What Is a Smart Factory?
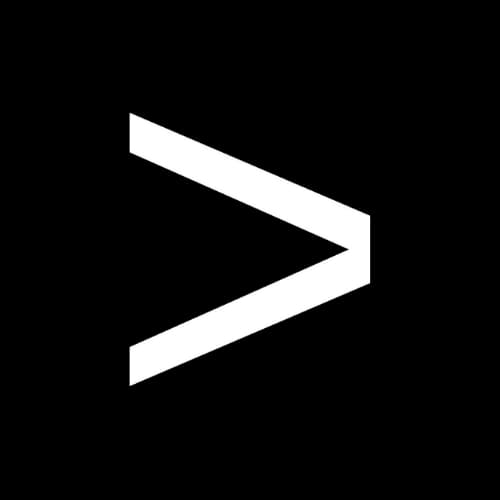
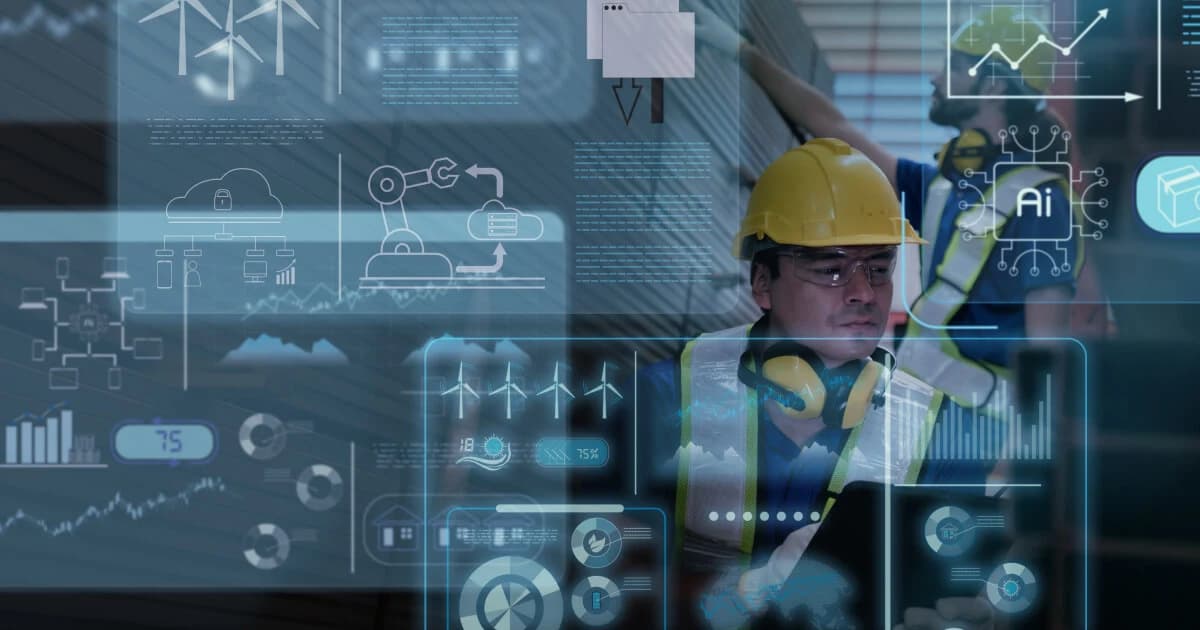
According to McKinsey and the World Economic Forum, the value creation potential for manufacturers implementing smart factory technologies will reach USD 37 trillion by 2025. This figure underscores how Industry 4.0 is reshaping manufacturing, as companies see benefits from digital transformation that include less downtime and improved productivity and efficiency.
When people hear “smart factory,” they often envision a facility dominated by robots with minimal human presence. However, the reality is very different.
Rather than replacing humans, smart factories are about integrating people, machines, and data to create a manufacturing environment that’s more efficient and productive, with higher-quality outputs.
This article explores the basics of smart factories, including:
- What is a smart factory and how it works
- Examples of smart factory technology and their impact on quality
- Benefits of creating a smart factory
Download your free Root Cause Analysis 101 Guidebook for tips on using the most common root cause analysis tools
What Is a Smart Factory?
The smart factory refers to the combination of different Industry 4.0 technologies into a manufacturing system that is automated, flexible and self-optimizing to drive efficiency and productivity gains. The smart factory encompasses a wide range of technologies used in manufacturing today, including:
- Cloud software
- Industrial internet of things (IIoT)
- Connected worker technology
- AI
- Additive manufacturing
How Does a Smart Factory Operate?
A smart factory operates as an integrated ecosystem, combining machines, people, and data to continuously improve the entire manufacturing process. Unlike traditional factories utilizing manual or even disparate digital processes, smart factories pull together multiple streams of data to optimize operations in real-time.
SAP breaks the structure of a smart factory down into three separate levels:
- Data Acquisition Level: This foundational level gathers data from various sources such as IIoT sensors, quality control checkpoints, supply chain systems, and customer feedback. These diverse data streams provide a comprehensive view of the entire manufacturing process.
- Data Analysis and Processing Level: At this level, technologies like cloud software, advanced analytics, and artificial intelligence process the collected data to improve manufacturing operations. This level transforms raw data into actionable intelligence, enabling informed decision-making across the organization.
- Intelligent Automation and Execution Level: Insights from data analysis optimize and automate factory operations. This could include adjusting production schedules and the flow of materials, fine-tuning robotic processes, providing prescriptive maintenance guidance, and optimizing supply chain operations.
When these levels are integrated, a closed loop is created where a constant stream of actionable data drives continuous improvement in smart manufacturing practices. For quality leaders, a smart factory offers greater visibility into the manufacturing process to enable proactive response to potential (or probable) issues.
