What Van Halen Can Teach Us About Safety Questions and LPAs
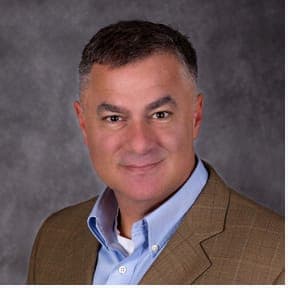
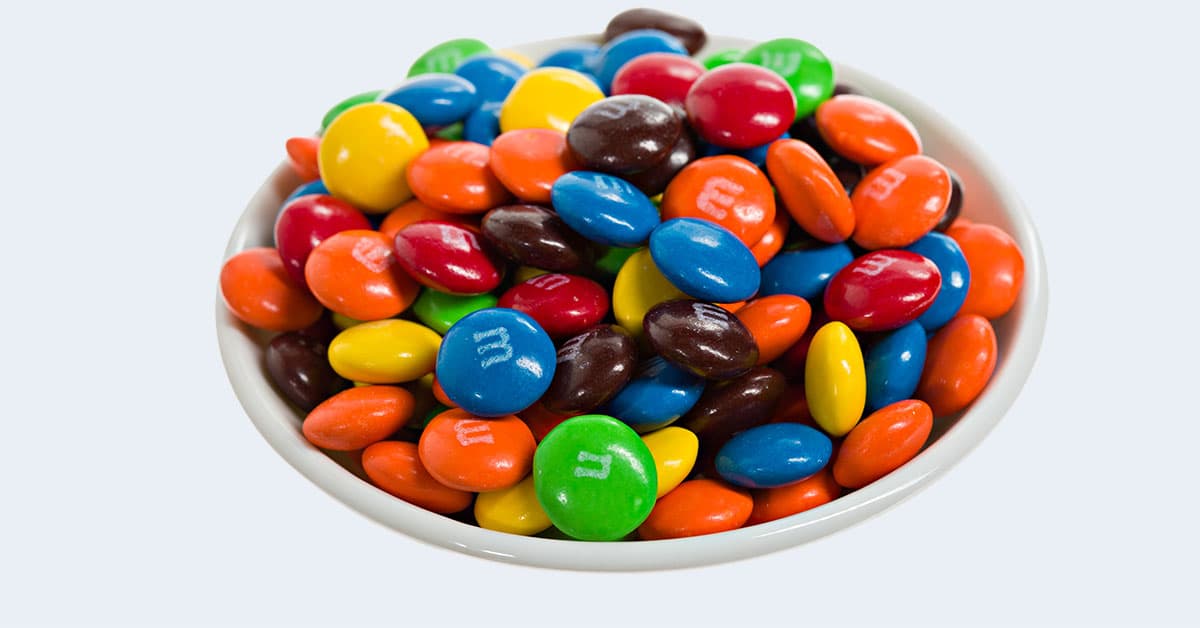
When it comes to what layered process audits (LPAs) should cover, manufacturers typically fall into one of two camps.
On the one hand, some companies prefer to focus exclusively on critical-to-quality characteristics in these short, frequent audits.
Other manufacturers incorporate safety questions into LPAs, helping keep tabs on known risks every single shift—the very element that makes LPAs so powerful in improving quality.
In today’s post, we look at 3 important reasons to include safety audits in your LPAs, and how the results can also shed important light on the state of quality in your plant.
Get LPA tips, strategies and best in this free Ultimate Guide to Layered Process Audits eBook
1. Safety Questions Are a Leading Indicator
Van Halen was famous for having contracts require a bowl of M&M candies with all the brown ones removed waiting backstage for them. While it sounds like a classic case of a rock band being purposefully difficult, that actually wasn’t the case.
The real reason their manager included this oddly specific request?
He knew that if he arrived at a venue and there were no brown M&Ms in the bowl, he was confident the venue would have the rest of the details right. If the bowl had brown candies (or if there were no M&Ms at all), the manager knew he had to check every other detail to avoid problems.
Safety questions play a similar role. Maybe you ask whether the operator is wearing safety glasses, or whether they’re wearing steel-toed shoes. These questions may seem basic, but in reality they are leading indicators of whether operators know the requirements of their job.
If the operator is wearing their safety glasses, that’s an indication that they know the most elemental safety requirements of the task. If they aren’t, you’ll want to look closer at everything else they are doing.
2. Safety Is Key to Preparation
Preparing to work safely is part of doing high quality work. For instance, if you’re baking a batch of cookies and neglect to have oven mitts nearby, what’s going to happen when the timer goes off? You’re either going to drop the pan and wreck the cookies, or potentially burn them while you’re looking for oven mitts.
One way to work in questions that address the fact that safety and quality go hand in hand is by using safety questions related to 5S on whether the work cell is set up correctly.
As an example, instead of asking if there are any trip hazards in the work cell, you might ask whether the work is set up to the diagram. This question covers multiple potential safety risks. For instance, it would identify if an operator creates a trip hazard by draping an air hose on the opposite side because he wants the machine on his left instead of right.
3. Layered Process Audits Identify Safety Risks Faster
One of the most important aspects of layered process audits (LPAs) is that they are short but frequent, taking place on every shift, every day. However, many organizations don’t do safety audits or inspections this frequently.
If you include safety questions in LPAs, you’re likely to find safety issues faster and prevent incidents simply due to the sheer number of checks you’re doing on a daily basis.
If you’re using software like EASE, for example, you can rotate in 10 safety questions in a 24-hour period over three shifts. Compare that to only doing one safety audit per week, and it’s easy to see how LPAs create added opportunities to identify and mitigate safety problems.
While some plants keep their LPAs focused on quality inputs, the truth is there is a strong argument for incorporating a few safety questions within each audit. Not only can you check for basic understanding and preparation, you also get more chances to identify unsafe behaviors before they cause accidents. In doing so, workers are protected as well as the customer, allowing you to verify that everyone is doing safe work that ensures quality.