SOPs in Manufacturing: How and Why to Create Them
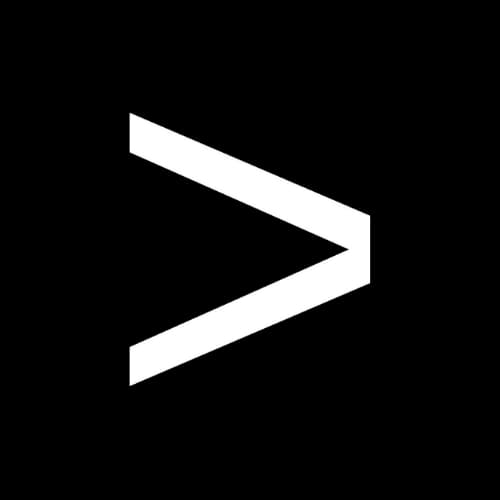
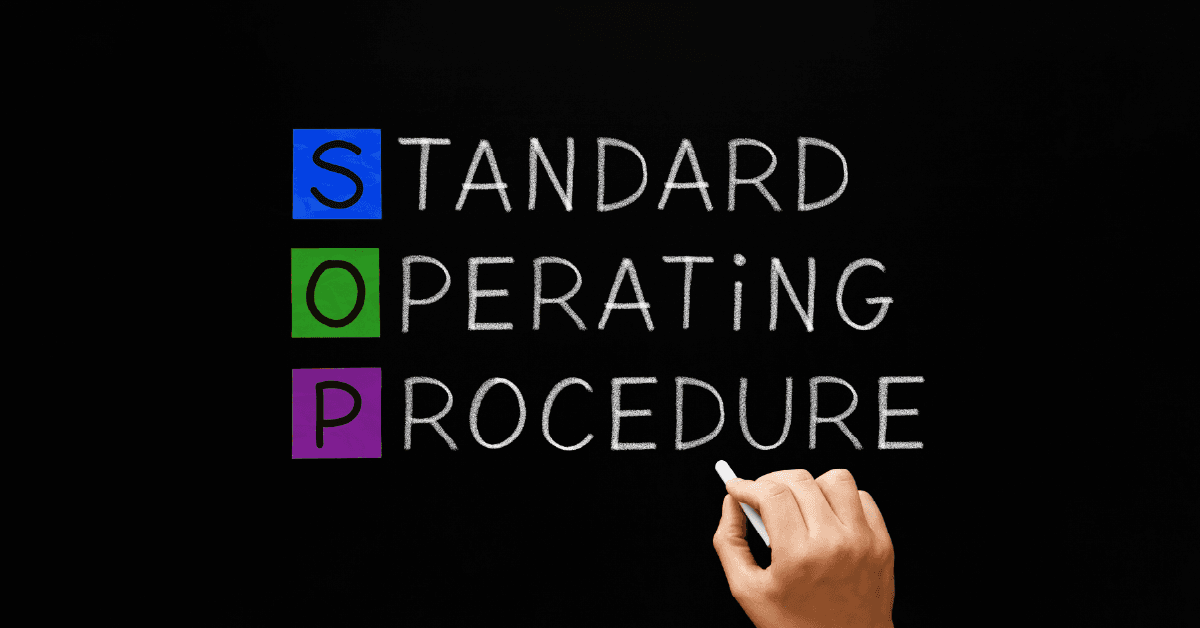
Process standardization has been the cornerstone of manufacturing for over a century, gaining prominence with the release of Henry Ford’s first Model T in 1927. Mass production based on standardized parts and processes is what enabled the development of the first assembly lines, rocketing the company to success and cementing Ford’s place in history.
That influence is seen even today, where standard operating procedures (SOPs) remain the backbone of how manufacturing organizations work. SOPs in manufacturing are a vital part of the Plan-Do-Check-Act process, laying the foundation for efficiency, productivity, profitability, and more.
