What Are Good Manufacturing Practice (GMP) Guidelines? What Manufacturers Need to Know
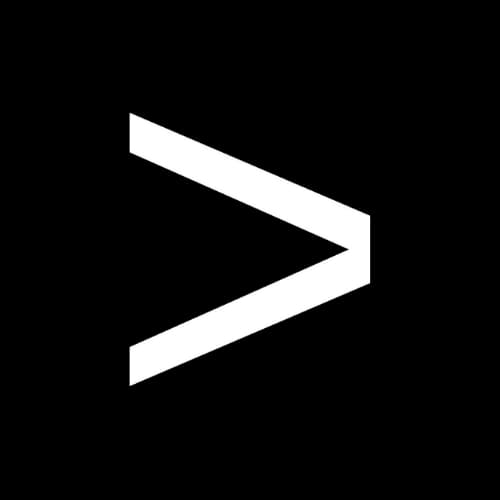
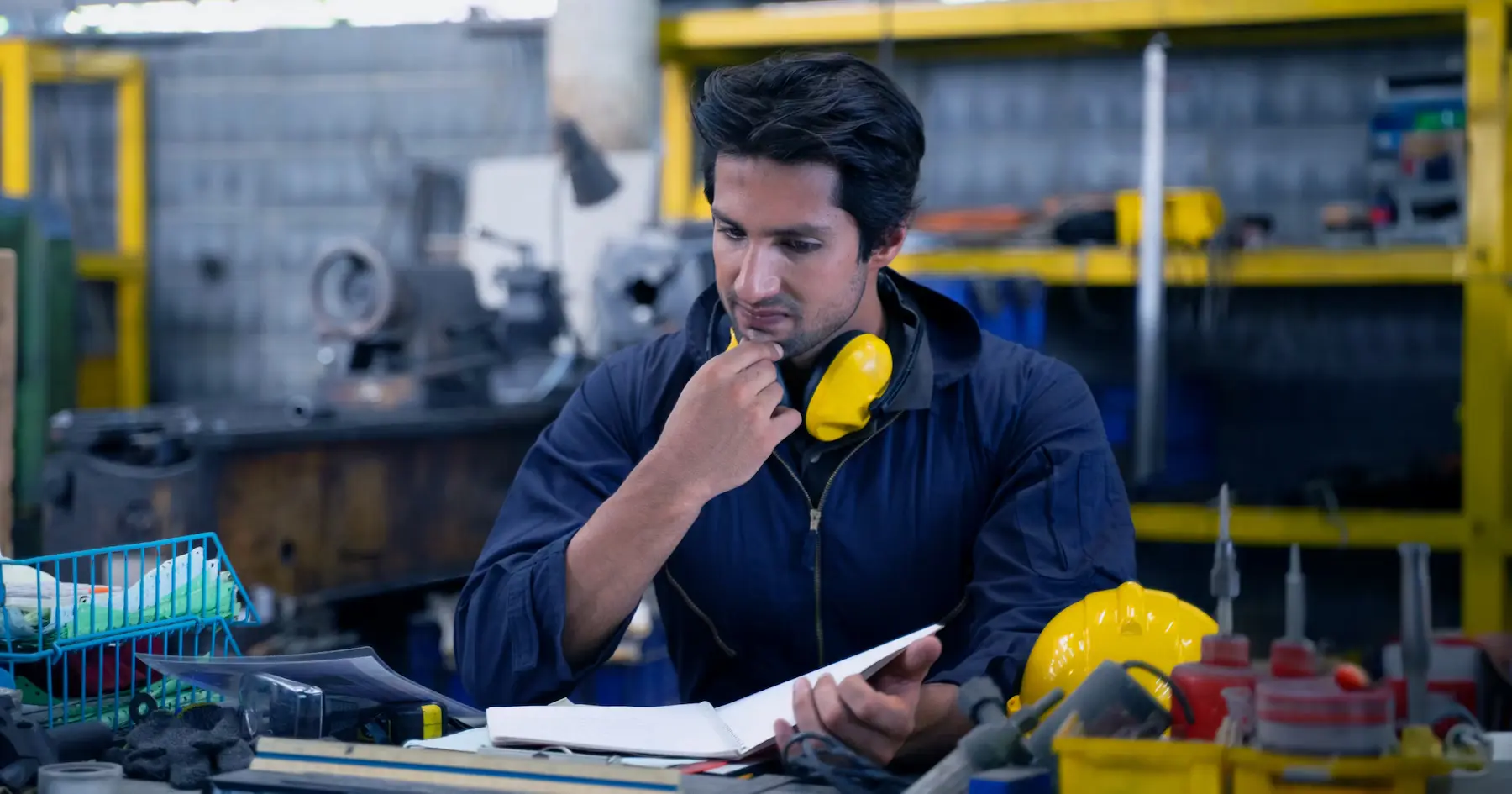
Food and Drug Administration (FDA) inspections are on the rise, with domestic inspections for medical devices jumping 144% in 2023 compared with 2022 according to The FDA Group.
