Using Layered Process Audits to Link Quality, Operations and Engineering
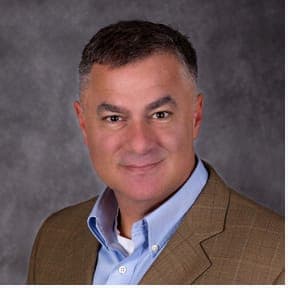
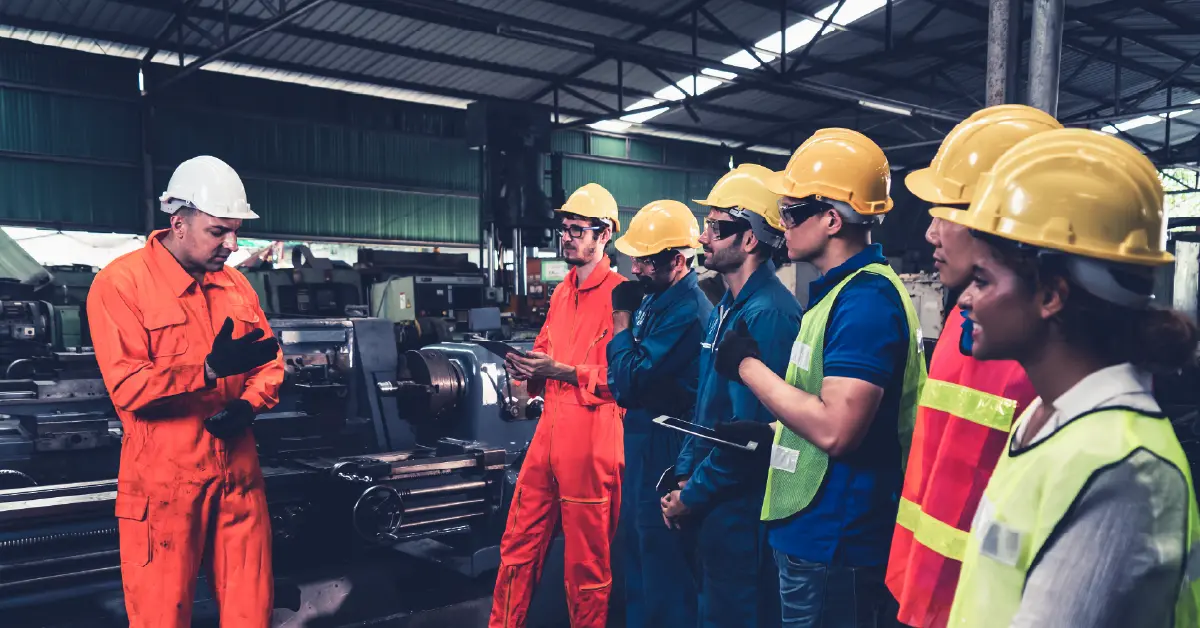
Layered process audits (LPAs) are a high-frequency auditing tool used by many in automotive and other industries to prevent process errors and manufacturing defects.
Mandated by OEMs like General Motors and Ford, these daily audits also provide a wide range of other benefits related to creating a culture of quality. One not often talked about, however, is the crucial role they play in connecting quality, operations and engineering.
Let’s take a look at how this works and why it’s so important, as well as the bigger picture of how LPAs improve communication both internally and externally.
Download your free Ultimate Guide to Layered Process Audits for more LPA question best practices, examples and tips
Quality: Bridging the Gap Between Operations and Engineering
At The Luminous Group, we tell clients to imagine a triangle with engineering, operations and quality representing the three points. Engineering writes the standards, while operators are supposed to follow those standards. In most manufacturing organizations, these groups are siloed, which creates opportunities for problems.
Consider, for example, that you have front-line operators who may not have the tools they need to do the job. The standards created by engineering also might not accomplish what they were originally created to do. From a quality perspective, you need to understand what those things are to prevent issues that could impact customers or worker safety.
Quality, then, must bridge the gap with systems to check whether standards are being followed on the plant floor—and that the standards themselves are working.
The Role of Layered Process Audits
LPAs help close the communication gap between operations, quality and engineering by facilitating conversations on the plant floor where the work actually happens.
When the process results in an unacceptable product, the first thing engineering wants to know is whether the operator followed the standard. LPAs give you confidence that the standard was followed. If you know this to be true and the result was still unacceptable, you need to look at whether the standard itself is sufficient.
In some cases, LPAs might reveal that the standard requires operators to perform tasks that are difficult if not impossible. This can be for many reasons, such as not being able to get the job done in time. Or maybe the standard requires them to attach a bolt in a blind installation.
For example, let’s say an operator must assemble four nuts on a part, only three of which are visible. During an LPA, the auditor sees that the operator only assembles three of them. When they ask why, they discover that the operator can’t see the location for the fourth nut.
In other situations, LPAs can help operations communicate with engineering when standards are difficult or even dangerous. When engineering goes to the plant floor for their audits, the standard is no longer theoretical. Instead, engineering can actually see people do the work, allowing them to make continuous improvements to the standard.
The Bigger Picture
In a larger sense, LPAs go beyond just facilitating communications between quality, operations and engineering. They also help create a culture of quality by building connections with:
- Other departments: When LPAs involve auditors from departments such as human resources, finance and logistics, it makes quality part of everyone’s job description. This can also help identify other areas for improvement, such as if a buyer finds a more efficient way to package components from a supplier.
- Company leadership: Having plant managers and even visiting CEOs conduct audits demonstrates leadership’s quality commitment and makes operators feel valued. Often, leaders can also bring fresh eyes to problems or identify inefficiencies.
- Customers: LPAs create a record that quality can use to communicate with the customer. This could be responding to a customer problem-solving issue, for instance, or showing the customer you’re meeting their needs by checking the line daily after changing an assembly process.
For many manufacturers, a digital platform like EASE has proven to be a game-changer when using LPAs to create more connected frontline workers and reinforce a culture of quality. Automated scheduling, reminders and a mobile app make it simple to conduct audits, so you can make sure audits are completed on-time and accurately. Robust reporting and custom dashboards also increase visibility, making it easy to share findings, identify trends and track issues.
LPAs have long been used in manufacturing to reduce defects and customer complaints. However, they also play a critical role in connecting quality, operations and engineering. Bringing these groups together not only ensures standards are being followed on the plant floor, but that the standards themselves are sufficient to create high quality products safely.