The Hidden Factory: Find and Fix Hidden Inefficiencies With Lean Six Sigma Techniques
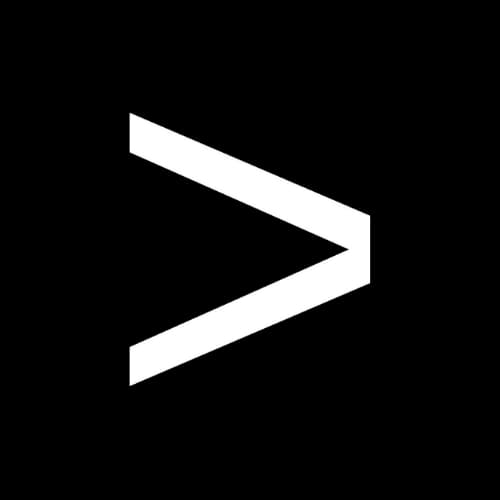
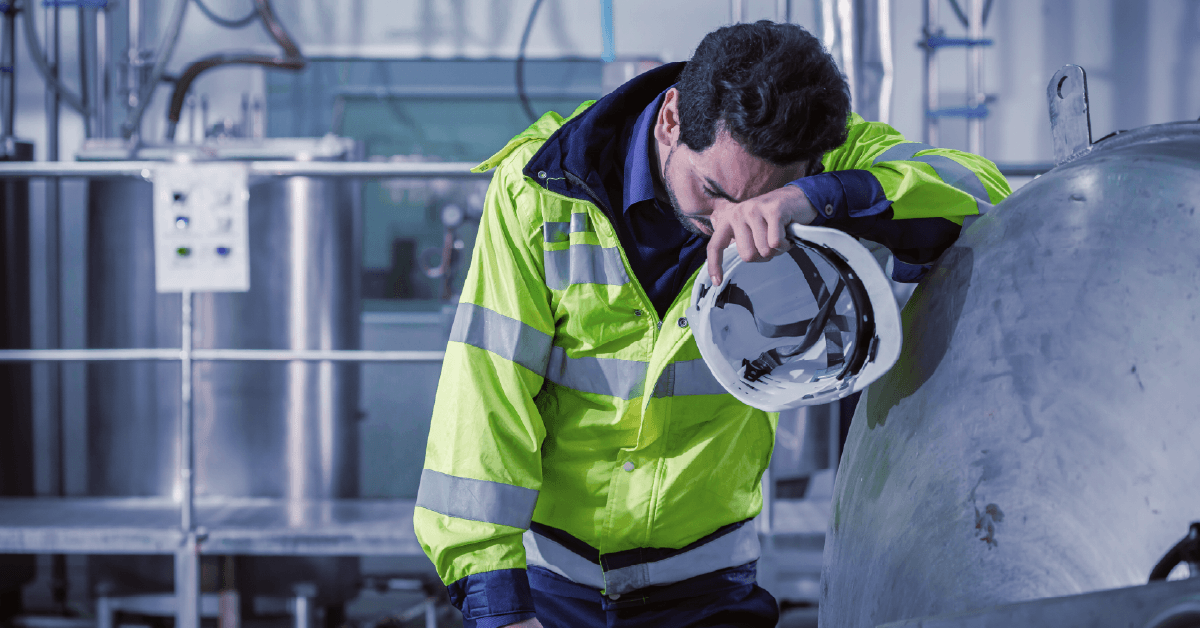
However, in every plant lurks a shadow factory, where people are actually following hidden processes rather than the ones that have been so carefully developed and documented.
In many cases, it’s not deliberate. Work instructions may be out of date, or perhaps operators are using a workaround to address another underlying problem.
At issue is the fact that these undocumented processes often actively undermine quality, safety, and efficiency.