Form 483 observations issued to pharmaceutical and medical device companies also more than doubled over that time, with Good Manufacturing Practice (GMP) violations a central focus.
So what are GMP guidelines, and what do manufacturers need to know to ensure GMP compliance?
Here we give a basic overview of GMP guidelines, including:
- Why GMP compliance is important
- GMP guidelines for medicines, medical devices, cosmetics, and food
- The 5 Ps of GMP
- Common GMP violations and how to avoid them
Download your free eBook on Cost of Quality: The Hidden Truth About Your Ultimate Quality Metric
What Are Good Manufacturing Practice Guidelines?
Good Manufacturing Practice (GMP) is a set of FDA requirements that apply to manufacturers of pharmaceuticals, medical devices, processed food, and dietary supplements. Also referred to as current good manufacturing practice or cGMP, the regulations aim to ensure products are consistently produced and controlled, as well as safe and effective, covering aspects of manufacturing such as:
- Process documentation and validation
- Quality control
- Employee training
- Sanitation and maintenance
GMP vs. cGMP: What’s the Difference?
The open-ended nature of GMP requirements provides flexibility for manufacturers in terms of how they implement controls in the manufacturing process.
However, the “c” in cGMP points to the fact that manufacturers must use updated equipment and systems to ensure compliance with GMP regulations. Specifically, current means that technologies that may have been cutting-edge in decades past may not be enough to meet today’s evolving risks.
Why GMP Regulation Compliance Is Important
GMP compliance is important from a number of perspectives, including:
- Consumer safety: Adhering to GMP helps reduce the risk of product contamination for consumers.
- Product quality:Following these requirements ensure that products meet quality standards, helping reduce errors, defects, and complaints.
- Avoiding regulatory violations: GMP violations can result in steep fines and penalties, and even jail time in the most egregious cases.
- Market access: GMP compliance is necessary to distribute certain products like drugs and medical devices in the U.S. and other countries.
- Brand reputation: Detailed GMP violations are published in FDA warning letters, leading to lasting brand damage for companies cited.
Pharmaceutical GMP Guidelines
The bulk of FDA’s actionable requirements around GMPs for pharmaceutical products are found in 21 CFR Part 211: Current Good Manufacturing Practice for Finished Pharmaceuticals. Special requirements for positron emission tomography (PET) drugs are also found in 21 CFR Part 212.
21 CFR Part 211 covers numerous individual requirements on nearly a dozen topics related to the manufacturing process, which are summarized in the table below.
