How to Implement Corrective Actions That Stick
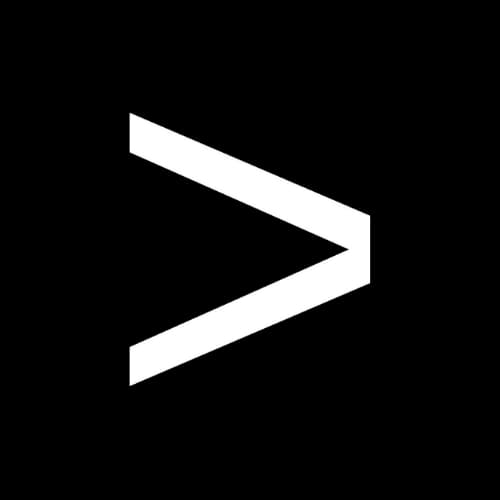

Many manufacturers struggle to implement corrective actions that truly prevent issues from recurring. While digital tools offer promising solutions, organizations often aren’t sure where to begin.
This article provides a practical framework for strengthening quality management systems and ensuring ISO 9001:2015 compliance through effective corrective actions, from root cause analysis to digital implementation.
Root Cause Analysis and Corrective Actions Defined
Root cause analysis (RCA) and corrective actions form the backbone of quality improvement in manufacturing. While quality defects carry monetary costs and far-reaching consequences, implementing effective solutions remains challenging for many organizations.
RCA and corrective actions serve three critical functions:
- Identifying and eliminating defects
- Preventing workplace safety incidents
- Reducing operational waste through targeted problem-solving
ISO 9001:2015 clause 10.2 mandates this approach, requiring organizations to not only correct nonconformities but also eliminate root causes and verify the effectiveness of their actions.
A Robust RCA and Corrective Action Plan in 6 Steps
A comprehensive root cause analysis and corrective action plan involves:
1. Problem Definition | Clear description of the issue and its impact |
2. Root Cause Analysis | Documented review findings |
3. Corrective Actions | Specific steps to address root causes |
4. Implementation Timeline | Clear deadlines and milestones |
5. Responsibility Assignment | Designated owners for each action |
6. Validation Criteria | Metrics to verify effectiveness |
Download your free Root Cause Analysis 101 Guide to learn the right way to use Pareto charts, the 5 Whys, and other common RCA tools.
Strategies for a More Effective Corrective Action Plan
Many organizations manage their corrective actions using a combination of spreadsheets stored on cloud-based information sharing platforms, email threads, and paper documentation.
While this approach might seem to do the job initially, it creates fundamental challenges, including version control, buried and lost information, and siloed department tracking systems. Before you know it, information gets lost, tasks get missed, and corrective actions fail to get implemented, putting your operation at risk of repeating the same issues over and over again.
These challenges highlight the need for a more structured, systematic approach to corrective actions, instead of cobbling together various tools and hoping for the best.
Make It Easier to Connect the Dots
Even the most well-designed corrective action plan can fail without proper visibility into the problem and root cause that it’s trying to correct. A full view of the issue, context, and history is often held up or hard to access because information is scattered or incomplete.
By having a centralized place for investigations, teams can find critical information quickly, capture visual evidence, prevent repeat issues, and spot patterns before they have any further impact on production.
Validate Regularly and Systematically
Validation isn’t a one-time event; it’s an ongoing process that requires systematic attention and clear metrics. Organizations often fall short by treating validation as an afterthought rather than an integral part of the corrective action process.
A structured approach combining scheduled effectiveness checks, continuous performance tracking, automated data collection, and real-time compliance monitoring ensures that improvements stick and problems don’t resurface. This systematic validation process allows teams to catch deviations early and adjust course before minor issues become major problems.
Prevent Recurrence Through On-the-job Training
The true test of any corrective action lies in its ability to prevent problems from recurring. While many organizations focus on fixing immediate issues, they often overlook the critical step of embedding these fixes into their daily operations.
When employees understand not just what to do but why they’re doing it, they become active participants in maintaining improvements rather than passive followers of procedures (or worse: expert pencil-whippers). More specifically, we’ve found that bite-sized training that’s delivered while the employee is doing the task is more likely to produce more lasting behavioral change versus traditional classroom-based education.
Effective on-the-job training can prevent recurrence by:
- Building confidence and compliance by combining hands-on practice with real-world settings, not hypothetical scenarios
- Reducing errors through targeted, contextualized training at the moment a potential problem or issue comes up—not weeks or months later
- Decreasing rework by verifying competency before new or updated processes go live
- Protecting your business with records that demonstrate due diligence to external or third-party auditors
- Ensuring lasting improvement by measuring and reinforcing knowledge retention over time
- Turning mistakes into learning opportunities and motivate employees to continuously improve
Digital Tools Sustain Corrective Actions
Although proper processes and engaged teams form the foundation of effective corrective actions, digital tools provide the framework for seamless integration, eliminating the fragmentation and visibility issues that plague traditional approaches.
Improve Team Collaboration
Modern tools revamp how teams work together on quality improvements. By providing real-time visibility and automated workflows, these digital tools:
- Cut resolution time through instant task notifications and automated follow-ups
- Strengthen quality culture through transparent performance tracking at all levels
- Enable proactive collaboration by connecting team members across departments
- Support data-driven decisions through shared access to quality metrics
Increase Efficiency with the Right Data
Digital solutions transform scattered documentation into actionable insights. Teams can find critical information in seconds, capture visual evidence that speeds up problem-solving, and spot patterns before they become problems.
Layered process audits (LPAs) play a crucial role here, providing multiple levels of verification from operators to management that corrective actions remain effective over time. By maintaining comprehensive, accessible digital verification records, LPAs help manufacturers:
- Make better decisions faster with centralized quality data
- Free up significant time by eliminating manual documentation
- Prevent recurring issues by connecting past solutions with current challenges
- Drive continuous improvement with real-time performance insights
Connect Corrective Actions to Existing Workflows
The most effective problem solving becomes part of your daily operations rather than existing as separate processes. Digital platforms make this integration natural by connecting corrective actions directly to existing workflows and making information accessible where it’s needed. You can expect to:
- Boost shop floor engagement by bringing quality tools directly to the point of use
- Save time and reduce errors by connecting quality processes to existing systems
- Ensure follow-through by automating verification and effectiveness checks
- Accelerate problem-solving with instant visibility into action status
Implementing corrective actions that stick requires combining clear processes, engaged teams, and effective digital tools. By moving beyond traditional spreadsheet-based systems, manufacturers can build stronger, more resilient operations that consistently deliver quality results.