to ensure gains are held in place
- 5S questions
This approach helps identify deeper trends by allowing you to see, for example, if you have a number of issues in a particular process area related to materials (6Ms). In other cases you might see a large number of failures tagged both stamping press and man (6Ms).
LPAs act as a critical process for capturing plant floor data you can use for continuous improvement. Just as important, they provide frequent checks to ensure teams are holding those improvements in place.
LPA software like EASE helps find more of these opportunities, providing data and details not captured in manual audits. Audit photos, custom tags and the ability to create process-specific checklists all help uncover what’s really happening on the plant floor. These insights combined with one-on-one interactions are key to implementing more effective—and permanent—improvements.