This article examines why and how to create SOPs, focusing on elements such as:
- What SOPs are and what they cover
- Benefits of creating manufacturing SOPs and risks of noncompliance
- Essential steps in creating SOPs
- Using technology to digitize SOPs and verify process adherence
Download a free whitepaper to learn Why and How Digital Safety Inspections Help Manufacturers Work Safer
What Are Manufacturing SOPs?
Manufacturing SOPs are step-by-step instructions that document protocols and best practices for performing specific manufacturing tasks and organizational processes. SOPs act as a reference tool for employees, providing a basis for process standardization that ensures quality and safety. A manufacturing SOP should state not just what to do and how to do it, but also why it’s important to the process.
Manufacturing SOPs and the Plan-Do-Check-Act Process
SOPs are part of the Plan step in the Plan-Do-Check-Act (PCDA) process approach used across manufacturing. The general PDCA framework is as follows:
- Plan: This phase focuses on documenting processes, both in terms of specific manufacturing procedures as well as quality and safety management processes as a whole.
- Do: Here is where you execute the processes defined in the Plan step. This includes not just manufacturing processes, but also quality processes like advanced product quality planning (APQP), failure mode and effects analysis (FMEA) and control plans.
- Check: Whereas in the Plan phase you say what you’re going to do, at this step you check that you are doing what you say. For example, a quality system audit looks at whether you’re following your stated SOPs for quality management processes, while layered process audits look at adherence to manufacturing SOPs.
- Act: This phase centers on making adjustments based on findings from the Check step, and is critical to promoting continuous improvement throughout the organization.
It’s worth noting that global management standards like ISO 9001, ISO 14001 and ISO 45001 are also built around PDCA, requiring manufacturers to document a wide range of processes. These include product design and development, production, corrective action, and internal audits.
SOP Types and Formats
SOPs take a variety of formats and can be can be created for any process used in an organization, including:
- Work instructions and maintenance procedures for frontline workers
- Administrative processes like onboarding, training, and HR procedures
- Quality management processes such as corrective action, inspections, and layered process audits
- General safety procedures such as chemical spill procedures, emergency response planning, or Covid safety precautions
- Processes that manufacturing supervisors and managers are required to execute
The most common format for an SOP is a checklist. These checklists may be arranged hierarchically, with detailed sub-steps listed under a smaller number of main steps. In other cases, manufacturers use a flowchart SOP format to map out procedures with multiple outcomes.
Technical vs. Management SOPs
Some SOPs in manufacturing focus on technical processes, while others focus on management processes. Whereas operator work instructions typically cover one segment of an assembly or production cycle, a supervisor or manager might have SOPs covering a specific period of time.
For example, a supervisor might have an SOP that says they must:
- Review timecards daily
- Conduct a layered process audit
- Perform disposition of any scrap parts
- Attend the daily production meeting
Each of these, in turn, may have a defined process on how to complete these tasks. For instance, the layered process audit SOP would cover steps such as where to find or download the audit checklist, how to submit results, and reaction plans for nonconformances.
Common Components of SOPs
SOP format varies from one organization to the next. However, it typically includes the following components:
- Objective: SOPs should start with a clear objective defining the purpose and intended outcome of the process. This gives employees context for better understanding goals and expectations.
- Scope: This section delineates the boundaries of the SOP, including which tasks and processes it covers, so that employees know when the SOP applies to them.
- Responsibilities: This section specifies the responsibilities of those involved in the process. For example, work instructions may apply to operators, while other SOPs may involve approvals of other team members at different stages.
- Materials, tools and equipment: SOPs should include a list of the tools, materials, and equipment required to carry out the process. These process inputs have a direct impact on quality, so it’s important to ensure employees have everything they need to do the job right.
- Process steps: The meat of the SOP is detailed, step-by-step instructions on what steps to do, how to complete them, and why they are important.
- Safety guidelines: SOPs should include any applicable safety procedures such as personal protective equipment (PPE) use, hazardous material handling guidelines, or lockout/tagout procedures.
