Understanding the 6Ms of Process Control
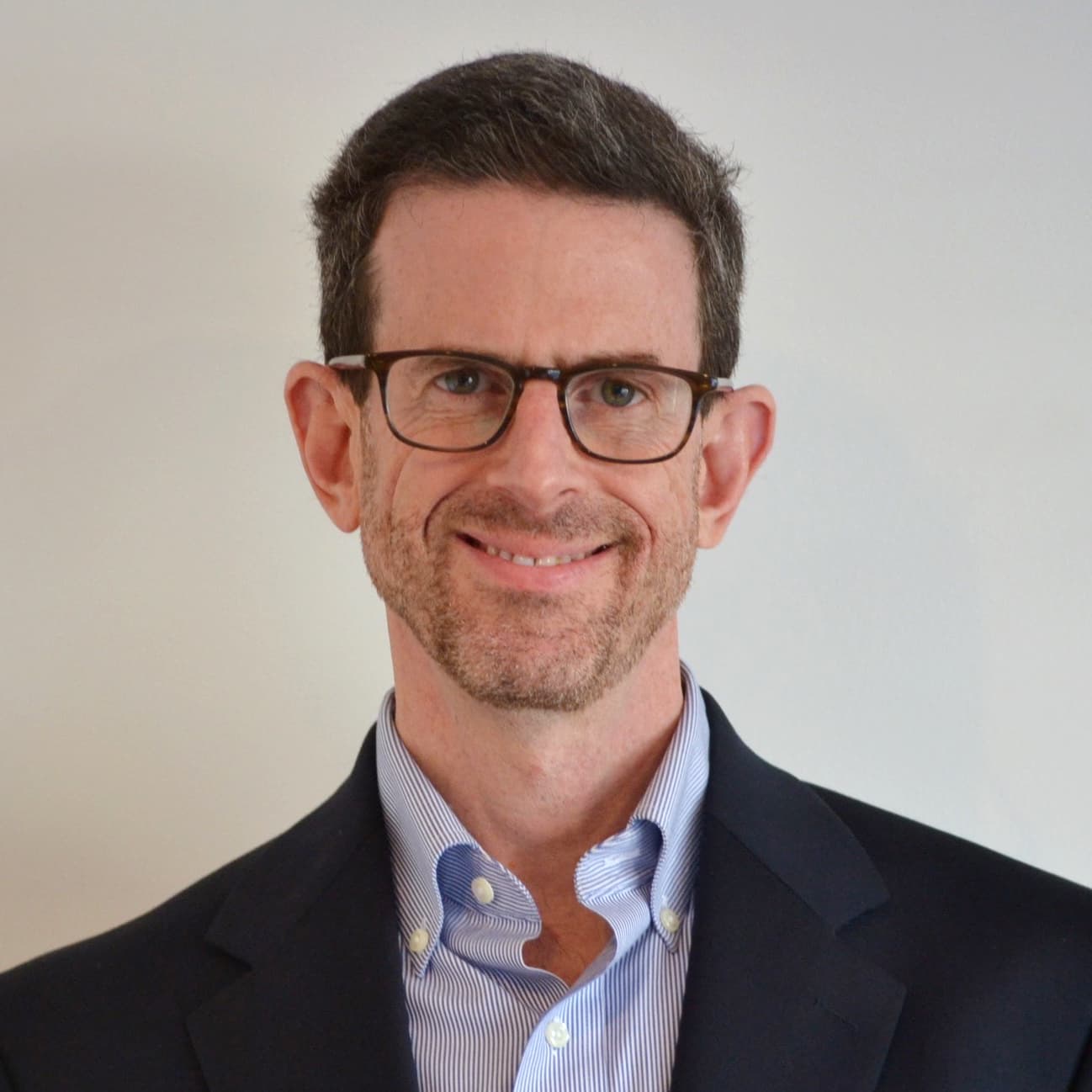
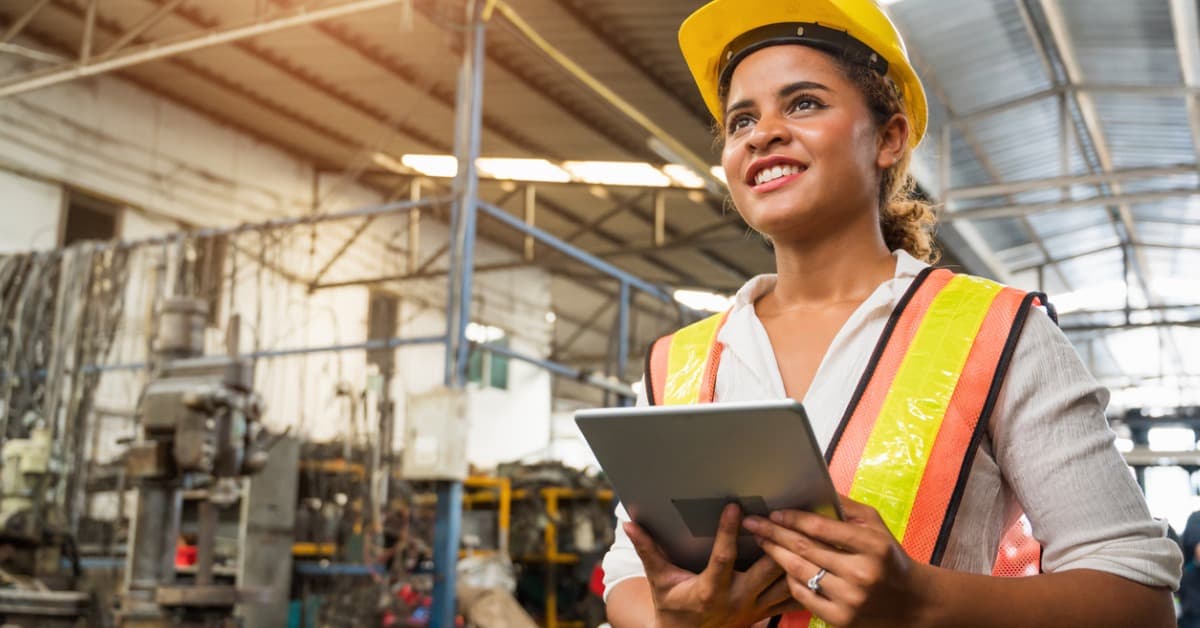
An Ishikawa or fishbone diagram is a tool commonly used to brainstorm potential causes as part of a problem-solving process. At the head of the fish is the problem, while each bone represents a category of contributing factors.
