How to Write Effective Layered Process Audit Questions
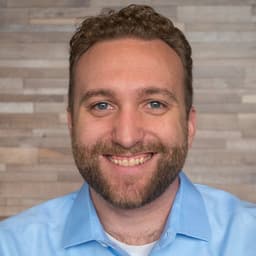
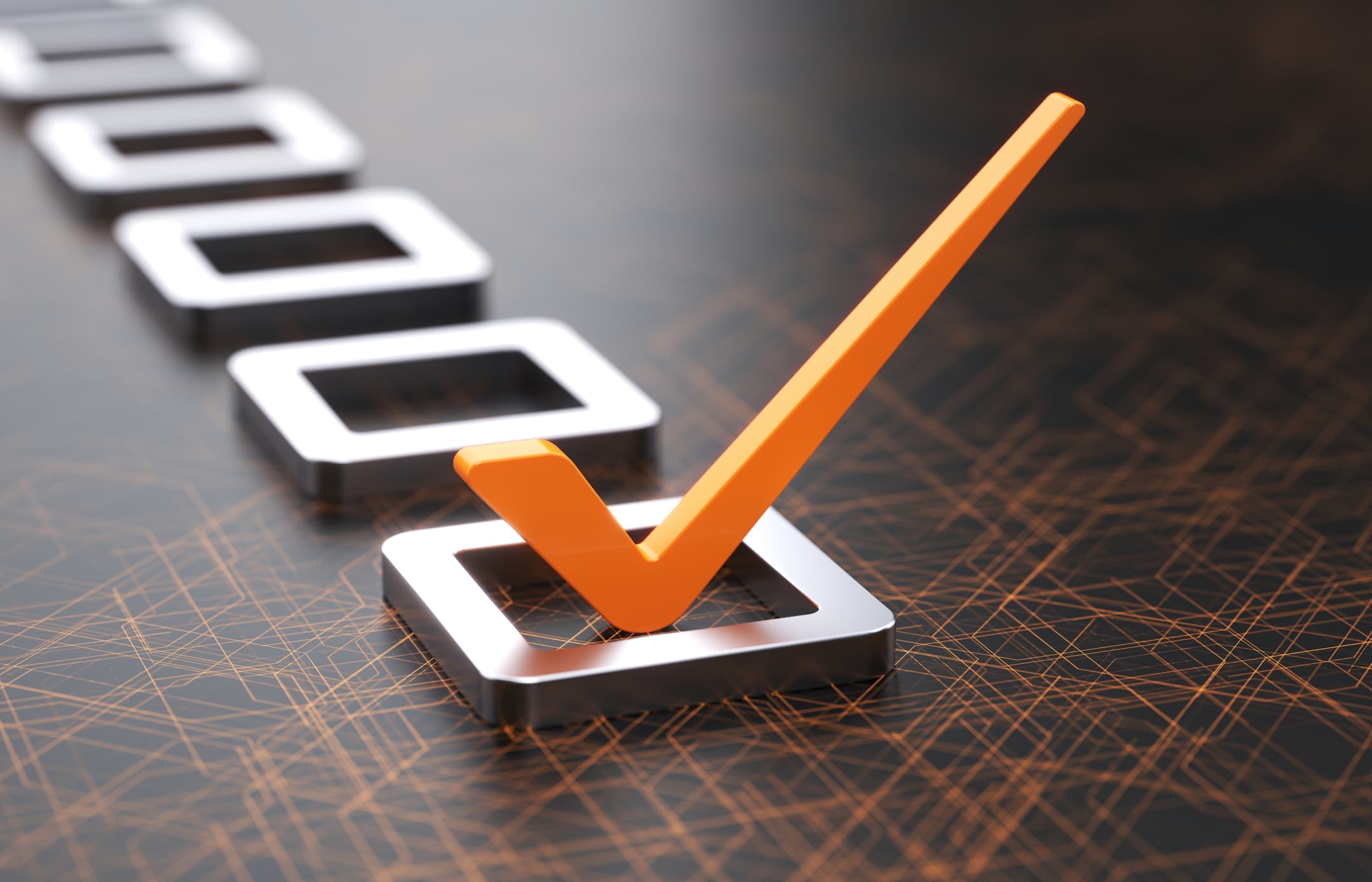
Famous businessman Robert Half once said, “Asking the right questions takes as much skill as giving the right answers.”
