Valeo Wipers Plant Reduces Quality Costs 50%
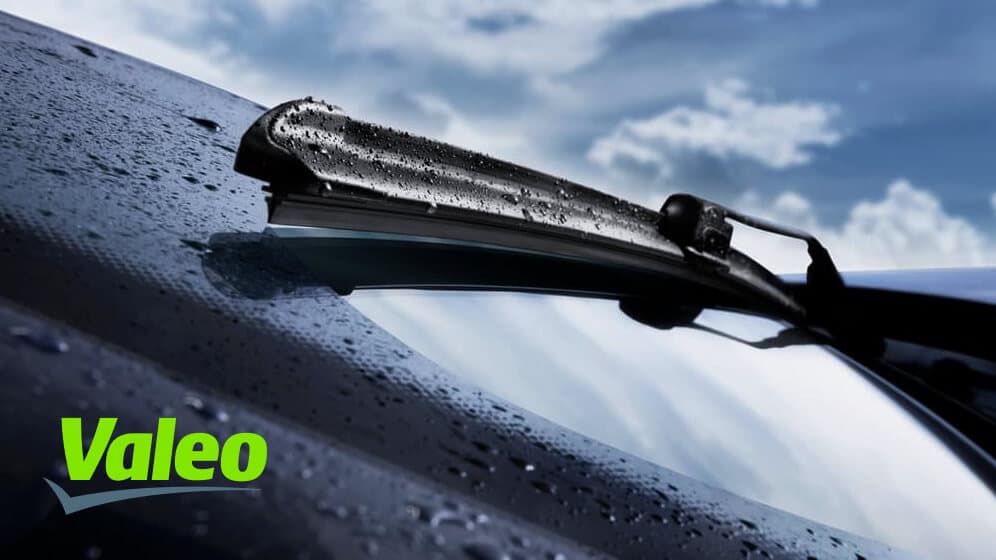
Overview
A leading automotive supplier deployed EASE to improve the efficiency of layered process audits after a competing software solution failed to deliver results.
The EASE platform helped Valeo improve control over their processes and systems, in particular helping quickly contain two quality issues to cut complaints and quality costs in half.
Background
Valeo is a Fortune 500 automotive supplier with over 100,000 employees in 31 countries worldwide. Headquartered in Paris, the company operates 184 production facilities and 64 R&D centers globally, bringing in over $18B in annual revenue.
The company conducts layered process audits (LPAs) to meet customer requirements and ensure quality processes are followed on the plant floor. Finding nonconformances that could lead to complaints is also a high priority as the company continually strives to improve customer satisfaction.
Addressing Customer Concerns
One of Valeo’s wiper facilities located in Mexico was facing a complaint from a leading OEM over defective pivot tubes.
“We needed to address the issue of broken pivot tubes causing leakage and breakdown in the field,” says Itze Porras, Quality Assurance Engineer. She says the problem was having an impact on customer satisfaction, a top concern in this customer-centric company.
To prevent the defect from occurring, Quality Engineer Jose Ochoa and his team added a step to the linkage assembly process to ensure the correct crimping in the field housing. “We added a small cut on the pivot from the linkage to verify that the tube wouldn’t break down,” says Ochoa.
More than just updating the work instructions, however, Ochoa and his team had to make sure the new process was being followed by operators on the manufacturing floor.
Like many automotive suppliers, the company was using LPAs to check high-risk process inputs such as those related to customer complaints. Initially, the facility used a basic audit software program to manage plant floor audits. Unfortunately, the platform didn’t perform as well as the team had hoped.
First, the software’s reminders didn’t allow enough time to complete the audit and any necessary followup. Sharing results with management was also problematic, as was identifying trends, calculating statistical data and determining whether audits were closed. Finally, the software had limited options for displaying data graphically, making it hard to see where their biggest quality risks existed.
Because of these difficulties, the plant stopped using their original audit software and decided to manage LPAs using Excel spreadsheets. This required someone to manually input and analyze LPA checklist data, making the process more time- and resource intensive while reducing visibility into quality risks.
“It was very tough to handle the data in Excel,” Porras says.
Making Layered Process Audits More Effective
To improve control and visibility into manufacturing processes, Valeo decided to pilot the EASE platform on a free trial in the plant.
“We needed something that was user-friendly, and that would allow us to review results and findings in a short 20-minute meeting,” says Porras.
Using EASE, Valeo is able to:
- Create an annual audit schedule in minutes
- Automatically remind team members of audits and send links to mobile checklists
- Upload audit photos as evidence or to make LPA questions clearer
- Visualize results instantly with Pareto charts showing failures by work area
- Track mitigation action items, due dates and open issues
They set up the system so that roughly 80 people in quality and production each complete six audits every month, totaling up to nearly 500 audits monthly.
Within the audit checklist, they included a photo of the tube with the right crimping so that auditors could easily verify whether operators were following the new process.
“This allows us to show what the correct condition looks like,” says Ochoa, adding, “this improvement helps us ensure the correct crimping for other customers as well.”
They also added an LPA question to verify that safety meetings take place daily and minutes are shared between shifts, an area which previously led to third-party audit observations. Prior to using EASE, minutes from the team’s daily safety meeting weren’t recorded or posted consistently, creating missed opportunities to share alerts, lessons and improvements across the plant.
“With this item now on the audit checklist, we can track the daily meeting and make sure safety issues are being communicated from one shift to the next,” says Porras.
Cutting Quality Costs in Half
Resolving the tube crimping issue with EASE has reduced customer complaints and quality costs by 50%, also delivering a substantial increase in customer satisfaction.
“We haven’t had a recurrence of the defect with the OEM, and we haven’t had any complaints from other customers either,” says Ochoa.
Team members report that the platform is easy to use, efficient and clear in terms of questions and follow-up actions—all primary objectives of the implementation. Valeo has also received positive feedback on third-party audits, minimizing findings now that LPAs verify that minutes from daily safety meetings are recorded and shared with the team.
Compared with the previous LPA software used, the system has improved control over audit reporting and follow-up, providing statistics and graphs to quickly identify quality risks.
“It’s helped us improve our communication and how we handle the results of our audits, including sharing photos and other evidence,” says Porras.
The platform makes it easy to see how many issues are open, how many are closed and where people aren’t completing their scheduled audits. Audits can be completed much faster, taking roughly half the time of previous methods. Their LPA program as a whole is more effective, and today roughly 98% of audits are completed on time.
Ultimately, the EASE platform has helped the team improve overall visibility into their manufacturing processes, showing exactly where operators are — and are not — following work instructions.
“This is very encouraging to us as we pursue our goal of zero customer complaints,” says Porras.