These categories are based on the 6Ms of process control, also called the 6Ms of production or problem-solving.
Here we break down the 6Ms, plus a technique we use at The Luminous Group for using this tool to go beyond root cause analysis to foster process excellence.
Download your free Ultimate Guide to Layered Process Audits for a powerful strategy to reduce defects, complaints and quality costs
What Are the 6Ms?
The 6Ms of process control are a framework for categorizing process inputs that could be causes of a quality problem. When variation exists in these process inputs, quality problems are more likely to occur. When the 6Ms of a process are stable as intended, quality issues can be prevented. The 6Ms are:
- Man (People)
- Machine
- Method
- Mother Nature (Environment)
- Material
- Measurement
1. Man (People)
This category refers to variation in human behavior, whether it’s variation in worker behavior over time or different techniques used among multiple people. For example, two people using the same work method may perform a process differently if one is tired, works too fast, gets distracted or had different training.
2. Machine
Machine refers to variation in equipment operation. For instance, perhaps due to normal wear and tear on a machine, it no longer drills a hole in a part where it should be.
3. Method
Variation in methods themselves shouldn’t typically occur once you have the procedure documented. Variation in how operators perform methods would be categorized under People.
In some cases, methods can vary when different work instructions are used to create similar parts for different clients. This situation would warrant considering whether operators are using the right method or were provided with sufficient training to be competent.
4. Mother Nature (Environment)
Environmental conditions can affect equipment performance as well as the stability of raw materials, making it an important source of variation to consider when evaluating quality problems. For example, high temperatures in the work area can cause distortion in some parts. Polymer pellets are also a good example, where high or low humidity can impact the drying process.
5. Material
While manufacturers expect raw materials to conform to requirements, supplier-related quality issues are common and should be evaluated during the problem-solving process. Material-related variation can happen, for example, if a product is labeled incorrectly, or if the incorrect parts or material were brought to the assembly line, or if the supplier has a known history of quality issues.
6. Measurement
Variation in measurements includes how measurements are taken as well as the accuracy of measurement equipment. For instance, if a gauge isn’t in good condition, it might not provide the right value. This makes it difficult to spot non-conforming parts or even make conforming parts appear as suspect or scrap.
The 7th M: Management
One final M that manufacturers are starting to incorporate into their problem-solving processes is management. In some instances, management can unintentionally cause unwanted variation, or cause a problem via omitting a needed action.
For example, let’s say during a 5 Whys analysis that you find out a machine wasn’t maintained properly because you’ve lost two operators and management hasn’t hired replacements. In this case, management not meeting its responsibility is the contributing factor that needs to be addressed.
Using the 6Ms to Define What Needs to Go Right
While the 6Ms are typically used in the context of root cause analysis, manufacturers can also use them to define what needs to be done right. Consider what would happen, for instance, if elements from each of the 6Ms are slightly off, but not out of conformance. Maybe the machine is a little worn and not advancing fully, or the operator is slightly off in how they load the part. All it takes is slightly more variation or a stack-up of variation factors to cause a quality problem.
The 6Ms can help you think about how you can drive all of that variation to zero, helping improve metrics such as defective parts per million (DPPM) and first-pass yield (FPY). Proactive companies take time to research and define these conditions, rather than just reacting to problems.
Running what-if scenarios can be helpful here, such as asking what happens if an operator retires. What elements must you check to make sure the new employee is doing the right things to prevent variation? Another powerful what-if is to ask what has to be done or checked after a power brown-out or power disruption. It’s better to have a contingency plan in your back pocket than to scramble after the customer files a complaint.
The 6Ms are a useful tool for exploring the cause of a problem, as well as a proactive planning tool for defining the conditions required for process excellence. Know that the 6Ms aren’t always cut and dried, so you don’t want to get hung up on which category a cause goes into. The important thing is to have a conversation about it with the people closest to the job, so you can create controls to prevent it and build layered process audit questions to verify your most risky 6M factors.