- Troubleshooting guidance: SOPs can include troubleshooting tips for common issues identified at various steps, helping reduce defects and keep the process running smoothly.
- Documentation requirements: If there are any specific record-keeping requirements or data capture associated with the procedure, the SOP should specify this.
How SOPs Are Used
Organizations use SOPs for a variety of purposes related to process standardization, including to:
- Document processes in alignment with regulatory and/or ISO requirements
- Train and onboard new employees
- Incorporate key elements of other quality processes such as control plans and FMEAs
- Provide a standard to audit against during checks like inspections, process audits, or quality system audits
- Support root cause analysis investigations, problem-solving, and corrective action processes
Importance of Manufacturing SOPs
Robust SOPs are essential to manufacturing quality and safety, providing a range of benefits that promote operational excellence. Below we discuss some of the main benefits of developing SOPs as they relate to:
- Process standardization
- Improved communication
- Regulatory compliance
- Quality management
- Employee safety
- Accountability
- Documenting institutional knowledge
- Productivity
Process Standardization
Process standardization is the principal goal of creating SOPs, ensuring all workers complete the same steps the same way. This is what allows for efficiency and consistent quality in manufacturing, which in turn promotes maximum productivity.
Creating strong SOPs is key to minimizing process variation that causes defects, customer satisfaction issues, and associated production slowdowns.
Improved Communication
SOPs help improve communication by setting forth clear expectations for how team members should perform certain processes.
Done right, SOPs give workers confidence that they are doing their jobs well and meeting management expectations. Without SOPs, many workers may just rely on their own intuition and/or shortcuts, leaving them in the dark as to whether or not their work is being done right.
SOPs such as work instructions can also be used communicate the most critical steps in a process, highlighting certain steps that matter most to quality or safety.
Finally, SOPs are critical to communicating important changes to your team. If a production process is changed, the updated work instructions should emphasize the recent change to bring it to the operator’s attention.
Compliance
SOPs help ensure compliance by incorporating steps needed to comply with regulations as well as standard requirements. This helps companies meet their compliance obligations and avoid fines and external audit findings.
In creating maintenance SOPs, for example, organizations should reference applicable OSHA standards, for example lockout/tagout requirements for preventing the release of hazardous energy.
In areas like food manufacturing, SOPs should take into account FDA regulations such as those related to hazard analysis and critical control point (HACCP) plans. Procedures outlined in work instructions for individual processes should align with critical control points and checks identified in the HACCP plan.
Beyond regulatory compliance, documenting SOPs is also a requirement under many global management standards, including ISO 9001, ISO 14001 and ISO 45001.
Quality Management
Quality management involves a range of activities such as creating control plans and failure mode and effects analysis (FMEA). SOPs such as work instructions ensure the planning done in those activities gets translated into defect prevention measures on the plant floor.
Moreover, manufacturing SOPs play a pivotal role in quality management by minimizing process variation. Any variation introduced into the manufacturing process can lead to variation in the output or product, which quality management is aimed at eliminating.
Employee Safety
SOPs help reduce workplace injuries and create a culture of safety by giving frontline workers the information they need to work safely, including:
- Which type of PPE to use and how to wear it
- How to handle any hazardous materials in the process
- High-risk steps where extra caution is needed, such as those identified during job safety analysis (JSA)
- What to do in the event of an emergency
Incorporating safety guidelines into SOPs is especially important from a training perspective, as a large proportion of workplace injuries happen to workers in their first year on the job. Remember that new workers may be unfamiliar with your processes and unaccustomed to following certain safety protocols in executing them.
Accountability
SOPs provide a baseline for ensuring accountability from the entire team. They do this by giving you a standard to audit or inspect against, such as when conducting safety inspections or layered process audits.
This starts with creating checklists. As you build your checklists, SOPs provide a crucial reference, designing questions around SOP elements critical to safety or quality. When a noncompliance is identified during a check, auditors have a specific standard to point to that operators should be following.
