How Digital Transformation is Driving Continuous Improvement in Manufacturing
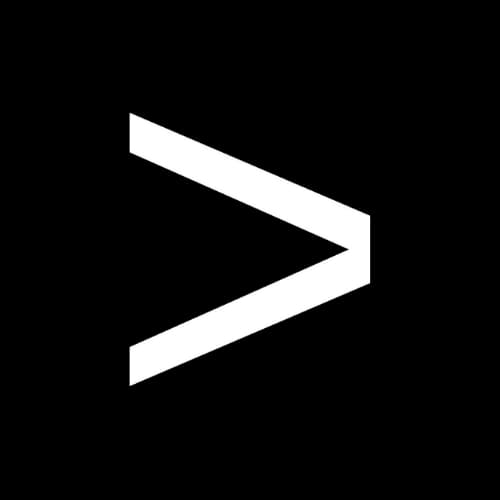

According to research from Gartner, 80% of manufacturers are ramping up digital transformation efforts in response to economic challenges such as inflation and worker shortages.
The growing number of companies increasing investment in digital transformation shows that Industry 4.0 delivers real value in continuous improvement. Organizations that integrate digital technologies into their operations are part of a sea change revolutionizing manufacturing, helping companies streamline their processes, improve quality, and boost productivity.
Here we explore real-life examples of how digital transformation drives continuous improvement in the manufacturing industry and giving forward-thinking companies a competitive edge.
Download your free Ultimate Guide to Layered Process Audits for more LPA question best practices, examples and tips
4 Ways Digital Transformation Is Driving Continuous Improvement in Manufacturing
Machine Learning
Machine learning or artificial intelligence (AI) is a fast-growing segment of today’s digital transformation wave. Manufacturers in particular are focusing on AI for a wide variety of use cases, such as:
- Supply chain optimization
- Predictive maintenance
- Transportation and logistics
- Process improvement
- Quality control
Wayfair, for instance, was an early adopter of AI, applying the technology to logistics and shipping. The ability of the company to continuously adjust which products they sent to different ports helped reduce inbound logistics costs by a staggering 7.5% amid pandemic-driven demand fluctuations.
Cloud Computing
According to Gartner, cloud computing remains one of the top drivers of Industry 4.0 investments, expected to reach $597 billion in 2023. The ability to store data in the cloud, rather than manage costly on-premise software systems, now means manufacturers can deploy various applications while maintaining a comparatively small IT footprint.
Applications range from enterprise platforms like manufacturing operations management (MOM) and enterprise resource planning (ERP) software to industry-specific point solutions like layered process audit (LPA) software.
In the case of LPA software, cloud technology enables greater visibility into manufacturing processes by making audit data available in real-time. People can complete checks on mobile devices and immediately upload findings to the cloud, which are then distilled into actionable insights for leaders.
As an example, one global tire manufacturer uses LPA nonconformance findings to trigger a fast look across all related machinery using custom tags in the audit question library. This quick response lets them quickly identify systemic issues with an outsized impact on quality.
Watch Our Free Webinar on LPA Improvement
IIoT and Edge Computing
Industrial Internet of Things (IIoT) sensors in plant devices have become a core digital transformation catalyst in manufacturing applications such as predictive maintenance, inventory management, and equipment optimization.
Edge computing, which refers to data processing near its source (the network edge), has also expanded manufacturer capabilities around harnessing production data to drive continuous improvement.
Automotive manufacturers use IIoT sensors on machinery to monitor and process performance data at the edge. This lets them quickly pinpoint maintenance issues and inefficiencies, with real-time analytics to drive plant floor decision-making.
For instance, smart factory technology lets automotive manufacturers use IIoT sensors to detect abnormal machine vibrations and repair equipment before it breaks down, reducing unplanned downtime. IIoT sensors combined with edge computing also allow them to collect and analyze production line data for identifying bottlenecks and process improvement opportunities.
Connected Frontline Worker Technology
LNS Research reports that manufacturers are achieving big successes with connected frontline worker technology, with four in five transformation leaders achieving meaningful corporate value from implementation.
Connected worker technology encompasses a suite of tools used for improving quality and efficiency, including:
- Digital procedure checklists, remote engineering support and troubleshooting guides to give operators on-the-spot access to vital information
- Software applications for conducting digital plant floor audits and inspections
- Bi-directional communication tools such as instant messaging to connect operators with added support and real-time answers to questions
Achieving Continuous Improvement Through Process Improvement
Digital transformation is rapidly changing the manufacturing landscape today, with even minor process improvements potentially providing significant returns. Those companies willing to take the leap are gaining a competitive advantage over those who adopt a wait-and-see approach. However, it’s critical to avoid “shiny object syndrome,” instead taking the time to identify an existing problem and then exploring how to solve it with digitization.