Subpart | Topics covered |
Subpart B | Organization and Personnel · Responsibilities of quality control unit · Personnel qualifications · Personnel responsibilities · Consultants |
Subpart C | Buildings and Facilities · Design and construction features · Lighting · Ventilation, air filtration, air heating and cooling · Plumbing · Sewage and Refuse · Washing and toilet facilities · Sanitation · Maintenance |
Subpart D | Equipment · Equipment design, size and location · Equipment construction · Equipment cleaning and maintenance · Automatic, mechanical and electronic equipment · Filters |
Subpart E | Control of Components and Drug Product Containers and Closures · Receipt and storage of untested components, drug product containers and closures · Testing and approval or rejection of components, drug product containers and closures · Use of approved components, drug product containers and closures · Retesting of approved components, drug product containers and closures · Rejected components, drug product containers and closures · Drug product containers and closures |
Subpart F | Production and Process Controls · Written procedures; deviations · Charge-in of components · Calculation of yield · Equipment identification · Sampling and testing of in-process materials and drug products · Time limitations on production · Control of microbiological contamination · Reprocessing |
Subpart G | Packaging and Labeling Control · Materials examination and usage criteria · Labeling issuance · Packaging and labeling operations |
Subpart H | Holding and Distribution · Warehousing procedures · Distribution procedures |
Subpart I | Laboratory Controls · Testing and release for distribution · Stability testing · Special testing requirements · Reserve samples · Laboratory animals · Penicillin contamination |
Subpart J | Records and Reports · Equipment cleaning and use log · Component, drug product container, closure and labeling records · Master production and control records · Production record review · Laboratory records · Distribution records · Complaint files |
Subpart K | Returned and Salvaged Drug Products |
Medical Device GMP Guidelines
Medical device GMPs are regulated by the FDA under 21 CFR Part 820, also known as the medical device Quality System Regulation (QSR). Containing 15 subparts, the QSR is a complex standard that defines quality system requirements at each stage of the medical device manufacturing process. Below, we summarize some of the topics covered in the QSR.
CFR Title | Subject |
Subpart B | Quality System Requirements · Management responsibility · Quality audit · Personnel |
Subpart C | Design Controls |
Subpart D | Document Controls |
Subpart E | Purchasing Controls |
Subpart F | Identification and Traceability |
Subpart G
|
Production and Process Controls · Inspection, measuring, and test equipment · Process validation |
Subpart H | Acceptance Activities |
Subpart I | Nonconforming Product |
Subpart J | Corrective and Preventive Action |
Subpart K | Labeling and Packaging Control |
Subpart L | Handling, Storage, Distribution and Installation |
Subpart M | Records · Device master record · Device history record · Quality system record · Complaint files |
Subpart N | Servicing |
Subpart O | Statistical Techniques |
Note that in February 2024, FDA issued a final rule incorporating by reference ISO 13485, harmonizing FDA requirements with the framework used worldwide to ensure medical device quality. This rule goes into effect in February 2026, until which point manufacturers must comply with the QSR.
Cosmetics GMP Guidelines
FDA has released draft guidance around GMPs for cosmetics, which does not constitute enforceable requirements but rather the agency’s recommendations for cosmetics manufacturers.
That said, the Food, Drug and Cosmetic (FD&C) Act gives the FDA the right to inspect cosmetics manufacturers facilities to determine whether products may be adulterated or misbranded.
To help manufacturers avoid violations, the agency points specifically to inspection guidelines excerpted from its Inspection Operations Manual that companies can use for internal inspections.
The table below summarizes some of the topics covered in potential FDA inspections of cosmetics manufacturing facilities.