Documenting Institutional Knowledge
As a generation of experienced workers retire, manufacturers are at risk of losing valuable institutional knowledge that keep operations running smoothly. By creating SOPs, however, manufacturers can capture and codify this institutional knowledge and transform it into actionable practices. Read more about good manufacturing practices (GMP).
This means that critical knowledge becomes embedded into documented procedures instead of being lost when workers leave. Ultimately, this helps safeguard companies against knowledge gaps and mitigate the challenges of the manufacturing skills shortage.
Productivity
Establishing SOPs contributes to productivity in a variety of ways, including by:
- Minimizing errors that slow down the production process
- Providing a reference point for employees that reduces the need to spend time looking for information
- Facilitating training and onboarding to shorten the learning curve and get new workers productive faster
- Helping identify and eliminate bottlenecks in the process, leading to greater efficiency
- Standardizing machine setup, maintenance and troubleshooting to reduce downtime and optimize resource use
Keeping SOPs updated also fosters continuous improvement as processes become increasingly streamlined and efficient—and thus more productive—over time.
Risks of Not Complying with SOPs
Noncompliance with SOPs creates a number of problems for manufacturers ranging from quality control issues to safety incidents. Noncompliance isn’t always deliberate, such as when someone forgets to do a step recently added to the manufacturing process.
The key is to make sure you have checks in place, ranging from quality system audits down to daily process audits to ensure you don’t just say what you do in your SOPs, but also that you do what you say in your SOPs.
Quality Control Issues
SOP compliance has a direct effect on quality control, making sure operators follow work instructions and that quality processes are held in place.
Let’s look at a few examples:
- When operators don’t comply with SOPs such as work instructions, defects can occur, leading to increased complaints and quality costs.
- If maintenance SOPs aren’t followed, unexpected and costly equipment downtime can occur.
- If supervisors don’t follow an SOP on disposition of scrap parts, there’s a risk those parts could get shipped to the customer.
Lower Productivity
Variation in processes reduces productivity in several ways. First, it leads to defects that require resources to fix through corrective action. Noncompliance with SOPs can also mean more downtime from machine issues and having to devote production capacity to fixing problems. With less variation, those resources and production capacity go towards creating products that generate revenue.
What’s more, equipment downtime and process bottlenecks also reduce overall equipment effectiveness (OEE), which contributes directly to productivity in a plant.
Increased Waste
Variation from SOPs leads to waste, and not just in terms of scrap rate. Noncompliance with SOPs drives up the three categories of waste in Lean, termed the 3Ms:
- Muda: Muda represents activities that don’t add value to the process. Eliminating these activities frees up capacity for value-added work.
- Mura: Mura, or “unevenness” in Japanese, causes excess capacity at certain times and the need to rush at other times.
- Muri: Muri, or “overburden,” references added stress on workers and processes due to inefficiency.
Safety Risks
Noncompliance with SOPs increases safety risks and can ultimately lead to workplace injuries. A few examples:
- If a worker fails to follow SOPs around safety guards or lockout/tagout procedures, the worker’s hand may be caught in the machine
- If an operator doesn’t wear the right PPE, they can be exposed to flying debris or hazardous chemicals
- Mishandling hazardous materials may lead to spills, fires, or exposures
How to Create a Manufacturing SOP
As the old saying goes, garbage in means garbage out. That is, if you communicate poor standards to people, the output will necessarily be subpar. The following steps, discussed in more detail below, can help make sure you build strong SOPs:
- Define the scope
- Determine your goal
- Create a process flow map
- List each step
- Review and improve
1. Define the Scope and Responsibilities
Your first step is to define the scope of your SOP, which sets the boundaries it will cover. This includes:
- What processes and activities are covered by the SOP
- Which equipment it applies to
- Who is responsible for following the SOP
2. Determine Your Goal
Next, you need to determine your goal in creating the SOP by asking yourself what you’re trying to achieve. Whether it’s to improve quality, efficiency, or compliance, a clear purpose acts as a guiding star for measuring success, prioritizing resources and engaging employees.
