How to Hire a Great Quality Engineer
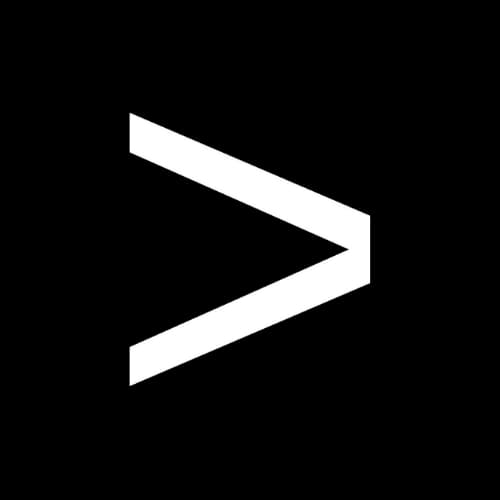
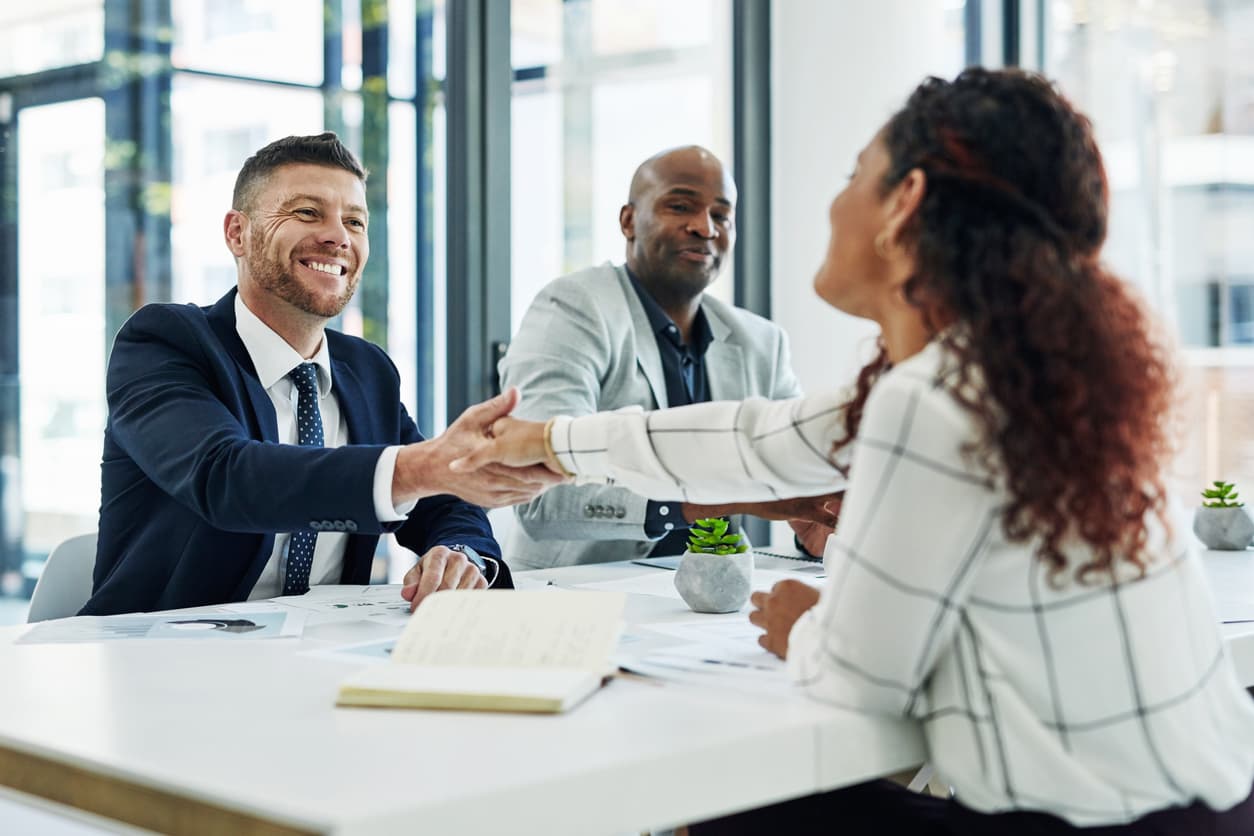
According to a Deloitte study on the manufacturing skills gap, the U.S. will need to fill 4.6 million manufacturing jobs over the next decade, but over half of those are likely to sit vacant.