In this context, this article examines:
- The concept of the hidden factory and how it manifests in manufacturing plants
- How it affects your business
- How to find and fix hidden inefficiencies using Six Sigma techniques
Download a free eBook on Сost of Quality: The Hidden Truth About Your Ultimate Quality Metric
What Is the Hidden Factory?
The hidden factory refers to undocumented or non-conforming procedures in manufacturing plants that introduce variation into the manufacturing process. According to late quality expert Armand Feigenbaum, this variation can account for up to 40% of total plant capacity.
Hidden factory processes include situations such as:
- Operators reworking parts at their station
- Speeding up cycle time when production falls behind
- Failure to perform preventive or autonomous maintenance
The Hidden Factory: A Real-World Example
To picture how the hidden factory works, let’s look at a real-life example from an injection molding process. In this specific process, the part produced was a coolant overflow bottle. If the injection system didn’t work properly, the bottle wouldn’t eject correctly, bending the mating surfaces of the bottle used for mounting to the assembly.
Here’s where the hidden factory issue came into play:
The bent tabs would cause the bottle to not mount correctly, but operators didn’t know it was because of a problem with the ejection system. They would just bend the tabs back with their thumbs to ensure the parts weren’t rejected.
While this was done with good intentions, problems could arise when a different operator was on the shift. Moreover, this undocumented process was hiding an unaddressed problem with the ejection system—one that could spell high quality costs for the company.
Why Is Identifying the Hidden Factory Important?
The impact of the hidden factory can hit manufacturing units hard, often affecting overall equipment effectiveness through:
- Availability loss: Unexpected shutdowns can result due to problems like parts shortages, equipment maintenance or line stoppages when workers fall behind.
- Performance loss: The manufacturing line can slow down due to inexperienced operators, or if a machine has degraded over time and no longer meets its original cycle time.
- Reduced yield: Increased equipment downtime and slow cycle times mean fewer parts are manufactured. Quality loss due to hidden factory processes also increases scrap, reducing productivity and revenue.
There are also hidden effects on safety to consider. Sometimes, operators will use a workaround for safety procedures, such as if PPE is uncomfortable or safety equipment isn’t working right. These unseen problems can lead to serious incidents that hurt workers and the company.
How to Identify Hidden Factory Processes
Identifying your plant’s hidden factory processes is the first step to bringing them into compliance with established standards. Lean Six Sigma methodologies, such as DMAIC (Define, Measure, Analyze, Improve, Control), play a key role in this effort. Observation and analyzing metrics are essential in uncovering hidden issues and implementing process improvements.
For example, connected worker platforms that allow employees to log observations can be a powerful method for engaging frontline workers in reporting problems they see and contributing to quality control.
Layered process audits are also an increasingly prevalent tool for uncovering hidden factory processes in manufacturing, providing daily real-time opportunities to:
- Observe processes at the Gemba, or where the work is actually done
- Verify process inputs (e.g., the 6Ms) comply with standards
- Get feedback on why operators aren’t following standards
Comparing performance metrics can also point to places where the hidden factory may be at work in your plant. For example, marked differences in cycle time between shifts often indicate where individuals are executing processes differently. This can significantly impact throughput, as inefficiencies and variations reduce the overall production rate. From there, you might observe the work area, looking for the root cause of bottlenecks or variations in process inputs or reducing waste on the factory floor.
How to Fix the Hidden Factory
Fixing the hidden factory to improve operational efficiency is no small task and requires a multi-faceted approach. Below, we discuss several strategies to attack the problem, which are:
- Look for small inefficiencies in a process
- Engage your employees in quality
- Encourage open communication
- Focus on risk
- Streamline the system
Manufacturers can apply a variety of tools to the above strategies, such as Kaizen events focused on a specific problem or Gemba walks where management observes what’s happening on the plant floor. Layered process audits are another popular strategy, particularly in the automotive industry, as are connected worker platforms that help increase visibility into issues.
Look at the Smaller Inefficiencies
Addressing smaller inefficiencies can lead to significant improvements in overall process efficiency. These issues might not seem significant, but they can create a feedback loop of inefficient practices to compensate for them, adding to the operational costs.
