Why the Cost of Quality Goes Beyond Fixing Manufacturing Failures
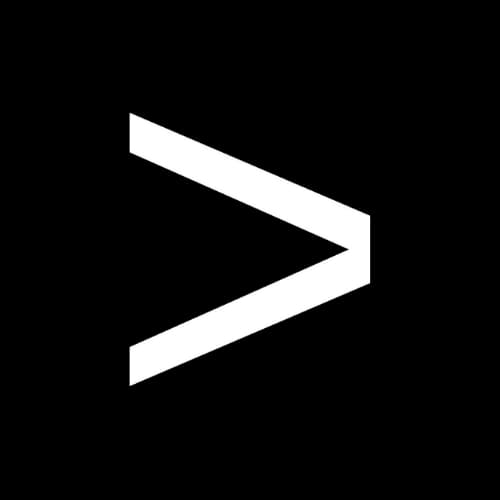
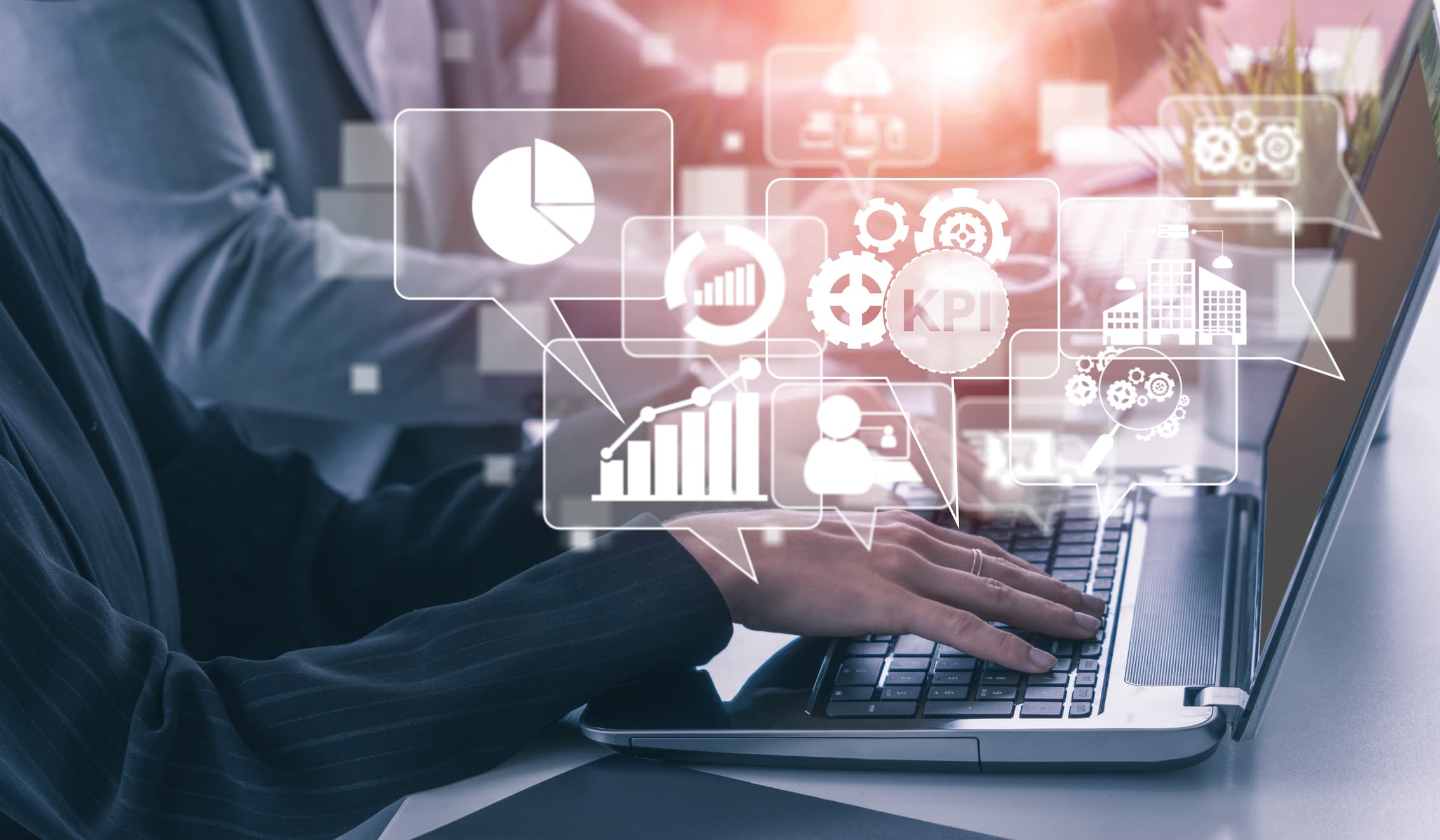
Research studies show that manufacturers estimate their cost of quality at approximately 10 percent of revenues, while, in reality, that figure is double that at 20 percent. While statistics like this are eye catching, it’s important to understand what is meant by the term, cost of quality. Unfortunately, it’s a widely misunderstood concept. Many organizations view the cost of quality solely in reference to failure costs. Common examples of activities related to this line of thinking include:
- Rework
- Scrap
- Returned materials
- Warranty recalls
In truth, any cost that your organization would not have expended if quality were perfect contributes to the cost of quality. The true cost of quality, therefore, certainly extends beyond manufacturing failures to expenses related to the cost of conformance or what is called the cost of good quality. Example of expenditures associated with the cost of good quality include:
- Preventing a nonconformance to customer or regulatory requirements
- Auditing the conformance of products and processes to requirements
Prevention Costs/Cost of Good Quality
Prevention costs are incurred through activities that your organization carries out to prevent poor quality in its products or services. This can also be thought of as the costs incurred to keep failure and appraisal/auditing costs to a minimum by preventing failures before they happen. Some examples of prevention costs might include:
- Quality improvement projects
- Reviews of your new products
- Supplier capability surveys
- Evaluations of process capability
- Education and training centered on quality tools and methodologies
Appraisal/Auditing Costs/Cost of Good Quality
In contrast, auditing costs are associated with measuring, evaluating, or auditing your products to assure that they conform to various quality standards, such as ISO 9001 or other customer requirements. Examples of auditing costs would be:
- Conducting product, layered process audits, or service audits
- Supplier quality audits for incoming products
- Performing in-process and final inspection/tests
- Calibrating measurement and test equipment
The time and expense involved with auditing activities can be a major burden today, but the advantages gained by completing layered process audits is significant as these routine audits provide valuable insight into trends of where processes break down and how such instances can be corrected. Data gathered through layered process audits also yield valuable suggestions for what you should change as well as statistics for further planning and analysis.
