Reduce Incidence Rate with These 8 Free OSHA Resources
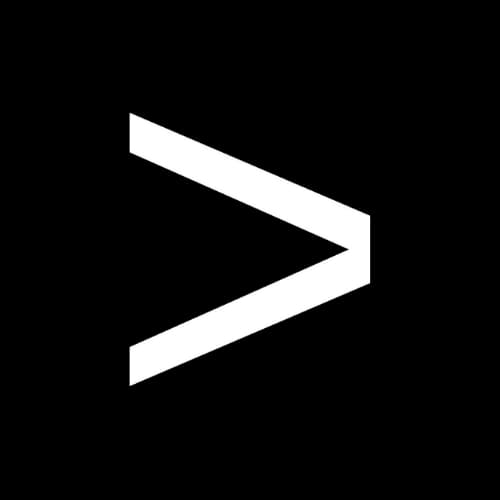
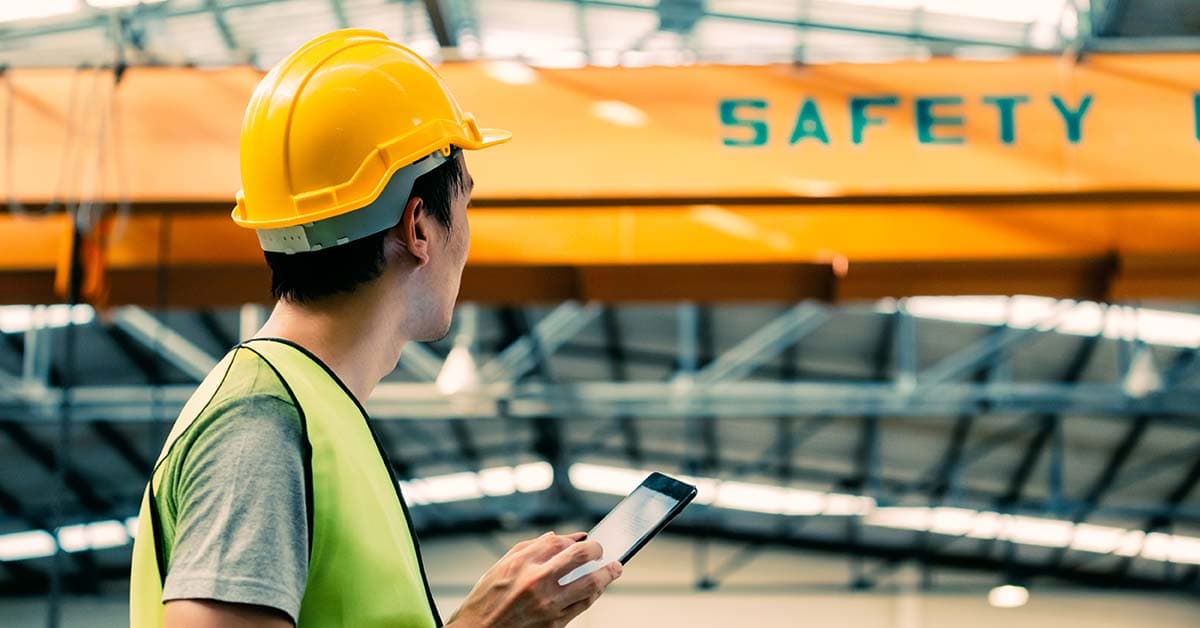
Manufacturing accounted for more than 15% of 2.8 million U.S. workplace injuries and illnesses in 2019, according to the latest data available from the Bureau of Labor Statistics (BLS). The industry’s incidence rate sits at 3.3 cases per 100 full-time employees (FTEs), higher than the national average of 2.8.
No matter what your plant’s incidence rate is, improvement should be the goal. To help you do it, today’s post looks at free OSHA resources such as training materials, publications and cooperative programs for improving safety.
1. OSHA COVID-19 Guidance
It’s worth reviewing OSHA COVID-19 guidance aimed at reducing coronavirus transmission in the workplace. As the pandemic may increase incidence rates overall, it’s one area where companies should be paying attention.