Examples of Smart Factory Technology
Smart factories utilize a variety of cutting-edge technologies to optimize the production process. Below, we discuss some examples of smart factory technology and how plants are using it to streamline operations, accelerate product development and achieve higher levels of quality and efficiency.
Cloud Computing
Cloud computing enables remote data storage, processing, and access to facilitate real-time collaboration and decision-making. For example, a factory can use cloud-based audit software to monitor process compliance across multiple production lines, allowing leaders to spot nonconformances and trends to prevent defects and complaints.
Industrial IIoT
Internet of things (IoT) or industrial internet of things (IIoT) refers to a network of interconnected devices and sensors that collect and share large amounts of data. One example would be sensors on manufacturing equipment that transmit real-time performance data to enable predictive maintenance and advance warning of impending problems.
Big Data
Big data refers to extensive and complex datasets that provide insight into large-scale patterns and trends. For instance, your factory might analyze years of production or IIoT sensor data to identify optimal operating conditions and leading indicators of quality.
AI and Machine Learning
AI and machine learning technology apply algorithms and statistical models to large datasets to learn from that data and make inferences and decisions based on it. One example would be combining AI with machine vision systems that analyze images of products during inspection and detect defects that might otherwise be missed during a traditional inspection.
3D Printing
3D printing or additive manufacturing is a process for creating three-dimensional objects from digital files. 3D printing allows for faster prototyping of new product designs or custom-made parts on demand, reducing inventory and accelerating innovation.
Digital Twins
A digital twin is a virtual representation of a physical objects or process, which teams can then use for simulation and optimization purposes. For example, you might create a digital twin of a production line to test different configurations and optimize performance without disrupting operations.
AR/VR
Augmented reality (AR) and virtual reality (VR) are technologies that enhance or simulate physical environments. For instance, maintenance technicians may use AR glasses to access real-time instructions and troubleshooting advice for complex assembly processes, improving accuracy and efficiency.
Edge Computing
Edge computing refers to processing data close to the point of collection on the factory floor, which accelerates analysis and saves network resources. An example here would be control sensors on a production line that process image data locally to make instant determinations on product defects without having to send data to a central server.
Advanced Robotics (Cobots)
Advanced robotics technology, such as cobots, are robots designed to collaborate safely with humans to handle complex tasks and improve efficiency. A cobot can assist a human worker in a precise assembly process, automatically adjusting its movements based on real-time quality data and the worker’s actions.
Blockchain for Traceability
Blockchain is a decentralized, tamper-proof digital ledger technology that records transactions and can be used to track products throughout the entire supply chain. Manufacturers can use blockchain, for example, in the context of supply chain management to track every step of a product’s journey from raw materials to finished goods.
Smart Factory Benefits and Results
Companies that adopt smart factory technology can achieve significant benefits across a range of manufacturing metrics, including those driven by the fourth industrial revolution:
- Productivity and Efficiency: One big benefit of smart factories is that they reduce costly downtime, also improving efficiency through optimized resource allocation. Accenture found that predictive maintenance can reduce equipment failures by up to 70%, while AI-driven scheduling can increase asset utilization by 20-30%.
- Quality Improvement: Advanced analytics combined with real-time monitoring allows teams to shorten the time between issue identification and resolution. Some companies, for example, have reduced defects by 50% or more, according to the World Economic Forum, boosting customer satisfaction while reducing complaints and recalls.
- Cost Reduction: Despite the initial investment, smart factories can yield substantial long-term savings, reductions in downtime and defects combined with more efficient, streamlined processes contribute to as much as 30% increased throughput and productivity, according to McKinsey.
- Sustainability: Smart factories can help manufacturers reduce both energy use and waste. The International Energy Agency (IEA), for example, reports that AI-powered energy management can provide savings equivalent to over 10% of annual on-site energy costs. Improved accuracy and predictive maintenance contribute to a smaller carbon footprint.
Connected Worker and the Smart Factory
As manufacturing processes become increasingly digitized, it’s often people who are left behind, with lag time between when data is collected and when it’s made available to those who need it most. One emerging smart factory strategy that centers on battling this problem is the connected worker.
Connected worker isn’t just another tool, or even a collection of tools, however. Rather, it’s a larger strategy aimed at bridging the growing digital divide between people, information, systems and machines. The goal is simple yet powerful—provide the right people with the right information at the right time, enabling them to make the best decisions.
Examples include giving operators access to on-the-job training checklists and troubleshooting guides, automatically notifying management of plant floor audit nonconformances or using IoT data to provide real-time guidance during production.
At a high level, connected worker strategies require a step-wise foundation that includes:
- Digitizing work processes
- Connecting workers to people, information, and systems
- Enabling real-time information flow and response
By implementing a connected worker strategy, manufacturers can:
- Accelerate response times to limit the impact of plant floor issues
- Improve visibility into and standardization of processes
- Fill knowledge gaps that are growing due to ongoing retirements and loss of institutional knowledge
As Industry 4.0 practices continue to redefine what’s possible in manufacturing, smart factories will be instrumental in creating an environment where data, machines and, most importantly, people work together seamlessly to drive continuous improvement and innovation.
Rather than a one-time project, creating a smart factory is a process that takes time as manufacturers choose the tools and strategies that are best aligned with their goals and the problems they need to solve. And while smart factory technology will undoubtedly continue to generate vast amounts of data, connecting frontline workers and business leaders with that data is vital to success.
The end result is a plant that’s not just connected and intelligent, but also human-centric in that people have the insights needed to make the best decisions, no matter what arises.