Many leading manufacturers that have historically used paper to complete audits are now turning to technology to streamline these important tasks. New software options offer real-time data, which allows you to work proactively on potential issues instead of just reacting to problems. Automated reporting options are available so that you have visibility into process performance across the company. Look for intuitive products that help you implement greater quality and efficiency in your organization for improved cost savings and resource utilization.
Failure Costs/Cost of Poor Quality
This type of cost results from products that are out of spec to customer work orders. Failure costs are further divided into internal and external failure categories. Internal failure costs primarily involve scrap and rework and are typically caused by issues linked to product defects, disruptions in schedules, material shortages, excessive downtime with equipment, and product redesigns. Using simple Six Sigma tools, such as the 5 Whys method, can help you uncover the root causes of these types of process failure and, therefore, reduce your internal failure costs.
In contrast, external failure costs center on returned products as well as recalls and warranty expenses. These occur after your product is shipped to the customer and are most likely caused by poor communication, unresolved complaints, and noncompliance with standards.
Totaling Your Cost of Quality
To calculate your true cost of quality, simply total the costs listed in the prevention, auditing, and failure (both internal and external) categories. This number will show you the difference between the actual cost of a product or service and what the reduced cost would be if there were no possibility of substandard service, failure of products, or manufacturing defects.
Almost every organization realizes that anything less than the highest quality is not an option. High quality is simply an entry ticket for the opportunity to compete or exist. Attaining high quality at the lowest possible cost is imperative. By reducing the cost of quality in your organization you are also protecting and enhancing your products’ quality reputation and, at the same time, increasing customer satisfaction.
What are some of the best methods you have found for reducing your cost of quality?