Note particularly the section on the role of employers, which details compliance requirements and best practices for reducing infections.
2. OSHA eTools
OSHA provides free web-based training for a wide variety of both general and industry-specific safety topics on its eTools page. Some eTools include virtual games that can be incorporated into training, with training resources covering topics such as:
- Hazard identification
- Lockout/tagout
- Powered industrial trucks
- Machine guarding
- Respiratory protection
- Ergonomics
On the eTools page you’ll also find what the agency calls Expert Advisors. These tools help walk you through tasks like:
- Identifying potential hazards
- Building an emergency plan
- Determining applicability of confined space and recordkeeping rules
- Selecting a respirator
3. OSHA Videos
OSHA provides videos you can use use in your own safety training programs, helping improve engagement compared with just going over printed materials. Video topics include:
- COVID-19 safety
- Ergonomics
- Respiratory protection
- Lockout/tagout
- Machine guarding
- Silica
Many eTools and videos cover common OSHA violations such as lockout/tagout, powered industrial trucks and machine guarding. As such, it’s worth paying attention to what the agency has to say about these topics.
4. OSHA Training Requirements Guide
To help companies ensure training compliance, the agency has published a PDF guide that pulls all OSHA-required training requirements together in one place.
With injuries higher among workers new on the job, training should be a particular area of focus for manufacturers. There’s no question that training is something OSHA inspectors will ask about on any visit to your facility.
5. OSHA Training Resources
OSHA provides several training resources in addition to those mentioned above, including:
- Outreach training courses in basic hazard awareness provided by OSHA-authorized trainers, leading to either OSHA’s 10-hour or 30-hour card
- A PDF guide aimed at helping employers develop effective training programs
- Links to OSHA Training Institute Education Centers certified in providing safety training
6. OSHA Cooperative Programs and Compliance Assistance
OSHA runs several cooperative programs and provides personalized compliance assistance for companies who want to get proactive about safety.
The agency offers tips for finding a cooperative program based on your individual needs. Programs include:
- Free, confidential onsite consultations for small- to medium-sized businesses that won’t result in enforcement penalties
- Safety and Health Achievement Recognition Program (SHARP) for companies that demonstrate superior performance during an onsite consultation
- Voluntary Protection Program (VPP) for companies with an incidence rate below industry average, a program that involves undergoing a rigorous OSHA evaluation
- OSHA Strategic Partnership Program (OSPP), which focuses on establishing goals and strategies for protecting worker safety in large corporations
- OSHA Challenge initiative where the agency mentors participants through the process of developing a health and safety program
- State programs for companies in one of 22 states with an OSHA-approved State Plan, which is a health and safety program run by the state rather than OSHA
Certain programs like SHARP and VPP also come with an added benefit: exemption from OSHA-programmed inspections while organizations maintain certification.
7. OSHA Resources for Small Businesses
Small businesses may have fewer dollars to invest in safety programs, which may inadvertently put workers at risk. To help address this problem, OSHA has put together some helpful resources specifically for small businesses.
These resources cover areas such as:
- Compliance guides for specific hazards like beryllium, silica and hexavalent chromium, as well as topics like confined spaces and hazard communication
- Recordkeeping and reporting guidance for completing OSHA logs and reporting safety incidents
- A Small Business Safety and Health Handbook that provides an overview of how to set up a health and safety management program, including dozens of self-inspection checklists
8. OSHA eBooks and Fact Sheets
OSHA publications cover a wide variety of health and safety topics, including fact sheets, eBooks, pamphlets and printable signs. Many are also available in Spanish.
These publications run the gamut, covering topics ranging from asbestos to welding. The eBooks provide in-depth information for industry, while fact sheets offer an easily digestible overview of topics for getting up to speed quickly on known hazards.
Reducing incidence rate isn’t easy, and it’s not something that happens overnight. Focusing on just a few of these resources can help plants make progress, whether through improved training, awareness or individualized support.