It’s true whether we’re talking about interviewing and hiring—Half founded one of the largest global staffing firms—or whether we’re talking about quality management. The need to ask thoughtful questions to gain valuable information is especially critical when it comes to creating layered process audit (LPA) checklists.
In an LPA program, multiple layers of management audit high-risk processes at varying intervals, conducting daily checks that systematically reduce variation. These process audits are powerful because of their high frequency, and their ability to provide a real-time snapshot of shop floor processes critical to quality.
As for whether a company can achieve the biggest benefits from LPAs? That all depends on whether you have well-written questions—and how frequently you update them.
Layered Process Audit Checklist Questions Should Add Value
LPA checklists should have about 10 to 15 yes or no questions focused on processes critical to quality, performance or customer satisfaction.
Many companies, particularly those using paper-based checklists, rely on overly generic questions that yield limited insights. They do this so they can use the same checklist for multiple work areas, when a best practices approach is to create separate checklists for each area.
LPA questions add value when they are:
- Objective: Auditors should easily be able to answer the question after comparing the evidence against the stated evaluation criteria.
- Specific: Avoid vague terms like “proper,” “correct,” “accurate” or “appropriate.” If you expect an auditor to verify an instrument has the right setting, clearly state the specifications and tolerances for that setting.
- Concise: Keep questions brief and to the point, avoiding jargon. Write questions in a way that non-experts can easily understand, since not all auditors will be familiar with the process. LPAs should take less than 15 minutes to complete, another important reason to make questions as straightforward as possible.
Examples of Layered Process Audit Checklist Questions
To help see where your LPA questions might need a little work, let’s look at some examples are from The Luminous Group. Note how the revised questions provide contextual detail so auditors understand the intent and value of each question.
Before: Are all red tags completed properly?
After: If any parts in the area have a red scrap ticket, verify the ticket contains the part number, date, quantity, defect and description. (Incomplete tagging distorts scrap reporting and hinders root cause analysis).
Before: Is the machine set up correctly?
After: Did the operator install the gear on the drive shaft with the blue-colored edge at a 45° angle to the base by using the 12-gear alignment tool? (If this specific tool is not used, the gear may be out of position and require rework after testing).
Before: Does the operator tighten the bolts in the correct order?
After: Is the operator tightening the bolts in the order specified on the work instructions? (Product failure may occur due to degradation in durability if specific order is not followed).
Before: Is the workstation clean?
After: Is all waste cleared from the workstation, with oily rags placed in oil waste bins? (A clean workspace helps prevent errors and safety incidents, and rags contaminated with oil are subject to special disposal requirements).
Creating Your Layered Process Audit Checklist
An effective LPA program extends beyond the quality team, seeking input from departments like operations, engineering and logistics. Design engineers are particularly well-equipped to identify processes critical to quality.
As you write your process audit checklist questions, keep the following considerations in mind:
- Checklists should be specific to the process, rather than using a single checklist to cover all work areas.
- Identify specific LPA questions from failure modes and effects analysis (FMEA) reports, customer complaints, scrap reports and other known problems. Questions may also cover other critical parameters like equipment reliability.
- Include questions from customer-reported issues and verification activities from corrective actions.
- While questions may ask for information like the operator’s name or part numbers, LPA questions don’t measure finished parts.
- Write yes or no questions so that a “yes” answer means passing and a “no” answer triggers follow-up.
- If you’re using an automated LPA platform, you can add photos to checklist questions to help auditors identify what “right” looks like.
- Randomize audit questions (or a portion of them) to prevent pencil-whipping and protect data integrity.
Developing good LPA checklists is an ongoing process, not a one-and-done event. If a question only has a 0.001% failure rate, that’s a wasted question that should be replaced with a newly identified problem or risk.
LPA questions are like anything else in quality management: take the “check the box” approach and you’ll get minimal results. Take the time to write thoughtful questions, and you’re more likely to see the kind of results that add millions (or more) to the bottom line.