Buildings and Facilities | · Design and construction · Surfaces · Fixtures, ducts and pipes · Lighting and ventilation · Water supply, washing and toilet facilities, floor drainage and sewage systems |
Equipment | · Design and materials · Utensils, transfer piping and contact surfaces · Portable equipment and utensils |
Personnel | · Education, training and qualifications · Attire · Restriction of food, drink and tobacco use from manufacturing areas |
Raw Materials | · Storage and handling · Containers and labeling · Material sampling and testing |
Production | Written instructions and procedures for · Equipment condition · Material approval · Sampling · Weighing and measuring · Identification of equipment and transfer lines · Label examination · Finished product packaging · Returned cosmetics |
Laboratory controls | · Testing of raw materials, in-process samples and finished products · Sample retention, storage and retesting · Water supply testing |
Records | · Incoming materials · Batch records · Finished product sampling and testing · Distribution |
Labeling | · Name and contents · Warnings · Other information including ingredients and safe use |
Complaints | · Complaint files · Details on reported injuries and medical treatment |
Food GMP Guidelines
FDA CGMPs for food are established in 21 CFR Part 117, alongside new hazard analysis and risk-based preventive controls for human food requirements in the Food Safety Modernization Act (FSMA). Food CGMPs apply to manufacturers, processors, and anyone who packages or holds food. They also apply to activities like juice manufacturing and seafood processing that are otherwise exempt from requirements around preventive controls.
The table below summarizes the food requirements found in 21 CFR Part 117, as well as Hazard Analysis and Risk-Based Preventive Controls requirements.
CFR Title | Subject |
Subpart B: CGMPs | · Personnel · Plant and grounds · Sanitary operations · Sanitary facilities and controls · Equipment and utensils · Processes and controls · Warehousing and distribution · Holding and distribution of human food byproducts for use as animal feed · Defect action levels |
Subpart C: Hazard Analysis and Risk-Based Preventive Controls | · Food safety plan · Hazard analysis · Preventive controls · Recall plan · Preventive control management components · Monitoring · Corrective actions and corrections · Verification · Validation · Verification of implementation and effectiveness · Reanalysis |
Subpart G: Supply Chain Program | · Responsibilities of the receiving facility · Using approved suppliers · Supplier verification activities · Supplier audits · Supply chain program records |
The 5 Components of GMP
Viewed in total, GMP spans hundreds of requiViewed in total, GMP spans hundreds of requirements that manufacturers must comply with to avoid regulatory action by the FDA. While the requirements vary by industry, they can be distilled into five main components, also called the 5 Ps:
- People
- Premises
- Products
- Processes
- Procedures
Let’s look at each of these in more detail and why they are important to GMP compliance.
1. People
People are the foundation of GMP, as they are responsible for ensuring the other elements are executed correctly and consistently.
Are your people adequately trained? Do they have the knowledge, skills, and qualifications required for their role? It is essential that staff be fully trained in GMP requirements and their specific responsibilities under those requirements.
2. Premises
Keeping your manufacturing facilities clean and in good working order is critical to preventing product contamination and quality issues. GMP regulations in this area focus on several different elements:
- Facility design and construction
- Maintenance
- Sanitation
- Environmental conditions
Note here that for FDA purposes, the agency doesn’t need to prove that products themselves are adulterated. Rather, they only need to prove that conditions exist such that products could be contaminated or adulterated, putting the onus on manufacturers to keep their facilities up to standard.
3. Products
Incoming quality of materials is a key component of product safety and efficacy. Here GMP criteria focus on activities such as:
- Developing and implementing testing programs for ingredients
- Establishing robust supplier qualification programs
- Performing supplier audits
- Monitoring supplier performance
4. Processes
GMP compliance requires that manufacturers:
- Document all of their processes
- Validate those processes
- Verify that employees follow documented processes
Companies must document both their manufacturing and quality processes, something that is a common violation in FDA warning letters and ISO audits.
5. Procedures
Work instructions and standard operating procedures (SOPs) must also be documented and reviewed at least annually. Procedures should also be reviewed and updated as necessary as part of root cause analysis, corrective and preventive action (CAPA), and change management processes.
Comply with GMP with These Essential Tools
GMP compliance is no straightforward task and requires coordination among individuals across the organization. The most essential ingredients for GMP compliance, however, can be boiled down to the following:
- Quality management system: Manufacturers need to be able to show that they have a well-organized quality management system that prevents mix-ups and potential contamination in the manufacturing process. In terms of FDA inspections, companies with digital systems will be better positioned to demonstrate a stronger compliance posture compared with disorganized paper records or spreadsheets.