One manufacturer had a single work cell creating a bottleneck on an assembly that was ultimately causing performance loss. Observation revealed that operators were first picking up two screws to hand start them, then reaching behind for a screwdriver to drive them to final torque. The connected worker screen was also behind the operator, forcing them to turn around to view the sequence of steps, torque achieved and module test results.
Of course, nothing in the work instructions mentioned all these twists and turns, which only served to slow the process down. Solving the problem required just a few relatively simple hacks, shortening the process from 14 to 10 seconds:
- Hanging the screwdriver on a traction system in front of the operator
- Installing a small stand for screws right next to the operator
- Mounting the connected worker screen in front of the operator
Engage Your Employees
Frontline workers see process inefficiencies and non-conformances firsthand. That is why engaging them is critical to identify and eliminate the hidden costs associated with operational inefficiencies in the production process.
Connected worker platforms, for instance, provide tools such as:
- Digital work instructions to ensure operators follow the right sequence of steps
- A way for operators to record plant floor observations such as machine or safety issues
- The ability to send instant messages to team members when problems arise
Mobile auditing tools, too, can help ensure process standardization and identify variations in high-value inputs such as operator behavior and machine settings. They also generate conversations about processes and quality, even uncovering insights from operators that can make processes more efficient.
Remember that follow-through is essential to engaging employees. People won’t speak up if they see management is slow to fix problems, which also undermines credibility and buy-in for continuous improvement efforts. Making investments in quality may seem like a cost sink until you understand the cost of doing nothing.
Encourage Open Communication
Fostering a culture of openness and communication is necessary to expose processes that don’t conform to standards. One problem in many plants is that when problems arise, blaming and finger-pointing are the first responses.
Instead, leadership needs to recognize and communicate to the team that finding problems internally is the goal because that’s what helps prevent them from reaching customers.
For example, Gemba walks and other plant floor checks can help normalize having open conversations about quality and safety. They also give frontline workers the chance to share their observations, concerns and ideas for improvement.
Focus on Risk
Any number of hidden processes may exist in a plant, but which ones need to be fixed first? More than just inefficiency, companies should also focus on risk.
In the context of the hidden factory, you want to look at where process variation has caused increases in KPIs like scrap or customer complaints. Pareto charts of process failures can provide important insight into your biggest risks, as well as layered process audit questions focusing on high-value process inputs.
As you look to standardize processes, consider also whether you’re providing operators with information about the highest-risk process elements. Digital procedure checklists, for instance, can be customized to the certification level of the operator. While a new operator may need to check off ten steps, a more experienced operator may only need three. Those three steps should be the ones most critical to quality or where known issues have occurred in the past.
Streamline the System
Streamlining the system is a way to proactively prevent hidden factory processes that harm efficiency, quality, and safety.
Consider the earlier example where operators initially needed to do a lot of bending and twisting to complete a process. Keeping people facing forward in what’s called the golden zone, as well as making the screws easier to grab, didn’t just increase efficiency. It also meant fewer defects.
That’s because of one simple fact:
Before rearranging the work station, the process required a greater number of steps. Fewer steps equal fewer opportunities for problems, such as dropping screws into the assembly.
Making Your Operations Efficient
Quality leaders must prioritize developing efficient processes and, just as importantly, ensuring people adhere to those best practices. Applying these strategies is a long-term effort that requires collaboration among multiple groups, an area where technology is helping companies make huge strides.
However, it’s important to remember that establishing standard operating procedures (SOPs) is a vital preliminary step, with everything else coming after. If your work instructions are insufficient, for example, it’s impossible to expect people to audit against that standard. Similarly, technology can’t fix insufficient standards, which are the foundation of quality.
Once SOPs are in place, plants can use tools like connected worker platforms and mobile auditing to improve efficiency, standardization and visibility.