Communicating the ‘why’ to employees is crucial to engaging people’s hearts and minds, gaining their buy-in so they are more likely to follow the SOP. If you don’t, they might do the procedure correctly ten times but get it wrong on the eleventh time, thinking it’s no big deal.
3. Create a Process Flow Map
Once you’ve determined the goal and scope of your SOP, you next need to create a process map of what you want to see happen in the work cell. As you go through this step, look for ways the procedure could be done wrong and ways to eliminate them.
Here you need to document each step, including:
- What to do
- How to do it
- Why it is important
From a best-practice perspective, the format of your SOP should emphasize images over words. You want people to be able to visualize what to do quickly, not have to read paragraphs. Manufacturers must also recognize that their workforce may have limited literacy and English capabilities, making it necessary to put images at the center of your SOPs.
Finally, you should ensure that SOPs are aligned with process FMEAs (PFMEAs) and the control plan. For example, prevention steps such as visual or gauge checks in the FMEA should be included, as should control plan elements such as red rabbit or error-proofing checks.
4. Review and Improvement
Manufacturers must review SOPs periodically to ensure they’re updated and reflect current knowledge of best practices. Review frequency varies depending on the organization, however a good rule of thumb is to make sure you’re reviewing them at least once every year.
SOPs should also be reviewed anytime there is a layered process audit finding or a customer quality notice. It’s important to ask operators where people are likely to be confused by the SOP, and if any words need to be changed for clarity. This can help identify areas where the SOP has gaps or is unclear, helping prevent similar occurrences in the future.
Who Should Be Involved in Creating SOPs?
Manufacturing or process engineers are typically those responsible for writing SOPs such as work instructions. However, it’s important that quality and operations have a chance to contribute after engineering has developed the first draft.
Quality engineers may have input on inspection steps or other control plan items that work instructions must include. Operations can also help identify where work instructions are impractical or dangerous.
For example, operators may highlight part of the SOP that requires them do to a blind install of a bolt on an assembly line, increasing the chance of missing that step.
Why Plants Are Digitizing SOPs
Plants are increasingly using solutions such as connected worker software to digitize work instructions. This is for several reasons:
- Easy access to work instructions: Connected worker platforms make digital SOPs like work instructions available at the point of use, providing real-time reminders where workers need it most.
- Streamlined tracking and version control: Digital SOPs are easier to track and keep updated, which helps eliminate versioning problems so you know people are always using the most up-to-date procedure.
- Faster training and onboarding: Digital SOPs can be easily accessed by new employees, with the level of detail customized to the operator’s certification level.
Using Mobile Process Audits to Verify SOP Adherence
There are major risks to not complying with SOPs, making it essential to verify that people are following them on the plant floor. High frequency checks such as layered process audits are particularly effective at verifying adherence to core SOP requirements to minimize defects, compliance issues and costs.
More and more, companies are using plant floor audit and inspection software to streamline the process and collect data for driving continuous improvement.
Plant floor audit and inspection software like EASE makes it possible to:
- Schedule a large number of audits or inspections in minutes
- Customize and update the question library to reflect changes in SOPs
- Rotate and randomize questions on checklists to ensure broad coverage of SOPs
- Complete audits using a mobile device and get instant visibility into SOP noncompliance
- Document findings and ensure follow-up such as assigning additional training on SOPs
Overall, this type of software helps execute a larger number of checks with ease, while offering data and insights on noncompliance trends and issues.
At the end of the day, it’s important to remember that SOPs can’t cover everything. You have to build a robust process that the SOP supports. If the operator can do a hundred things wrong, just telling them to do the one right thing isn’t going to result in a strong process.
Instead, you need to look at the process and eliminate as many opportunities for errors as possible. Once you have, SOPs and plant floor checks keep your team on the right track, so everyone is pulling in the same direction to deliver a consistent product.