- Process documentation: All processes, from manufacturing processes to overarching quality processes themselves, must be documented. This provides the basis for standards against which plants can verify that they are meeting GMP criteria.
- Employee training: A well-trained staff is crucial to GMP compliance. It’s worth noting that training shouldn’t be a one-time event, but rather a continuous process. Document updates and employee training should be part of a feedback loop, where updates trigger new training requirements so that employees are always working from the most up-to-date procedures.
- Internal audits and inspections: Manufacturers must implement internal verification programs to ensure compliance with GMP. Internal audits and inspections are necessary for maintaining tight control over every aspect of the manufacturing process, potentially to cover hundreds of requirements (or more).
GMP Inspections: What to Expect
The FDA has the right to inspect manufacturing facilities for a number of reasons, whether for routine surveillance as part of a risk-based site selection model or for cause. FDA also conducts pre-approval inspections (PAI) for new drugs prior to market authorization.
So what can manufacturers expect during a GMP inspection?
- Plant walkthrough: FDA inspectors will want to do a walkthrough of your facility to evaluate compliance with GMP requirements. Here they will look at elements such as whether equipment is clean, and any obvious maintenance issues such as leaky pipes and signs of pests (or places where pests can enter).
- Documentation review: In any inspection, regulators will ask to review your documentation. This includes SOPs, manufacturing records and equipment maintenance logs, as well as sampling and testing procedures and results.
- Process observation: During the inspection, the FDA will take time to observe your processes on the plant floor, comparing them against your documented procedures.
- Training records: While you may not be required to produce training records for all employees, spot checks are common. They may also want to speak with employees at random to ensure they are knowledgeable and capable of doing their jobs effectively.
- Corrective action records: Inspectors are likely to want to review your corrective and preventive action (CAPA) records to see how you manage deviations, non-conformances and customer complaints. Here they will be looking at CAPA effectiveness and whether your root cause analysis processes are sufficient to ensure quality.
For more information on what to expect, manufacturers should review the FDA’s Investigations Operations Manual (IOM), the agency’s primary reference when conducting inspections.
Common GMP Violations
Analysis of GMP violations from 2018 to 2022 by The FDA Group reveals some interesting trends in GMP compliance in pharmaceutical and medical device companies. According to that analysis, the most common citations over that period were, in descending order:
- Not having or following written procedures
- Not adequately investigating discrepancies or failures, or documenting those investigations
- Not having scientifically sound laboratory controls
- Cleaning, sanitation and maintenance violations
- Computer control of master formula records
- Control procedures to monitor and validate performance
The Role of Internal GMP Audits
Internal audits and inspections are an integral part of GMP compliance and avoiding violations, especially around following written procedures. Internal GMP audits should focus on verifying that all procedures are documented, and that your team follows those documented procedures.
Incorporating GMP requirements into manufacturing inspection checklists can also help verify compliance on a day-to-day basis with requirements around:
- Process adherence
- Facility cleanliness and maintenance
- Employee training effectiveness
- Incoming material inspection
- Labeling and packaging
- Warehousing and distribution
With a digital audit and inspection platform like EASE, manufacturers can simplify internal GMP checks with mobile checklists and dynamic checklists for monitoring GMP compliance. It also makes it easy to periodically verify corrections are in place, such as after-process changes, and prevent repeat findings by checking past problem areas with violations.
GMP guidelines cover a multitude of requirements, and keeping up with them all can be error-prone and complex when trying to manage compliance with manual processes.
Digital audits and inspections can help reduce this complexity, providing ongoing monitoring of process adherence while also demonstrating a proactive approach to compliance to FDA inspectors. Incorporating GMP questions into regular checks ensures documented processes are followed and corrective actions are implemented correctly, minimizing GMP violations, helping avoid recalls, and protecting consumer health.