It’s a grim prospect for the manufacturing industry, where the average time to fill a position rose from 94 to 118 days from 2015 to 2018. U.S. Bureau of Labor Statistics (BLS) data show that as of September 2019, a full 500,000 manufacturing jobs remain open, a problem that affects nearly every company in the industry.
Quality departments are already feeling the pain, with a quick search of Indeed showing thousands of open positions for quality engineers nationwide.
What can companies do to adapt to the skills gap? And how can they ensure they’re bringing on the right hires?
To answer these questions and learn how to hire a great quality engineer, we talked to Craig Nowotny, general manager of Arthur Wright & Associates. The staffing firm focuses exclusively on filling positions in manufacturing, engineering and operations, an area where Nowotny has nearly 30 years of experience.
Be Ready to Move Quickly
A cursory search on job site Indeed shows more than 4,000 openings for quality engineers nationwide, part of why Nowotny says companies must be ready to move quickly.
“It’s a candidate-controlled market, and there’s a real shortage of talent,” Nowotny says. He adds, “When you see someone good, you need to make an offer, because otherwise, your competitors will snap them up.”
He says the typical “cattle call” process—where you phone screen 20 applicants, bring 10 in for interviews and bring back your top three for round two interviews—is too lengthy for today’s competitive job market.
“That’s a 30- to 60-day process,” says Nowotny. “The best candidates are going to be long gone by then.”
Another common problem is having too many cooks in the kitchen slowing down the hiring process. Ultimately, Nowotny says, you can’t please everyone—which in turn means you can’t make a decision.
Keep Expectations Realistic
Nowotny says a critical challenge is that many companies have outsized expectations, which can slow down the hiring process (or set you up for disappointment). Part of the issue is that, depending on the company, the title quality engineer can cover areas such as:
- Supplier quality
- Quality process
- Quality cost management
- Warranty quality
Some positions may even comprise each one of those skillsets, but Nowotny warns companies away from making their list of required qualifications too long.
“If you have a job description where you want someone who can walk on water, you’re not going to find that person,” he says. “You have to determine what’s most important.”
What to Look for in a Candidate
The most important element to look for, according to Nowotny, is direct experience. That means they should already understand the systems your organization uses, such as IATF 16949 for automotive quality or AS9100 for aerospace quality.
“You can’t take someone from food and expect them to know automotive, just as you can’t take someone from automotive and expect them to know aerospace,” he says.
Part of the problem in hiring a great quality engineer is that engineers aren’t usually outgoing, so they’re not likely to wow you with their bubbly personality during the interview.
“Engineers are methodical thinkers,” Nowotny says. “They have to process questions and information before they speak.”
That means companies must look beyond surface impressions to avoid overlooking quality candidates who aren’t necessarily charismatic. He says companies should be sure to look at:
- Growth potential: Instead of focusing on the dream candidate, ask yourself, is this person a quick learner? Do they get along well with others? While everyone wants the A player, Nowotny recommends asking whether you can take a B player up to the A level.
- Job moves: It’s no secret that a quality professional’s job relies on the ability to solve a constant stream of problems. That means it’s critical to ask why someone is looking for a new job—and avoiding candidates that always seem to be running from problems rather than confronting them.
- Cultural fit: Your next quality engineer has to be able to adapt to your plant’s culture. “You could have a plant in northern Alabama and one in southern Alabama and they could be totally different,” says Nowotny. “It’s all about identifying what makes your site’s culture unique.”
As manufacturing enters the era of Industry 4.0, it’s also worth looking for candidates with a background or interest in using advanced technology to improve quality on the plant floor.
If there’s one thing Nowotny says quality managers should take away, it’s that companies need to accelerate the hiring process.
“If you have a position that hasn’t been filled for six months, that shows your hiring process is broken,” says Nowotny. “That’s where we come in.”
By keeping expectations realistic, and focusing on the right elements, organizations will be in a better position to hire the best quality engineer candidates. And you never know—your new hire could end up being a future leader.